Реферат по теме выпускной работы
При написании данного реферата магистерская работа еще не завершена. Окончательное завершение: январь 2014 года. Полный текст работы и материалы по теме могут быть получены у автора или его руководителя после указанной даты.
СОДЕРЖАНИЕ
- Введение
- 1. Актуальность работы
- 2. Цель и задачи исследования
- 3. Классификация тонкостенных изделий
- 4. Исследование особенностей применения ультразвука для механической обработки тонкостенных цилиндрических изделий
- 5. Конструкторская часть
- Предварительные выводы
- Список используемой литературы
ВВЕДЕНИЕ
В настоящее время все большее внимание уделяется развитию и совершенствованию обработки изделий со съемом относительно небольших слоев металла и создание на поверхности и в поверхностном слое необходимых физико-механических свойств и шероховатости.
Постоянное развитие техники на современном этапе требует использования деталей, которые имеют тонкие стенки (с целью экономии материала и облегчения конструкции в целом). Сейчас их количество значительно увеличивается в общей массе деталей, подвергающихся механической обработке. Тонкостенные трубы, как и оболочковые конструкции, обеспечивая высокую плотность компоновки, находят широкое применение в самых разных отраслях промышленности и, что особенно важно, в ответственных областях: нефтедобывающей, самолето- и ракетостроении, криогенной технике и холодильных установках, космических и военно – промышленных разработках.
Решение проблемы снижения металлоемкости изделий привело к появлению всевозрастающего числа входящих в эти изделия деталей, характеризующихся как нежесткие, одну из основных групп которых составляют тонкостенные цилиндрические детали.
В мировой практике металлообработки разработано большое количество методов обработки. По своей сущности они усложнились. Интенсивность протекания процессов разрушения, деформирования, преобразования материала деталей значительно возросла. В разработке и совершенствовании методов обработки имеет место тенденция одновременного воздействия на обрабатываемые заготовки и детали механических нагрузок и химических веществ, теплового или магнитного полей, электрической и лучевой энергии, энергии элементарных частиц и т.д. в различном их сочетании.
Накопленный опыт показывает, что не существует универсальных методов обработки деталей из различных конструкционных материалов, так как каждый имеет свою конкретную область рационального применения. Технолог и конструктор должны выбрать высокоэффективный метод обработки из большого числа возможных или создать на основе их совмещения комбинированный метод изготовления детали
В настоящее время во всех ведущих отраслях машиностроения все в больших масштабах применяют высокоэнергетические и комбинированные методы обработки материалов. Эти методы развиваются быстрыми темпами не только в силу своей относительной молодости, наличия задела еще не реализованных идей и возможностей, универсальности используемых энергоносителей, но и главным образом благодаря развитию современного машиностроения.
1. АКТУАЛЬНОСТЬ РАБОТЫ
В процессе резания обрабатываемая деталь и режущая кромка инструмента совершают упругие колебания. Поэтому для достижения особо высокой точности обработки необходимо не только проводить статический анализ взаимного расположения обрабатываемой детали и инструмента (что непосредственно влияет на точность обработки), но и в определенной степени анализировать колебательную систему станок-приспособление-инструмент-обрабатываемая деталь динамически, т. е. в ходе колебаний.
Если в дополнение к силе резания, изменяющейся с высокой частотой по синусоидальному закону, появляется еще одна составляющая, близкая по своей частоте к частоте собственных колебаний инструмента или обрабатываемой детали, то могут возникнуть биения, снижающие точность обработки. При этом может создаться такое положение, что обработка вообще окажется невозможной. При обычном резании принято считать, что практически все колебательные явления нежелательны. Во всех учебных пособиях указано, что необходимо использовать такие режимы резания, при которых не возникают колебания. При этом обращено внимание на то, что обработка детали не должна проводиться в низкочастотной области колебаний, где амплитуда довольно велика и может наблюдаться заметное дрожание обрабатываемой детали и инструмента. Однако уже давно давались рекомендации проводить обработку с наложением высокочастотных колебаний, в частности ультразвуковых.
