Abstract
Content
- Introduction
- 1. The nature and content of production stocks
- 2. The procedure for documenting operations with production stocks
- 3. Production stocks of the enterprise: accounting tasks and cost management
- 3.1 Overview of research and development
- 3.2 Production inventory management
- 4. Inventory audit
- Conclusion
- References
Introduction
Production stocks (hereinafter referred to as PZ) form the basis of the economic activities of organizations and are the main link in the process of exchanging values and the results of the functioning of organizations. Accounting for the acquisition, storage and use of PP is a very important aspect of work at the enterprise. With a rapid change in the nomenclature of products, suppliers of material resources and prices for materials in the criteria of a market economy, inventory accounting becomes even more significant. The process of managing material and production stocks is complicated by their dynamic nature. The solution to this problem is the timely delivery of analytical information about the circumstances of material and production stocks to the management system of the organization. In order to have absolute information about PP, an effective mechanism for their analysis and accounting is necessary. Systematic, competent accounting of PP is the basis of effective enterprise management. Inaccessibility of reliable data on the availability and movement of inventory, as well as incorrect reflection of them in the reporting can lead to incorrect management accounting and, as a result, to losses of the organization [6].
The object of the study is the accounting and audit processes in the conditions of Bacon–Invest-Agro LLC.
The subject of the research is theoretical and organizational–practical aspects of accounting and auditing of production stocks.
The purpose of the work is to identify deficiencies in accounting, analysis and disclosure of inventory in the reporting, to improve the accounting and audit procedures of inventory, their disclosure in the reporting.
To achieve this goal , the following tasks were defined:
- to consider the theoretical foundations of accounting PP, their concept and structure;
- to study the procedure for documenting PZ and their reflection in accounting statements;
- to reveal the essence of the methodology and stages of the analysis of material and production stocks;
- to consider the organizational and economic characteristics of the organization;
- to analyze the features of accounting and analysis of PP in organizations for the production of soft drinks;
- to identify opportunities for information support of accounting and analysis of PP, and their disclosure in the financial statements;
- develop practical recommendations on the procedure for accounting and analysis of PP, their disclosure in the financial statements.
1. The nature and content of production stocks
According to the Accounting Regulations "Accounting of material and production stocks" of PBU 5/01, assets are accepted for accounting as material and production stocks:
- used as raw materials, materials, etc. in the production of products intended for sale (performance of works, provision of services);
- used for the management needs of the organization;
- intended for sale.
Inventory is a part of the current assets of the organization, i.e. a part of the property used in the cases presented in figure 1.
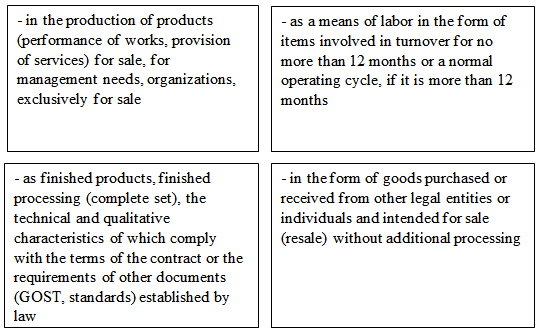
Figure 1 – Use cases of inventory
The material basis of the product is raw materials and basic materials. Raw materials are called products of agriculture and the extractive industry. Materials are called products of the manufacturing (processing) industry. The nomenclature number is the accounting unit of the MPZ. It is developed in the context of each name or homogeneous groups of stocks. Materials are material elements that are acquired for the purpose of further use in the production process as objects of labor. Materials are completely consumed in the production cycle and, therefore, completely transfer their value to the cost of production products or services rendered.
According to the method of use and purpose in the production process , materials are divided into types (figure 2).
