Master of DonNTU Khomenko Vyacheslav
Elaboration of Typical Models of Electromechanical Systems for Possible Damages Analysis in the Production Facilities Parts
Abstract
Topicality
At present it is necessary to provide maintainability engineering of electromechanical equipment, control and determination of its state without disassembling, prediction of technical state and accident prevention.
Control without disassembling is executed using vibroacoustic diagnostic methods, thermal diagnostics, diagnostics by the electrical values of an electrical drive.
In that direction vibroacoustic diagnostic methods have reached the maximum evolution.
Our work is focused on the study of interference between electromechanical transducer and the driven load, and the search for the possibility to extract diagnostic symptoms from the electrical values of the mechanism (from electrical current, tension, power).
Domestic and foreign experience shows that the introduction of diagnostic facilities is economically feasible. It is well known, that the timely execution of repair works reduces the possibility of industrial injuries, the number of random equipment failures and correspondingly the time of downtime of production lines.
Objective
Elaboration of mathematical models that will perform to diagnose the emergency conditions in the production facilities parts.
Content of the work
The observable object can be in one of the following conditions:
- intact condition, i.e. the condition when the observable object meets all the requirements specified in the normative-technical documentation;
- capacity for work, i.e. the condition when the object is capable of executing the given functions within the limits specified in the normative-technical documentation (it means that some bugs can exist, but they do not impede the proper use of the object);
- adequacy of operation, i.e. the condition, when the object executes the predefined algorithms of operation at the given moment (it is known only that the object operates adequately in the given operating mode at the given moment);
- emergency situation of the object, when its further operation is impossible as its parameters exceed the acceptable limits.
There exist the following diagnosed damages:
- electromagnetic damages:
- packet of steel pressing loss;
- breakage of the wounding or short circuit in it;
- eccentricity, ellipsoidality of the interior stator bore relative to the stator rotational axis;
- incorrect reciprocal mounting of the rotor and stator packs;
- eccentricity of the exterior surface of rotor relative to its rotational axis;
- breakage or contact loss in the winding bars or in the cage rings of the squirrel-cage in the induction motor;
- pressing loss of whole packet of steel or only in the teeth region;
- imbalance of rotor masses;
- the shafts misalignment;
- mechanical impairment;
- catching of elements;
- problems with sliding bearings;
- problems with frictionless bearings;
- reducers and multiplicators damages;
- muffs damages.
During diagnostics of electrical drive condition all the necessary diagnostic symptoms are extracted from the observable signals. The following characteristics of the signals are used: spectrum, dynamical spectrum, cepstrum, correlation, autocorrelation, bispectrum, bicoherence, and wavelet decomposition. The methods of signal filtration, synchronous and synchronized detection, resonance amplification, and other methods of noise cancellation and extraction of valuable information are used. Application of Fourier theory and Fourier methods and wavelet transform in this case is perspective.
The next figure presents the cross-correlation function of two sinusoidal signals for different values of initial phases.
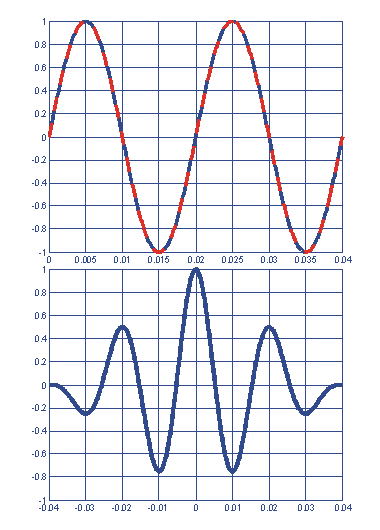
Figure 1 – Animated graph : cross-correlation function of two sinusoidal signals
Fourier transform, which transfers the signal notation from the time-based scale to the frequency-based scale, in fact breaks the signal into constituent sinusoids. That means that it loses the time information, and so is applicable only for stationary signals. Anyway, there are methods that provide some additional time information. Windowing, dividing the signal into parts and other methods are used. But such methods have some obvious limitations.
Forward Fourier transform:
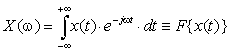
Inverse Fourier transform:

The wavelet transform in its turn is based on the wavelets - a certain form of the wave that has the limited duration and the average value of which makes zero. Thus, the wavelet transform is based on dividing the signal into the shifted and scaled versions of the original (mother) wavelet.

where:
- wavelet-coefficients which are functions of scale and position;
- wavelet scale;
- wavelet position;
- wavelet-function.
To establish the correspondence between the set of states W in the input of the electromechanical system and the set of diagnostics symptoms Z at the output, it is necessary to get a mathematical description of these relations using the models of electromechanical systems.
The set of states W can be divided into two subsets: W' and W''. The set W' includes operable states allowing the mechanism to execute the predefined functions. The reserve of the working capacity (the approach to the overload capacity) of each state in this subset is different. Transition from one state to another in the subset W' can be explained by malfunctions witch do not lead to the loss of working capacity (incipient damages). Subset W'' includes the states that indicate malfunctions in the mechanism that lead to the loss of working capacity.
In order to diagnose we have to divide all the possible conditions into a finite number m of classes Wi; i=1,2,...m. They are to be identified. The number of possible bugs determines the number of classes in the subset of states of nonoperability. Assuming such a classification of the object's states we can divide the process of diagnosis into several steps.
At the first step we determine which of the two subsets, W' or W'', the object belongs to.
Analysis of the object's states in the subset W' allows to determine the type of its working capacity changes and in some cases to predict the time of transition into the subset W''. At this step degradation processes take place in the parts of mechanisms as well as changes in the properties of vibroacoustic signals.
At the third step we determine which of the states in the subset W'' the object belongs to.
Conclusion
Application of typical models for electromechanical systems diagnostics will allow to automatize the diagnostic process, to increase the diagnostics accuracy. Determination of cross-correlation functions between electrical and mechanical parameters of the system will give a possibility to diagnose some damages with less effort.