Реферат по теме выпускной работы
Содержание
- Введение
- 1. Литературный обзор
- 1.1 Актуальность темы, цели и задачи исследования
- 1.2 Анализ проблемы разделения системы N2 – CH4
- 1.3 Анализ технологий очистки природного газа от азота
- 1.4 Выбор технологии очистки для небольшого месторождения
- 2. Создание математической модели
- 3. Оптимизация параметров технологической схемы
- Выводы
- Список источников
Введение
Совершенствование технологий транспортировки, обнаруженные значительные запасы, снижение затрат на разработку и экологическая устойчивость — все это дает основание считать, что природный газ, в частности метан, останется одним из главных источников энергии в ближайшем будущем. Тем не менее, есть некоторые факторы, препятствующие его широкому применению. Повышенное содержание азота приводит к понижению качества газа, снижению его энергетической ценности, повышает затраты на перекачку газа. Поэтому, очистка природного газа от азота является неотъемлемым этапом его подготовки для использования.
1. Литературный обзор
1.1 Актуальность темы, цели и задачи исследования
Актуальность работы обусловлена тем, что в настоящее время нет относительно недорогих и эффективных методов очистки природного газа от азота, в особенности для небольших месторождений. Преимущественно исследованы методы очистки от примесей таких, как вода, диоксид углерода (углекислый газ
), сероводород (высокосернистый газ) и др. А очистка от азота представляется, как более трудный процесс в связи с малой химической активностью азота.
Объект исследования: система природный газ – азот.
Предмет исследования: очистка природного газа от азота на небольшом месторождении.
Цель исследования — изучение возможности удешевления и повышения эффективности процесса очистки природного газа от азота с использованием математического моделирования. Для достижения данной цели необходимо решить поставленные задачи.
Основные задачи исследования:
- Анализ существующих технологий очистки природного газа от азота.
- Выбор и проверка адекватности модели установки очистки для небольших месторождений.
- Подбор и оптимизация технологических параметров процесса на основе созданной модели.
Предложенные задачи будут корректироваться на основании полученных результатов.
1.2 Анализ проблемы разделения системы N2 – CH4
Азот является не токсичным и негорючим газом, не способствует коррозии. Наличие азота отрицательно влияет на теплоту сгорания смеси газов, выводит его из стандартного диапазона индекса Воббе и требований к газовому продукту. Кроме того, присутствие азота сказывается на стоимости перекачки газовой смеси и размерах оборудования, такого как компрессоры и трубопроводы. Согласно ГОСТам конечное значение концентрации азота после очистки должно быть меньше 1%.
И метан, и азот представляют собой устойчивые к химическим воздействиям газы, что является серьезной проблемой для разделения их в системе N2 и CH4. Также селективного отделения азота от метана добиться сложно из‐за почти одинакового критического диаметра молекул N2 и CH4 (3,64 Å и 3,80 Å соответственно) [1].
Сложность эффективного разделения N2 – CH4 связана со следующими факторами. Во‐первых, из‐за сходного критического диаметра между N2 и CH4 трудно разработать материалы с точным размером пор для эффективного молекулярного сита. Во‐вторых, обязательное наличие интенсивного броуновского движения делает практически невозможным контроль угла, под которым молекулы газа входят в поры материалов. Кроме того, различия в конденсируемости и поляризуемости не способствуют N2 – селективному разделению. Более высокая поляризуемость и критическая температура CH4 приводят к более сильному взаимодействию с большинством материалов, таким образом, препятствуя преимущественной адсорбции и проникновению N2 [2].
1.3 Анализ технологий очистки природного газа от азота
Разделение газов — процесс, который может осуществляться фракционной конденсацией (охлаждением, сопровождающимся образованием конденсированных систем), ректификацией, сорбцией селективными абсорбентами и адсорбентами, а также диффузией через пористые перегородки (мембранное газоразделение) и др. Наиболее широко в промышленности применяется конденсация в сочетании с сорбцией и ректификацией при низких температурах.
Основные доступные методы удаления азота: криогенная перегонка, абсорбция, адсорбция, мембраны и газоразделение на основе гидратов [3].