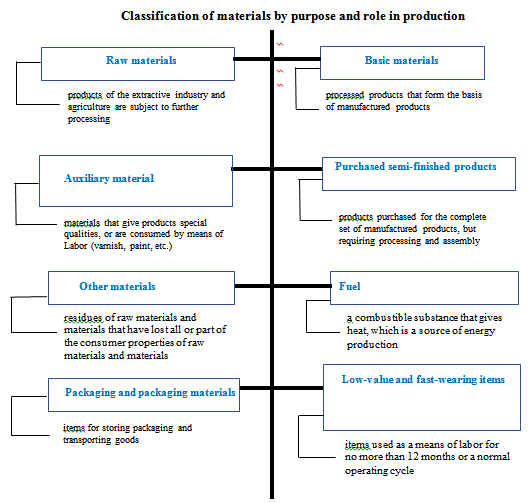
Figure 2 – Classification of materials by purpose and role in production
A group of inventories is a set of inventories with similar characteristics, information about which is disclosed in accounting (financial) statements by one indicator. In accordance with the FSB "Stocks", the main groups of inventories are: items used in the current activities of the accounting entity for a period not exceeding 12 months, regardless of their value, as well as items intended to provide social support measures for certain categories of citizens in order to exercise the transferred state powers established by the legislation of the Russian Federation; finished products, biological products; goods for sale; other tangible assets, regardless of their value and service life, established by separate regulatory legal acts of the Ministry of Finance of the Russian Federation. The materials can be divided into:
- main;
- auxiliary.
This division is determined by the peculiarities of technology and organization of production. The group of basic materials includes:
- purchased semi-finished products;
- accessories;
- production inventory [5].
Returnable waste is the remnants of materials that have completely or partially lost the consumer properties of raw materials and materials that can later be used as raw materials for other products. Auxiliary materials are used to influence raw materials and basic materials and to give the product certain consumer qualities (for example, varnishes and paints for cars, pepper and other spices in sausage production) or to maintain and care for tools and facilitate the production process, as well as to facilitate the production process.
Auxiliary materials include:
- fuels and lubricants;
- containers and packaging materials;
- spare parts.
Fuel (fuel), depending on the application, is divided into technological (for technical purposes), motor (for refueling vehicles) and economic (for heating work areas). The container is intended for packaging, transportation, storage of materials and products. Spare parts are used to replace worn-out components and parts of machinery and equipment. Inventory and household supplies are a part of the organization's MPZ, used as a means of labor for no more than 12 months or a normal operating cycle. Labor products in the form of stocks of finished products and goods subject to sale or resale without additional processing are allocated to independent groups. The goods are part of the MPZ purchased or received from other legal entities or individuals and intended for sale [1].
2. The procedure for documenting operations with production stocks
All business operations carried out by the enterprise must necessarily be executed with exculpatory documents. These documents serve as primary accounting documents, on the basis of which accounting is conducted. "In accordance with Federal Law No. 402-FZ of December 6, 2011 "On Accounting", every fact of economic life is subject to registration as a primary accounting document. The forms of these documents are approved by the head upon presentation of the official who keeps accounting records. Registration and accounting of business transactions takes place using unified forms of primary reporting.
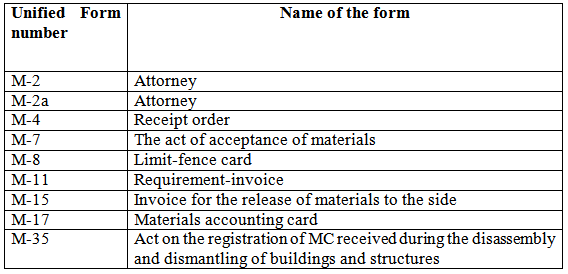
When purchasing MPZ, the supply departments of organizations receive external registration documents from suppliers: invoices and payment requirements, as well as shipping documents (waybills (Form No. 1-T)), which serve as the basis for acceptance and acceptance of materials for accounting. Powers of attorney (forms no. M-2 and no. M-2a) are used to ensure that an employee has the right to act as a trustee of the organization when receiving valuables released by the supplier. Form No. M-2a is used by organizations that receive tangible assets by proxy in large volumes and regularly. It is usually issued for a period of 15 days. Acceptance and registration of incoming materials is made out in warehouses, while a receipt order of form No. M-4 is necessarily drawn up. It is written out for the actually accepted amount of materials.
The main point of use of MPZ is their release for the production of products. This happens based on pre-set limits. "The limits are set in accordance with the norms of material consumption, which were developed by the relevant services of the organization, taking into account the remaining materials at the beginning and end of the year" [3]. Limit-fence cards are the most common expenditure documents. They serve for the release of materials, for the purpose of manufacturing products, current control over compliance with limits and are a document authorizing their write-off from the warehouse. They also keep records of materials that were not used in the production process. The transfer of MPZ from one warehouse to another warehouse is made out by drawing up a requirement-an invoice for the internal movement of materials (form no. M-11). With the help of the same documents, an operation is carried out to transfer the remnants from the production of unused materials to the warehouse, if they were received on demand, as well as the delivery of waste and valuables received in case of marriage.
