Реферат по теме выпускной работы
Содержание
- Вступление
- 1. Анализ теоретических основ выпаривания
- 2. Анализ технологического процесса как объекта управления с точки зрения его материальных потоков и их информационных переменных
- 3. Особенности процесса выпаривания в схеме многоконтурного регулирования
- 4. Математическая модель процесса выпаривания гидроксида калия
- 4.1. Структурная схема САР соотношения потоков исходного раствора и греющего пара
- 4.2. Структурная схема САР концентрации раствора гидроксида калия
- Выводы
- Список источников
Вступление
Химическая промышленность позволяет синтезировать материалы, которых нет в природе, использовать их для создания всевозможных машин и приборов, для строительства жилищ и производства товаров потребления. Поэтому химическая промышленность в мире развивается быстрыми темпами.
Химическая промышленность выпускает синтетический каучук, пластические массы, искусственное волокно, искусственное топливо, красители, лекарственные вещества и многое другое.
Выпаривание – процесс концентрирования растворов нелетучих веществ путем удаления жидкого летучего растворителя в виде пара.
Этот процесс широко распространен (в химической, пищевой, металлургической и других отраслях) по причине того, что многие вещества получают в виде разбавленных водных растворов, а для дальнейших производственных этапов они нужны в концентрированном виде. Также за счет концентрирования растворов уменьшается их объем и снижаются затраты на их транспортировку.
В процессе выпаривания происходит частичное удаление растворителя из всего объема раствора при его температуре кипения. Это является принципиальным отличием выпаривания от испарения, которое происходит на поверхности раствора при любых температурах ниже температуры кипения. В некоторых случаях выпаренный раствор подвергают последующей кристаллизации в выпарных аппаратах, специально сконструированных для этих целей.
На практике часто в качестве греющего агента при выпаривании используют водяной пар, который называют греющим или первичным. Первичным служит пар, получаемый из парогенератора, или отработанный пар. Пар, который образуется при выпаривании кипящего раствора, называется вторичным. Тепло необходимо для поддержания процесса обычно подводят через стенку. Процесс проводят под вакуумом, при повышенном и атмосферном давлении. Выбор давления в значительной степени зависит от свойств выпаривания и возможности использования тепла вторичного пара.
1. Анализ теоретических основ выпаривания
Выпариванием называют процесс концентрирования растворов, который заключается в частичном удалении растворителя путем его удаления при кипении. Сущность выпаривания заключается в переводе растворителя в парообразное состояние и отвод полученного пара от сконцентрированного раствора, который остался [1].
Процесс выпаривания проводят таким образом, чтобы при заданной производительности получить раствор необходимой концентрации, надлежащего качества, без потерь сухого вещества и при возможно меньшем расходе топлива. Особенностью процесса выпаривания является то, что в парах кипящих растворов нормально содержатся только пары чистого растворителя, а растворенное вещество является нелетучим. Это положение, лежащее в основе теории и методов расчета выпарных аппаратов, для большинства растворов твердых веществ вполне оправдывается. Растворитель удаляется в парообразном состоянии, чаще всего представляет собой водяной пар, который носит название вторичного пара.
В качестве теплоносителя при выпаривании используют насыщенный или слегка перегретый водяной пар, который называется греющим или первичным. Первичным служит либо пар, получаемый из парогенератора, или отработанный пар, либо пар промежуточного отбора паровых турбин. Тепло, необходимое для выпаривания раствора, обычно подводится через стенку, отделяющую теплоноситель от раствора. В некоторых производствах концентрирование растворов осуществляют при непосредственном прикосновении выпариваемого раствора с топочными газами или другими газообразными теплоносителями. Также может применяться электрический обогрев.
Протекание теплоносителей в греющей камере происходит под действием напора, создаваемого извне. Скорость течения теплоносителей по трубкам в большинстве случаев определяется естественной циркуляцией и зависит от разницы удельных весов закипающего в греющей камере раствора, пронизанного пузырьками пара и раствора, который опускается по циркуляционной трубе.
2. Анализ технологического процесса как объекта управления с точки зрения его материальных потоков и их информационных переменных
Исследуем ТП на наличие материальных потоков. Цель управления выпарной установкой заключается в получении раствора заданной концентрации.