В ходе изучения этого относительно нового метода обработки было установлено, что он является одним из перспективных методов обработки будущего, и это было связанно с его особенностями:
- cущественное снижение сил резания при обработке;
- устранение нароста;
- обеспечение доступа СОТС в зону резания;
- снижение высоты микронеровности обработанной поверхности в несколько раз по сравнению с обработкой, на одинаковых режимах, без ультразвуковых колебаний инструмента;
- снижение до минимума или отсутствие остаточных напряжений на обработанной поверхности после применения ультразвуковой технологии;
- снижение контактного трения.
Одновременно с увеличением количества тонкостенных труб повышаются и технические требования к точности размеров поверхностей, формы и их взаимного расположения. В прецизионном машиностроении допуски составляют порядка микрометров. Известны решения по получению труб методами пластического деформирования. Для получения цилиндрических изделий повышенной точности успешно применяется раскатывание. Но невозможность обработки отверстий сложной конфигурации, так же сложность конструкции, что влечет за собой усложненную технологию изготовления раскатки, ее повышенную себестоимость и пониженную надежность. Становиться вопрос о целесообразности применения раскатывания, и приходиться прибегать к резанию. Резание по своей сущности менее производительно, чем пластическое деформирование, так как формообразование происходит не в объёме заготовки, а по её поверхности. При обработке резанием геометрически возможная точность формообразования снижается вследствие проявления технологической наследственности и собственно погрешностей точения. Практика показывает, что при интенсификации режимов резания обычно ухудшается точность обработки, возникают интенсивные вибрации.
Поэтому разработка способов и средств, обеспечивающих заданную точность выходных параметров тонкостенных цилиндрических изделий и снижающих трудоемкость их изготовления, является актуальной научной задачей.
2. ЦЕЛЬ И ЗАДАЧИ ИССЛЕДОВАНИЯ
Целью данной работы является повышение качества изделий машиностроения на основе специальных композиционных технологий, путем разработки общего подхода их создания, базирующегося на композиции особенностей синтеза различных вариантов технологий, в которой количество направлений повышения качества изделий определяется числом вариантов технологий, входящих в состав композиционной технологии.
Для достижения указанной цели в магистерской работе были поставлены следующие задачи:
- Создание универсального лабораторного стенда для изучения механизмов ультразвукового воздействия с различных направлений на процесс резания. Определение положительных и отрицательных факторов применения ультразвукового точения. Определение факторов, способных позитивно воздействовать на процесс ультразвукового точения.
- Исследование влияния ультразвукового воздействия при точении на качество поверхности и поверхностного слоя, на формирование стружки.
- Исследование динамических характеристик упругой системы ультразвуковой установки.
- Исследование влияния ультразвукового воздействия на стойкость режущего инструмента, изучение природы этого влияния, определение путей повышения стойкости инструмента при УЗ воздействии на процесс резания.
- Выбор рациональных условий обработки с целью минимизации остаточных деформаций тонкостенных изделий.
- Определение деформирующей способности технологических остаточных напряжений при обработке точением тонкостенных цилиндрических изделий сложного поверхностного очертания с целью управления их остаточными деформациями.
3. КЛАССИФИКАЦИЯ ТОНКОСТЕННЫХ ИЗДЕЛИЙ
Для выполнения синтеза технологического процесса должна быть определенная база данных, из которой можно было бы производить выбор необходимых вариантов решений или относить получаемые решения к какому-либо классу объектов. При всем этом содержание базы данных должно быть подчинено определенным законам, а расположение технологических объектов должно выполняться по некоторым закономерностям. Эта проблема решается с помощью классификации тонкостенных изделий.
При проектировании технологических процессов определение общих свойств объектов помогает найти общие принципы, которые приводят к более простому проекту технологии изготовления тонкостенных изделий. На сегодняшний день пока не разработаны строгие методы классификации и нет общих правил, позволяющих выделять классы и объекты. Однако, классифицируя, мы объединяем в одну группу объекты, имеющие одинаковое строение и поведение. Разумная классификация, несомненно, часть любой точной науки [1,5].