In preparation for the inventory of the MPZ, an inventory of property is compiled, documents and the actual availability of materials are checked. It is produced by a continuous method: all goods and valuables are recalculated without any exceptions. The values that were received during the inventory inventory at the enterprise are accounted for in the presence of the commission. The fact is recorded in the register or commodity report, and then documented in the inventory "Inventory items received during the inventory". The property of the organization is weighed, recalculated by the commission. The results are recorded in the inventory inventories. The volume or weight of materials during the inventory of MPZ is determined using a technical calculation based on measurement data. Based on the results of the actual inventory of stocks, the commission fills out acts and inventories. Their difference is that the inventory records the results of the material inspection, the act – the documentary inventory. If a discrepancy between data and information has been revealed, comparison statements are filled in. They take into account the re-grading and cost differences. The deficiencies of the MPZ identified during the inventory are written off on the date of the audit. The cost of MPZ shortages is written off for costs associated with production or sales, taking into account the norms of natural loss [6].
3. Production stocks of the enterprise
3.1 Research and Development overview
The work of a large number of Russian and foreign researchers is devoted to the study of the tasks of organizing accounting and analysis of production stocks at enterprises. Such scientists as: Kruglyak Z. I., Kalinskaya M. V. [7], Basalaeva E.V. [8] and others made a significant contribution to aspects of the theory and practice of inventory accounting. Among the foreign researchers, it is necessary to single out the scientific works of such scientists as: Needles B., Anderson X, Caldwell D. [9], etc.
3.2 Production inventory management
The main element of any production process are stocks, which are the most important management factor in the enterprise. However, at present, due attention is not paid to the inventory management system at the enterprise.
The acquisition (creation) and maintenance of stocks entails certain costs, which very often exceed the cost of the stocks themselves. Therefore, each manager tries to minimize the amount of these expenses and at the same time leave the level of customer service that satisfies them.
Investing in business development, every entrepreneur wants to get the maximum return on investment. Since stocks are also investments, it is necessary that they be optimal, i.e. invested in the right stocks, as well as at the right time, in a certain amount, etc. Insufficient or excessive inventory of material values in the enterprise leads to loss of profit - from under-sale or from sale with discounts [5].
Recently, enterprises have been paying attention to the remaining stocks in the warehouse, which lose their value and actually freeze the funds invested in them. Given the insufficiency of working capital and credit sources, most enterprises today seek to reduce all inventories, thereby increasing payback. However, the purpose of the business is to earn more by offering customers a "marketable" product, and not to sell stale stocks for the sake of profit. Therefore, it is necessary to calculate a certain amount of inventory, as well as to understand how much potential profit is lost when there is none.
For effective inventory management, the company must:
- Determine the list of necessary stocks.
- Ensure the availability of the necessary stocks in the warehouse in a specific period of time.
- Determine the losses from the lack of stock in the warehouse.
- Determine the turnover of stocks, that is, the time during which they are stored in the warehouse, and the "fate" of illiquid funds invested in stocks.
- The proposed measures will allow the company to make decisions on the change of suppliers or distributors, update the range of stocks, etc.
- The level of stocks in a certain way also depends on consumer demand for a particular finished product. In order to meet the demand, it is necessary to have a certain stock of material resources. In accordance with the division of demand into dependent and independent, the following inventory management systems can be distinguished: a system with a fixed order size and a system with a fixed delivery interval [6].
- The system with a fixed order size is the simplest and most common. It provides for control over the level of stocks in the warehouse of the enterprise. When the quantity of stocks becomes below the required level, an order for replenishment of stocks is issued. The advantage of this system is that there is constant control over the level of stocks.
- In a system with a fixed delivery interval, the size of the stock at the enterprise is regulated by changing the volume of the batch of orders. The disadvantage of this system is that additional costs arise if there are no stocks at a particular time.
- Therefore, for effective inventory management, it is necessary to determine in advance the quantity of products ordered and the timing of orders, which will satisfy demand through:
- one-time creation of a stock for the entire required period of time;
- creating the necessary stock for each time period [2].