Криогенная перегонка остается ведущей технологией для крупных заводов по производству природного газа мощностью более 0,5 млн. стандартных кубометров в сутки (тыс. куб. м в сутки). Большие скорости потока газа позволяют покрыть высокие капитальные затраты на криогенную установку в течение нескольких лет. Метод основан на различии температур кипения различных компонентов для разделения. Для извлечения азота из природного газа используются четыре основных процесса криогенного фракционирования: одноколонный, двухколонный, трехколонный и многоколонный процессы. В одноколонном процессе используется одна криогенная дистилляционная колонна, которой помогает внешний холодильный цикл. Отсутствие внешнего холодильного цикла, который используется на заводах СПГ для исходного газа с низким содержанием азота, приводит к перерасходу товарного газа в произведенный азот. Три другие конфигурации, которые названы многоколонными процессами, работают на основе ребойлера и конденсатора, соединенных по теплу. В основе многоколонной структуры лежит идея двухколонного процесса, который изначально был изобретен и широко использовался для получения чистого кислорода [3].
При мембранном методе разделение компонентов газа достигается за счет различий размеров молекул и скорости их перемещения в мембранах, а также подвижности компонентов исходного природного газа [4]. Мембраны для разделения газов обычно делятся на три категории, определяемые материалами их изготовления: полимерные, неорганические мембраны и мембраны со смешанной матрицей. Транспорт молекул газа через мембрану по механизму растворения‐диффузии происходит сначала за счет абсорбции молекулы газа в мембрану, а затем за счет диффузии, или проникновения, молекулы через материал мембраны.
Для адсорбции при переменном давлении и технологий мембранного разделения, в соответствии с приоритетом газовых соединений, процессы разделения N2 и CH4 можно рассортировать на N2 – селективные процессы и CH4 – селективные процессы. В процессах, селективных по отношению к CH4, CH4 необходимо извлекать путем вакуумирования в цикле адсорбции или неизбежно концентрировать на стороне пермеата (потока вещества, проходящего через полупроницаемую мембрану в процессе мембранного разделения) при низком давлении, что требует дополнительной энергии и процессов повторного повышения давления CH4 до давления в трубопроводе для последующей обработки, что значительно увеличивает стоимость процесса. Таким образом, N2 – селективные процессы более выгодны для очистки природного газа, когда характеристики адсорбента и мембраны достигают стандарта, а их эксплуатационные расходы значительно ниже, чем CH4 – селективные процессы [5]. Для разделения N2 и CH4 применяются металлоорганические комплексы (МОК), цеолиты, твердый бор, модифицированные материалы и т.д. [4, 6].
Новейшими исследованиями является использование MoS2 в качестве адсорбента. Результат показывает, что взаимодействие между любым газом и исходным MoS2 очень слабое, но взаимодействие между N2 и MoS2 можно значительно улучшить легированием В или С [7].
Известные мембраны и адсорбенты, используемые при отделении азота, представлены в таблице 1.
Таблица 1 — Мембраны и адсорбенты, используемые при отделении азота
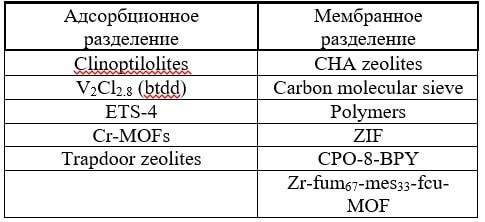
Некоторые МОК в смеси азота и природного газа в большей степени связывают азот. Металлоорганические каркасы представляют собой кристаллические материалы с большой площадью внутренней поверхности и большими объемами пор. Общая химическая схема обратимого связывания азота при адсорбции металлоорганическим комплексом представлена на рисунке 1.
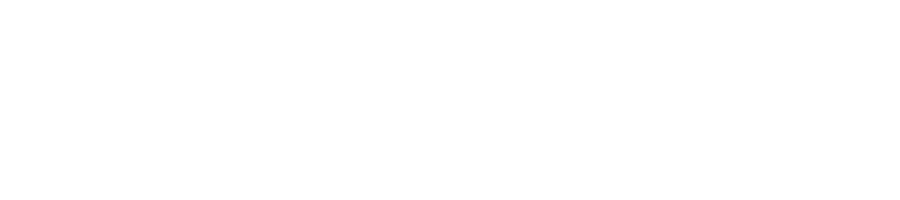
Анимация 1 — Общая химическая схема обратимого связывания азота при адсорбции металлоорганическим комплексом,
где R – общая органическая функциональность [5].