Классификация тонкостенных изделий существенно облегчает понимание основной проблемы и дальнейшее развитие общего теоретического подхода синтеза технологического процесса комбинированной обработки тонкостенных изделий. Классификация помогает определить обобщенную, специализированную и собирательную иерархию объектов и классов. Целью классификации является нахождение общих свойств объектов и их поведения [1,6].
На рисунке 1 представлена классификация изделий с тонкостенными поверхностями. Классификация изделий осуществляется по следующим признакам:
- по виду изделия;
- по жесткости изделия;
- по назначению;
- по толщине стенок изделия;
- по типу внутренних полостей;
- по виду выполняемых эксплуатационных функций;
- по качеству поверхностного слоя;
- по методам обработки;
- по степени прецизионности.
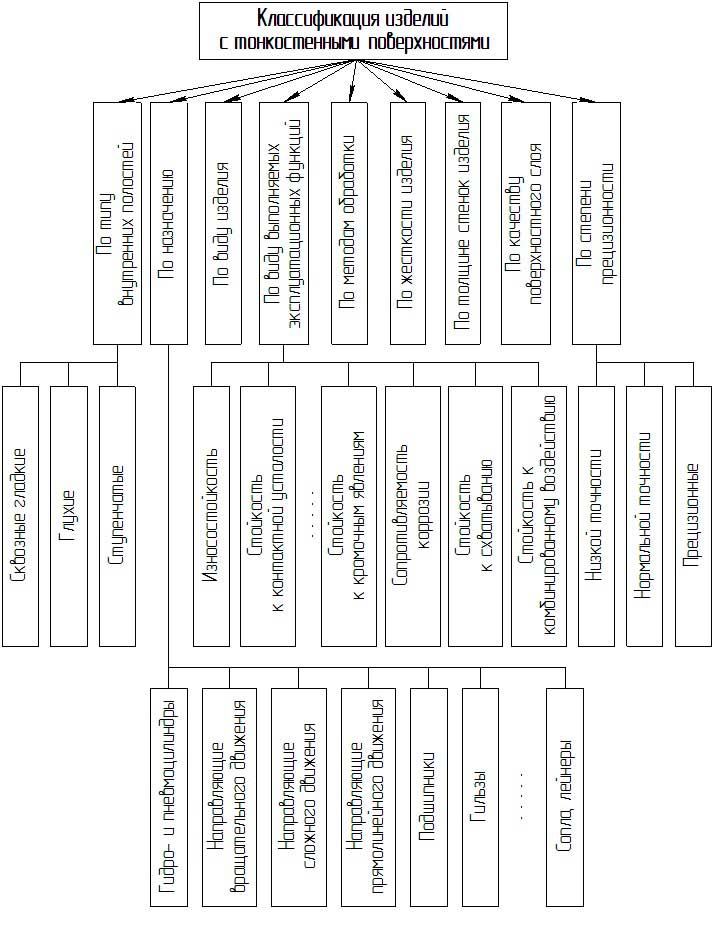
Рисунок 1 – Классификация тонкостенных цилиндрических изделий
По виду, изделия с тонкостенными цилиндрическими поверхностями подразделяются следующим образом: втулки и стаканы; диски и кольца; цилиндры и трубы [1,7].
К дискам и кольцам можно отнести такие изделия, в которых отношение высоты Н к диаметру D не превышает значения Н/D≤0,5. При этом для колец отношение наружного D к внутреннему d диаметру не должно превышать следующего значения D/d≤2,0. Для втулок и стаканов значение отношения высоты к диаметру находится в следующих пределах 0,5 < Н/D ≤ 2,0. Цилиндры и трубы имеют отношение высоты к диаметру, которое превышает значение Н/D > 2,0.
По жесткости, изделия с цилиндрическими поверхностями подразделяются на следующие: жесткие, нормальной жесткости и нежесткие.
К жестким можно отнести такие изделия, на деформацию которых не оказывают влияние силы закрепления в приспособлениях при обработке. К нормальной жесткости относятся изделия, деформация которых от закрепления в приспособлении при обработке находится в пределах допуска на обработку. Для нежестких изделий необходимы специальные приспособления для обеспечения заданной жесткости, так как без этих приспособлений возможна деформация изделия, превышающая допуск на обработку.