4. Audit of production stocks
It is advisable to carry out an audit of production stocks with an inventory or with a study of the inventory already carried out at the enterprise. At the same time, the auditor examines the following issues:
- organization of the conclusion of a contract with suppliers of production stocks;
- the structure of these agreements;
- terms of delivery, payment, stipulated penalties for violation of the terms of the contract.
The objects of the audit of tangible assets are:
- acceptance of material values in terms of quantity and quality;
- storage of material assets;
- consumption rates in production;
- accounting of operations on the movement of material assets;
- reporting;
- primary documentation;
- MBP movement operations.
The main errors that occur when checking these audit objects are:
- addition of inventory items to the inventory inventory;
- understatement of balances on individual analytical accounts;
- implementation of so-called other materials;
- deliberate overestimation of prices during the sale of production stocks;
- incorrect determination of the initial cost of production stocks [10].
Conclusion
Summing up, we can say that the main task of inventory accounting is to control the security and efficiency of their use, the correct assessment of the movement of inventory. It is very important to timely convey information about the state of material and production stocks to the management system of the enterprise. Since this greatly affects the efficiency of enterprise management.
References
- Сначев Н.П. Оптимизация запасов предприятия [Электронный ресурс] Режим доступа: http://cyberleninka.ru/article/n/optimizatsiya-zapasov-predpriyatiya
- Кодацкий В.П. Пути эффективного управления оборотными активами промышленных предприятий В.П. Кодацкий // Актуальные проблемы экономики. - 2013. - № 4. - С. 150. Режим доступа: Сначев Н.П. Оптимизация запасов предприятия [Электронный ресурс] Режим доступа:
- Приказ Минфина России от 29.07.1998 № 34н «Об утверждении Положения по ведению бухгалтерского учета и бухгалтерской отчетности в Российской Федерации» (ред. от 29.03.2017). https://base.garant.ru/12112848/
- Приказ Минфина РФ от 06.07.1999 № 43н «Об утверждении Положения по бухгалтерскому учету «Бухгалтерская отчетность организации» (ред. от 08.11.2010). URL: http://base.garant.ru/5759066/
- Приказ Минфина России от 28.12.2001 N 119н (ред. от 24.10.2016) "Об утверждении Методических указаний по бухгалтерскому учету материально-производственных запасов" (Зарегистрировано в Минюсте России 13.02.2002 N 3245).URL: http://www.consultant.ru/document/cons_doc_LAW_35543/
- Баркалова М. Н. Учет материально-производственных запасов по российским и международным стандартам //том IV. – 2014. – С. 31. Режим доступа URL: https://cyberleninka.ru/article/v/razlichie-buhgalterskogo-uchetamaterialno-proizvodstvennyh-zapasov-po-rossiyskim-i-mezhdunarodnym-standartam
- Кругляк З. И., Калинская М. В. Экономическая сущность и классификация запасов, как объекта бухгалтерского учета //Политематический сетевой электронный научный журнал Кубанского государственного аграрного университета. – 2014. – №. 99. Режим доступа URL: https://cyberleninka.ru/article/n/ekonomicheskaya-suschnost-i-klassifikatsiyazapasov-kak-obekta-buhgalterskogo-ucheta
- Басалаева Е.В. Инновации в экономическом анализе, бухгалтерском и управленческом учете как формирование нового подхода к финансовому менеджменту // Международный бухгалтерский учет. 2015. № 24 (366). С. 34 - 45. Режим доступа URL: https://cyberleninka.ru/article/n/innovatsii-v-ekonomicheskom-analize-buhgalterskom-i-upravlencheskom-uchete-kak-formirovanie-novogo-podhoda-k-finansovomu-menedzhmentu/viewer
- Нидлз Б., Андерсон X, Колдуэлл Д. Принципы бухгалтерского учета: Пер. с англ. / Под ред. Я. В. Соколова. - Второй изд. - М .: Финансы и статистика 2014. Режим доступа URL: http://www.vkaznu.ru/index.php?showtopic=10648
- Юкаева, B.C. Управленческие решения: учебное пособие / В.С. Юкаева. – М.: Дашков и К, 2017. – 325 с. – материал взят с сайта Студворк https://studwork.org/shop/61016-upravlenie-zapasami-predpriyatiya-i-puti-ih-optimizacii