(количество кадров – 8, количество циклов – 5, объем – 95 Кб)
Склонность метана к гидратообразованию позволяет разделить компоненты смеси путем перевода метана в твердую фазу, при которых азот остается в газовой фазе. Клатратные гидраты представляют собой льдоподобные кристаллические соединения, которые состоят из клеток молекул воды, связанных водородными связями, которые захватывают небольшие молекулы природного газа внутри своих клеток. Гидраты природного газа в настоящее время являются важным фактором для большинства операций из‐за их склонности к агломерации и закупорке трубопровода или технологического оборудования. Для газовых смесей CO2 – N2 – СН4, CO2 является более стабильной молекулой в гидратной фазе, тогда как N2 является наименее стабильной. Это приводит к предпочтительному занятию CO2 над СН4 в гидратной клетке или, в отсутствие CO2, предпочтительному занятию СН4 над N. Большинство процессов разделения включают использование реактора с мешалкой и использование молекул-промоторов для снижения рабочего давления [1].
Также существует способ обеспечения комплексного извлечения ценных примесей из природного гелийсодержащего углеводородного газа с повышенным содержанием азота с его предварительной глубокой осушкой и очисткой, и дальнейшим выделением из него последовательно (по температурам кипения) пентан‐гексановой углеводородной фракции, бутановой фракции, пропановой фракции, этана, товарного топливного газа, жидкого азота и жидкого гелия высокой степени чистоты с применением эффективных технологий криогенного, ректификационного, абсорбционного, гравитационного и фильтрационного разделения и минимизации энергозатрат на реализацию процесса в целом за счет оптимального использования рекуперации тепла при теплообмене между горячими и холодными потоками и применения турбодетандеров, тепловых насосов. По второму варианту существует способ производства аммиака, который включает риформинг углеводорода с избытком воздуха для образования потока исходного синтез‐газа, удаление азота и инертных газов из потока исходного синтез‐газа дистилляцией, при этом обеспечивают охлаждение при помощи расширения жидкости посредством расширителя‐генератора, а верхний поток частично конденсируют сбросовым потоком, охлажденным посредством расширения жидких остатков из дистилляционной колонны, и подачу синтез‐газа со сниженным содержанием азота и инертных газов с дистилляции в контур синтеза аммиака, при котором жидкие остатки расширяют с помощью расширителя жидкости с извлечением работы [8].
Основные преимущества и недостатки рассмотренных методов перечислены в таблице 1.
Таблица 2 — Преимущества и недостатки основных методов отделения азота
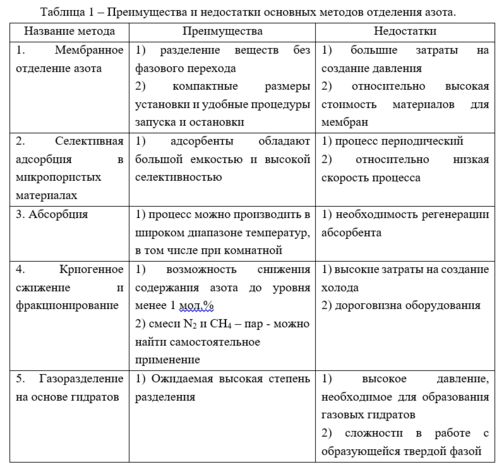
1.4 Выбор технологии очистки для небольшого месторождения
Основной заинтересовавший способ — нетривиальный метод поглощения абсорбцией метана из смеси газов с азотом, а не наоборот. Удаление азота с использованием абсорбционных технологий не является обычной
практикой в газовой промышленности. Существует несколько коммерческих процессов удаления N2, работающих за счет физической абсорбции СН4 в углеводородном масле, которые были созданы для переработки газа со скоростью подачи 2–30 млн куб. футов в сутки. Затраты на большое количество растворителя и повторное сжатие СН4 непомерно высоки для использования блока удаления азота с селективной абсорбцией СН4 на крупномасштабных заводах по производству СПГ; поэтому существует растущая потребность в разработке селективного абсорбента N2 [9].
Проводится процесс абсорбции минеральными маслами, например, прямогонной нафтой или парафиновым маслом, по существу состоящими из С5–С8, с последующим выпуском непоглощенного азота. При этом большую роль имеют молекулярные свойства N2 и СН4, включающие различия в кинетическом диаметре, поляризуемости, квадрупольном и дипольном моментах молекул. В [10] приведено описание процесса абсорбции метана прямогонной нафтой, включающего следующие стадии:
- Абсорбцию углеводородного компонента природного газа прямогонной нафтой, по существу состоящей из С5–С8 парафиновых углеводородов, в устройстве для осуществления абсорбции, и выпуск непоглощенного азота.
- Десорбцию углеводородного компонента из прямогонной нафты в отпарной колонне при температуре на ее дне в интервале от 150°C до 200°C.
- Рециркуляцию на стадию (а) прямогонной нафты, регенерированной при десорбции.
- Подачу десорбированного углеводородного компонента в распределительную сеть.