По толщине стенок, изделия с цилиндрическими поверхностями подразделяются на изделия с толщиной стенок: 0,3 … 1,0 мм; 1,0 … 3,0 мм; 3,0 … 10,0 мм.
По типу внутренних полостей, тонкостенные цилиндрические изделия подразделяются на следующие: сквозные гладкие, глухие и ступенчатые.
По степени прецизионности, тонкостенные цилиндрические поверхности могут быть следующие: низкой точности, нормальной точности, прецизионные.
По назначению, тонкостенные цилиндрические поверхности можно подразделять на: направляющие вращательного, сложного и прямолинейного движений, гидро- и пневмоцилиндры, подшипники, гильзы, сопла, лейнеры и др.
По виду выполняемых эксплуатационных функций, тонкостенные цилиндрические поверхности могут реализовывать следующие функции: стойкость к контактной усталости, износостойкость, стойкость к кромочным явлениям, сопротивляемость коррозии, стойкость к схватыванию, стойкость к комбинированному воздействию и др.
4. ИССЛЕДОВАНИЕ ОСОБЕННОСТЕЙ ПРИМЕНЕНИЯ УЛЬТРАЗВУКА ДЛЯ МЕХАНИЧЕСКОЙ ОБРАБОТКИ ТОНКОСТЕННЫХ ЦИЛИНДРИЧЕСКИХ ИЗДЕЛИЙ
Конструкции станков, предназначенные для механической обработки, не могут не допускать небольших колебаний обрабатываемой детали и инструмента, которые образуют своего рода колебательную систему. Общим случаем является резание с наложением вибраций, при котором силы резания действуют в виде импульсов, а выделение тепла незначительно. Обычное резание, которое сопровождается выделением тепла и обусловлено действием сил резания, состоящих из статической постоянной составляющей и наложенной на нее переменной составляющей (изменяющейся по синусоидальному закону), представляет собой лишь частный случай. Эти обстоятельства необходимо учитывать при рассмотрении принципов точной обработки.
Вибрационное резание связано с использованием специального оборудования, которое нуждается в умелом обращении, что создает определенные сложности. Однако после соответствующей настройки такого оборудования в дальнейшем уже не требуется особо высокой квалификации обслуживающего персонала. В таком случае даже при наличии лишь низкоквалифицированных рабочих можно наладить непрерывное производство деталей, обладающих малым разбросом размеров и практически постоянной точностью. Вибрационное резание позволяет осуществлять точную обработку, используя только точение. При этом можно точно обработать даже материалы, которые раньше для получения требуемой точности всегда подвергали шлифованию. Работы, которые прежде выполнялись, например, на дорогих шлифовальных станках (кругло- шлифовальных, плоскошлифовальных, внутришлифовальных и т. п.), при вибрационном резании оказываются ненужными. Таким образом, вибрационное резание обладает целым рядом достоинств, которые позволяют снизить трудоемкость работ и материальные затраты.
К особенностям применения ультразвука при механической обработке тонкостенных цилиндрических изделий можно отнести:
- уменьшение сопротивления резанию;
- повышение точности обработки;
- комнатная температура резания;
- исключение образования нароста;
- при такой обработке не образуются пластические деформации и не возникают заусенцы;
- шероховатость получаемой поверхности определяется только геометрическими факторами;
- стружка сходит плавно;
- улучшается смазывающее и охлаждающее действие СОТС;
- у получаемой поверхности расстояния между микронеровностями оказываются более удовлетворительными;
- поверхность может быть радужной;
- повышается износостойкость;
- возрастает коррозионная стойкость;
- повышается стойкость инструмента.
Все перечисленные преимущества в той или иной мере могут быть реализованы при вибрационном резании. Рассмотрим влияние каждой из них более подробно. Объектом рассмотрения является колебательная система, имеющая низкую частоту собственных колебаний, на которую действуют импульсные силы резания. Необходимо отметить, что период этих сил и продолжительность их действия очень малы. При проведении исследований измеряют импульсную силу резания, которая усредняется и дает среднюю силу резания. Для измерений используют экспериментальную установку, где силу резания определяют по деформации упругого элемента, на который наклеены тензометрические датчики. Можно считать, что при вибрационном резании абсолютное значение мгновенной силы резания или импульсной силы резания должно уменьшаться. При этом средняя сила резания будет в 3–10 раз меньше развиваемой при обычном резании.
При вибрационном резании, когда силы являются импульсными, в случае умелого использования переходной области динамических характеристик колебательной системы станка удается создать такие условия, при которых упругие колебания как бы приостанавливаются и перемещения становятся статическими, а средняя сила резания уменьшается.
Повышение точности обработки при вибрационном резании происходят за счет колебания режущей кромки резца. При этом в течение времени режущая кромка находится в контакте с обрабатываемой деталью и образуется стружка. Можно считать, что за это время положение режущей кромки (вершины резца) в процессе резания остается неизменным. Колебания обрабатываемой детали тоже как бы прекращаются. Это позволяет повысить точность обработки. Даже при использовании резания с вибрациями в серийном производстве разброс размеров получаемых деталей существенно снижается. Выборочный контроль показал, что даже при малых глубинах резания (несколько микрометров) точность обработки сохраняется на требуемом уровне продолжительное время.
При импульсном воздействии силы в импульсной форме выделяется и теплота в процессе резания. В этом отношении вибрационное резание существенно отличается от обычного. При вибрационном резании средняя сила резания резко уменьшается. В свою очередь, средняя температура резания тоже существенно снижается (примерно до уровня комнатной). При этом на стружке не появляются цвета побежалости, что наблюдается при обычном резании из-за окисления. Стружку, образовавшуюся после вибрационного резания, можно, не боясь обжечься, брать голыми руками, что при обычном резании в общем случае немыслимо.
Обычное резание можно сопоставить с пайкой, при которой нагретый паяльник крепко прижат к детали. Напротив, при вибрационном резании нагрев происходит только в результате постоянных быстрых перемещений паяльника вверх-вниз; при этом пайку никогда не удалось бы закончить. При обычном резании существенной проблемой становится развивающаяся температура. Под действием этой температуры могут происходить тепловые деформации обрабатываемой детали, что ухудшает точность обработки. Между тем в случае вибрационного резания устанавливающаяся температура в большинстве случаев не снижает точности.
Исключение образования нароста. При вибрационном резании не происходит повышения температуры; стружка образуется в области неустойчивости колебательной системы резец — обрабатываемая деталь во время переходного процесса. Поэтому даже если и предположить, что существуют некоторые факторы, стимулирующие возникновение нароста на режущей кромке резца, то ввиду кратковременности взаимодействия схватывания нароста с режущей кромкой не происходит.
Таким способом можно осуществлять прецизионное резание тонкостенных изделий, которые раньше обычно обрабатывали шлифованием; вибрирующим алмазным инструментом можно резать закаленные стали. Можно надеяться, что в перспективе вместо шлифовальных станков для обработки (заточки) инструмента будут использоваться станки с вибрирующим режущим инструментом. На основе вибрационного принципа резания можно будет создать весьма разнообразное новое станочное оборудование [3].
5. КОНСТРУКТОРСКАЯ ЧАСТЬ
В области ультразвуковых частот, создаваемых магнитострикционными вибраторами, осуществить вибрационную обработку без создания концентратора соответствующей конструкции и выбора подходящей геометрии инструмента практически не удается.
Для колебательных систем режущего инструмента с магнито- стрикционными вибраторами необходимо выполнение следующих условий:
- когда инструмент закреплен на концентраторе, используемом для увеличения амплитуды колебаний, необходимо, чтобы достигался резонанс частот вибратора и инструмента;
- режущий инструмент должен легко крепиться к вибратору или концентратору и легко сниматься с них;
- для колебательной системы инструмента следует определить координаты узлов колебаний и крепить инструмент к суппорту именно в этих местах;
- если колебательная система инструмента соединяется с суппортом в узлах колебаний на болтах, то необходимо подобрать такие конструкции, при которых частота собственных колебаний системы не изменялась бы [3].