Его иллюстрационная схема представлена на рисунке 1.
![Рисунок 1 – Иллюстрационная схема абсорбции углеводородного компонента природного газа прямогонной нафтой [10]](images/pic_4.jpg)
Рисунок 1 — Иллюстрационная схема абсорбции углеводородного компонента природного газа прямогонной нафтой [10]
Основным преимуществом данного способа является доступность минеральных масел, используемых в качестве абсорбентов и возможность проводить процесс в широком диапазоне температур. Недостатком данного способа является многоступенчатое отделение метана от тяжелых углеводородов, т.к. алканы отлично растворяются друг в друге. Следующим этапом исследования мы намереваемся найти вещества и режимы, при которых метан будет достаточно хорошо поглощаться, несмотря на тяжелые углеводороды в системе, а также смоделировать абсорбционную установку для подбора наиболее подходящих условий и абсорбентов процесса.
2. Создание математической модели
Первый шаг — верный подбор исходных данных, что позволит нам определить оптимальные параметры процесса для достижения максимальной эффективности очистки газа и минимизации затрат.
Основным вариантом для очистки на небольших месторождениях является концентрация азота в исходном газе – от 5 до 15%, исходя из этого принимаем усредненную исходную концентрацию в 10%. Согласно ГОСТу конечное значение концентрации после очистки должно быть – до 1%.
Диапазон возможного изменения расхода, очищаемого газа составляет от 800 до 2400 н.м.куб./ч, в качестве отправной точки принимаем 800 н. м. куб./ч. Абсорбция происходит при комнатной температуре и давлении, равному давлению на входе природного газа. Отсюда температура на входе в абсорбер составляет 20°C, а давление возьмем из [10] – 6 МПа.
Процесс абсорбции состоит из двух основных этапов:
- Абсорбция: Природный газа поглощается абсорбентом (растворителем).
- Десорбция: Природный газа выделяется из абсорбента и направляется на подачу в распределительную сеть.
Подобную абсорбцию осуществляют либо в тарельчатых, либо в насадочных колоннах, подавая природный газ снизу, а абсорбент сверху, — для моделирования используем тарельчатую колонну. В данном случае в качестве основного компонента природного газа выступает метан, абсорбент необходим состава С5–С8 парафиновых углеводородов, поэтому в системе будем рассчитывать абсорбцию метана пентаном из системы метан – азот. Из верхней части колонны выпускают газ – азот преимущественно. Из нижней части колонны выпускают абсорбирующую жидкость, содержащую метан.
Математическая модель описывает динамику изменения концентраций в природном газе и абсорбенте на протяжении всего процесса абсорбции. Для создания математической модели необходимо составить уравнения материального баланса для каждой фазы процесса (газ и абсорбент–жидкость).
Следующим шагом является подбор программного обеспечения. В основу всех средств моделирования заложены общие принципы расчетов материально‐тепловых балансов химических производств. DWSIM — это инженерный симулятор, являющийся открытым аналогом таких продуктов, как HYSYS, UniSim и Symmetry. На основе DWSIM можно создавать цифровые двойники нефтегазовых производств, заниматься комплексной оптимизацией и существенно повышать эффективность работы оборудования без капитальных вложений в основные активы. Он тесно интегрирован с Microsoft Excel. Наряду с возможностями производить моделирование и оптимизацию сложных химико‐технологических систем эта программная оболочка позволяет производить проектный расчет параметров основного технологического оборудования. С помощью данной программы создается и расчитывается приблизительная схема вида — рисунок 2, подобная схеме рисунка 1 [10].