Простые геометрические соображения показывают, что при колебаниях вершины резца под углом к направлению его движения будет ухудшаться точность обработки, т.е. колебания окажутся вредными. Поэтому существует три метода наложения колебаний на инструмент:
- в направлении осевой составляющей силы резания;
- в радиальном направлении;
- в направлении главной составляющей силы резания.
С учетом наложения колебаний различного направления была спроектирована установка, для наложения высокочастотных колебаний на инструмент в радиальном и тангенциальном направлениях, что показывает ее универсальность. Установка, которая изображена на рисунке 5.1, предварительно была спроектирована в системе автоматизированного проектирования SolidWorks и совершала только колебания в радиальном направлении.
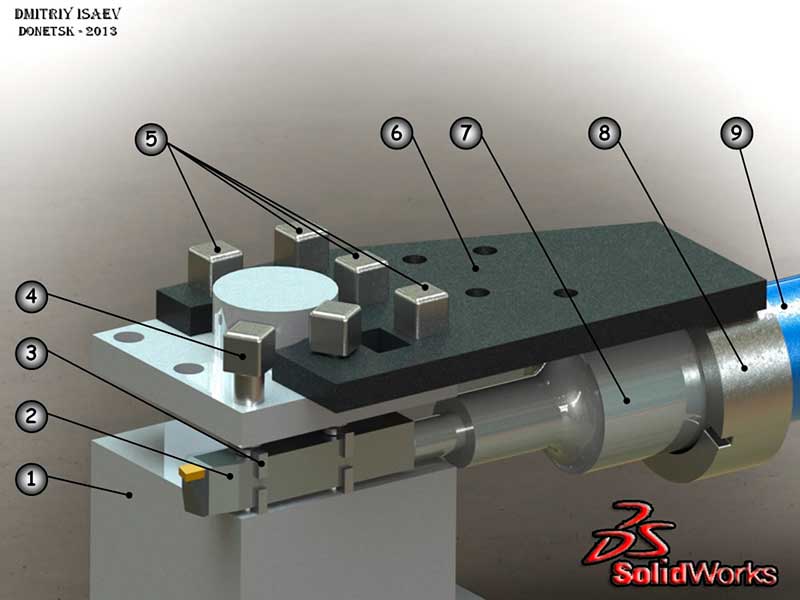
Рисунок 5.1 – Установка для радиального направления колебаний
(1- резцедержатель; 2 – резец; 3 – направляющие опоры; 4 – винты М14; 5 – винты М14(укороченные); 6 – стальной лист; 7 – концентратор ступенчатый; 8 – кольцо; 9 – магнитострикционный преобразователь)
Установка состоит из ступенчатого концентратора 7, к которому через шпильку прикрепляется резец 2. В кольцо 8, приваренное к листу 6, крепится по внешней резьбе магнитострикционный преобразователь 9. Концентратор с резцом крепятся по внутренней резьбе к преобразователю. Собранный узел устанавливают на резцедержатель 1 станка и закрепляют винтами 5. Согласно ранее проведенным расчетам, резец устанавливается в рабочее положение между направляющими опорами 3 и поджимается винтами 4.
Опыты планируется проводить на базе токарно-винторезного станка модели 1М61 [8]. Для данного типоразмера станков предназначена спроектированная установка, пример работы которой изображен на рисунке 5.2.
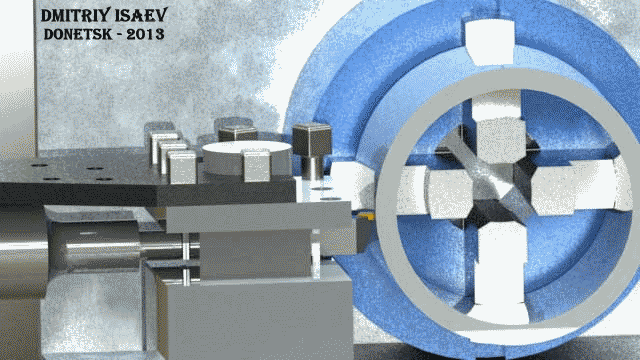
Рисунок 5.2 – Анимационный пример работы установки для радиального наложения колебаний, разработанный в SolidWorks(8 картинок, 22 кадра/с, объем - 507кб)
Известно, что наложение тангенциальных высокочастотных колебаний на инструмент – более перспективное направление исследований, поэтому предусматриваем перенастройку установки, как изображено на рисунке 5.3, для обеспечения тангенциальных колебаний.