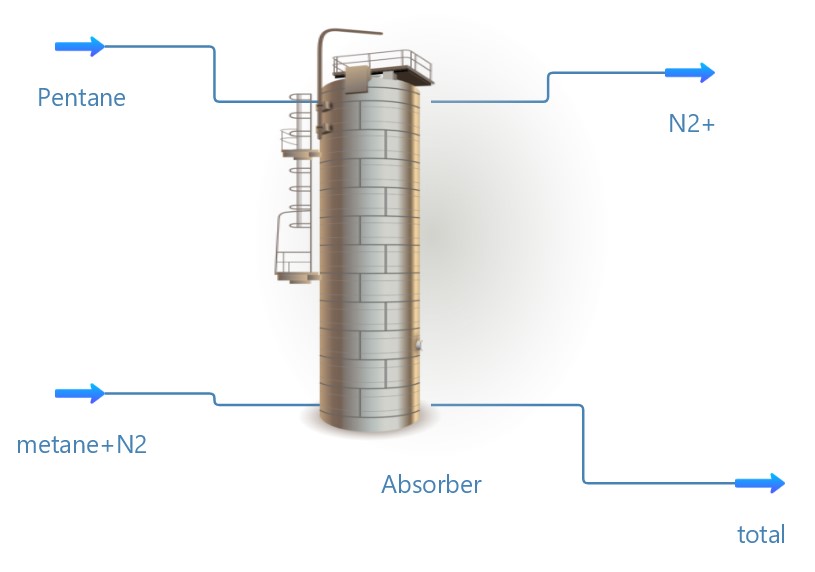
Рисунок 2 — Схема абсорбции углеводородного компонента природного газа прямогонной нафтой, созданная с помощью DWSIM
3. Оптимизация параметров технологической схемы
Для оптимизации параметров технологической схемы используются управляемые переменные — переменные, значения которых можно выбирать в технически допустимых пределах по своему усмотрению и тем самым влиять на ход технологического процесса. Примером управляемых переменных могут служить скорости потоков, температуры, давления в аппаратах, концентрации и т.д.
В данном случае условия протекания процесса представляются постоянными (температура, давление, концентрация), основная задача найти подходящий абсорбент для процесса, поэтому помимо пентана в качестве абсорбента, стоит смоделировать применение гексана и гептана, а далее сравнить конечные результаты.
Выводы
Отделение азота от метана является трудной задачей при использовании любой технологии, но без этого невозможно достичь необходимого качества продукта и увеличить эффективность работы оборудования. Необходимо искать новые методы и материалы для отделения азота от метана с высокой селективностью и эффективностью, а также совершенствовать существующие. Наиболее перспективным для относительно небольших месторождений на наш взгляд является абсорбция с подбором эффективного и не дорогостоящего абсорбента. Недостатки этого метода представляются устранимыми, если удастся найти подходящий абсорбент, который позволил бы повысить чистоту получаемого метана, а также простую и эффективную технологию регенерации абсорбента.
При написании данного реферата магистерская работа еще не завершена. Окончательное завершение: июнь 2024 года. Полный текст работы и материалы по теме могут быть получены у автора или его руководителя после указанной даты.
Список источников
- Ohs B., Lohaus J., Wessling M. Optimization of membrane based nitrogen removal from natural gas / Journal of Membrane Science, 498, 2016. – p. 291–301.
- Sun Q., Wang M., Li Z., Li P., Wang W., Tan X., Du A. Nitrogen removal from natural gas using solid boron: A first‐principles computational study. Fuel, 109, 2013. – p. 575–581, doi:10.1016/j.fuel.2013.03.032.
- Rufford T. E., Smart S., Watson G. C. Y., Graham B. F., Boxall J., Diniz da Costa J. C., May E. F. The removal of CO2 and N2 from natural gas: A review of conventional and emerging process technologies / Journal of Petroleum Science and Engineering, 94–95, 2012. – p. 123–154.
- Патент № 2559413 C2 Российская Федерация, МПК F25J 3/02. Удаление азота из природного газа / Х. Бауэр, М. Гвиннер, Д. Гарте; № 2011118883/06: заявл. 11.05.2011: опубл. 10.08.2015.
- Zhou Y., Yuan Y., Cong S., Liu X., Wang Z. N2 – selective adsorbents and membranes for natural gas purification / Separation and Purification Technology, 300, 2022.
- Патент на изобретение JPS6342717A Japan. Отделение азота / Okamoto H., 1986.
- Shuang W., Huijie L., Mengnan Q., Aijun D., Jianfen F., Qiao S. B/C–doped MoS2 as promising materials for nitrogen removal from natural gas: A first‐principles computational study / Computational Materials Science, 214, 2022.
- Патент на изобретение RU 2597081 C2. Способ комплексного извлечения ценных примесей из природного гелийсодержащего углеводородного газа с повышенным содержанием азота2014153653/05 / Мнушкин И. А., 2016.09.10. Заявка № 2014153653/05, 2014.12.29.
- Jusoh N., Lau K. K., Shariff A. M., Yeong Y. F. Capture of bulk CO2 from methane with the presence of heavy hydrocarbon using membrane process. International Journal of Greenhouse Gas Control, 2014, 22, 213–222.
- Патент № 2185226 C2 Российская Федерация, МПК B01D 53/14, C10L 3/10. Способ удаления азота из природного газа / Л. Чиккарелли. – № 2000103939/12 EDN MPXDXN; заявл. 18.02.2000: опубл. 20.07.2002.