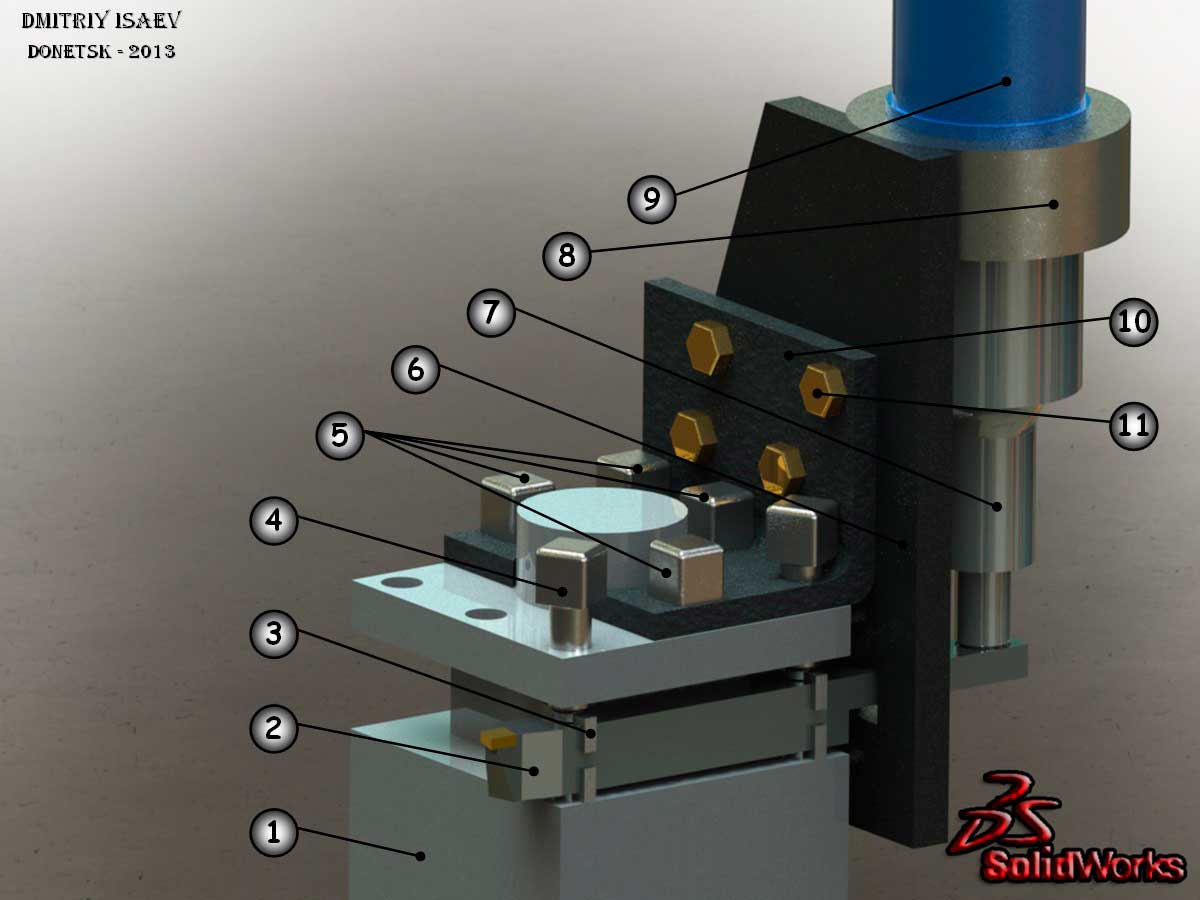
Рисунок 5.3 – Установка для тангенциального направления колебаний
(1- резцедержатель; 2 – резец; 3 – направляющие опоры; 4 – винты М14; 5 – винты М14(укороченные); 6 – стальной лист; 7 – концентратор ступенчатый; 8 – кольцо; 9 – магнитострикционный преобразователь; 10 – стальной уголок; 11 – винты М12)
Узел состоящий из магнитострикционного преобразователя 9, кольца 8, ступенчатого концентратора 7 и стального листа 6 устанавливаем вертикально и закрепляем винтами 11 к стальному уголку 10, который крепится к резцедержателю 1 с помощью винтов 5. Резец 2, имеющий удлиненную хвостовую часть, устанавливается в рабочее положение и закрепляется винтами 4. Резец к концентратору крепиться с помощью шпильки.
Далее преобразователь подключается к ультразвуковому генератору (в данном случае - модели УЗГ1-1), который будет преобразовывать электрическую энергию промышленной частоты в электрическую энергию ультразвуковой частоты [9]. Так как преобразователь в ходе работы нагревается – предусмотрен подвод охлаждающей жидкости электронасосом станка к соплам преобразователя, расположенных на задней части корпуса.
ПРЕДВАРИТЕЛЬНЫЕ ВЫВОДЫ
В данной работе проведен анализ современного состояния вопроса вибрационного резания тонкостенных изделий. Таким образом можно осуществлять прецизионное резание тонкостенных изделий, которые раньше обычно обрабатывали шлифованием; вибрирующим алмазным инструментом можно резать закаленные стали. Можно надеяться, что в перспективе вместо шлифовальных станков для обработки (заточки) инструмента будут использоваться станки с вибрирующим режущим инструментом. На основе вибрационного принципа резания можно будет создать весьма разнообразное новое станочное оборудование.
Комбинированный метод обработки, а именно применение ультразвуковых колебаний в процессе токарной обработки тонкостенных изделий нуждаются в дальнейшем исследовании, так как применение ультразвука приводит к заметному снижению силы резания, что в свою очередь значительно снижает упругие отжатия в системе СПИД , снижению шероховатости, повышение коррозионно- и износо-стойкости, повышение точности и значительное снижение износа оборудования.
При написании данного реферата магистерская работа еще не завершена. Окончательное завершение: январь 2014 года. Полный текст работы и материалы по теме могут быть получены у автора или его руководителя после указанной даты.
СПИСОК ИСПОЛЬЗУЕМОЙ ЛИТЕРАТУРЫ
- Таровик А.Б., Михайлов А.Н. Классификация и особенности эксплуатации изделий с тонкостенными цилиндрическими поверхностями // Cб. трудов межд. науч.-тех. конф. в г. Севастополе 17 – 22 сентября 2012 г. – Донецк: ДонНТУ, 2012.
- Таровик А.Б., Михайлов А.Н. Классификация комбинированных методов обработки тонкостенных цилиндрических изделий // Прогресивні технології і системи машинобудування: Міжнародний зб. наукових праць. - Донецьк: ДонНТУ, 2012.
- Кумабэ Д. Вибрационное резание: Пер. с яп. С.Л. Масленникова/ Под ред. И.И. Портнова, В.В. Белова. – М.: Машиностроение, 1985. – 424 с.
- Астахов С.А. Высокопроизводительное точение тонкостенных закалённых цилиндрических заготовок // Автореферат диссертации по машиностроению и машиноведению. - Тула:ТулГУ, 2012.
- Хубка В. Теория технических систем: Пер. с нем. – М.: Мир, 1987. – 208 с.
- Михайлов А.Н. Основы синтеза функционально-ориентированных технологий машиностроения. – Донецк: ДонНТУ, 2008. – 346 с.
- Кривошапко С.Н. Аналитические поверхности в архитектуре зданий, конструкций и изделий. – М.: Либроком, 2012. – 328 с.
- Станок токарно-винторезный модели 1М61. Руководство по эксплуатации. - М:Машиностроение, 1981.
- Генератор ультразвуковой модели УЗГ1-1. Руководство по эксплуатации. - М:МашГиз, 1985.