Основной регулируемой технической величиной является концентрация выпариваемого раствора на выходе из второго выпарного аппарата. Концентрация выпариваемого раствора зависит от расхода и концентрации исходного раствора, расхода греющего пара, уровня раствора в выпарных аппаратах [2–4]. Таким образом, схема материальных потоков и их информационных переменных будет выглядеть следующим образом:
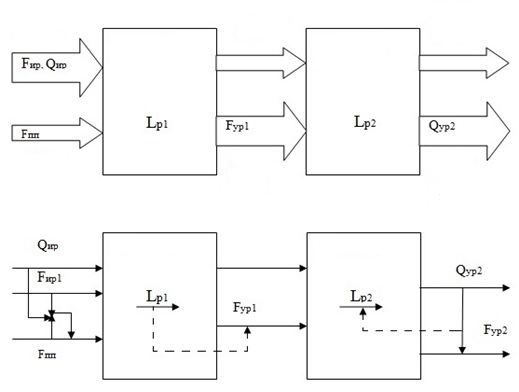
Рисунок 1 – Схема материальных потоков и информационных переменных процесса выпаривания
На рис. 1 находятся следующие обозначения:
- расход исходного раствора – Fир;
- концентрация исходного раствора – Qир;
- уровень в выпарном аппарате – Lp;
- концентрация упаренного раствора – Qyр2;
- расход первичного пара – Fпп;
- расход упаренного раствора – Fур2.
В выпарной аппарат-1 подаются исходный раствор с определенной концентрацией и греющий пар. Греющий пар подают в установку в определенном соотношении с расходом исходного раствора и его концентрацией. Далее происходит частичное упаривание исходного раствора. Частично упаренный раствор отводят с установки по уровню в первом аппарате. Затем полученный раствор и вторичный пар поступают во второй выпарной аппарат. Выпаренный раствор отводят с установки по уровню в последнем аппарате, регулятором, задание которому изменяет регулятор концентрации растворенного вещества в выпаренном растворе.
3. Особенности процесса выпаривания в схеме многоконтурного регулирования
Цель управления выпарной установкой заключается в получении раствора заданной концентрации, а также в поддержании материального и теплового балансов.
При больших колебаниях расхода исходного раствора, а также при изменении в нем концентрации растворенного вещества, качественное регулирование процесса обеспечивается применением сложных схем, например, схемы многоконтурного регулирования, которая представлена на рис. 2 [5–7].
Греющий пар подают в установку в определенном соотношении с расходом исходного продукта. Это соотношение корректируют регулятором концентрации растворенного вещества в исходном растворе. Для стабилизации работы второго выпарного аппарата частично упаренный раствор, направляемый к нему, регулируется по каскадной схеме регулирования расхода с коррекцией по уровню раствора в первом выпарном аппарате. Давление в системе поддерживается на заданном значении путем регулирования расхода пара растворителя с коррекцией по давлению в последнем выпарном аппарате.
Тепловой баланс процесса выпаривания при больших колебаниях расхода исходного раствора, а также при изменении в нем концентрации растворенного вещества, обеспечивают регулятором расхода на трубопроводе подачи греющего пара в кипятильник 2 первого корпуса установки.
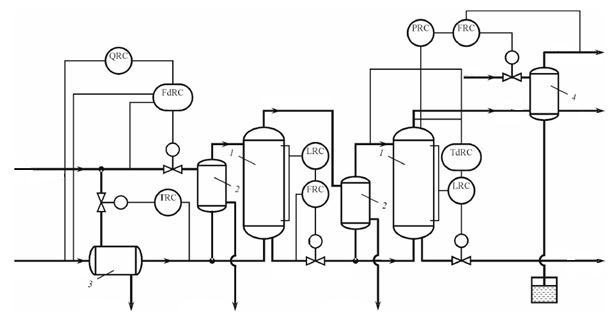
Рисунок 2 – Схема многоконтурного регулирования двухкорпусной выпарной установкой
Нормальный тепловой режим работы выпарной установки возможен только при подаче исходного раствора с постоянной температурой Тк, близкой к температуре кипения раствора. Для достижения этого устанавливают регулятор температуры исходного раствора, выходной сигнал которого влияет на клапан, который меняет подачу греющего пара в теплообменник-подогреватель исходного раствора 3.
Если весь вторичный пар из предыдущего корпуса направляется в кипятильник 2 последующего, то давление (разрежение) стабилизируют только в последнем корпусе, изменяя с помощью регулятора количество паров растворителя, отводимых из него. Последнее обычно достигается путем изменения подачи охлаждающей воды в барометрический конденсатор 4.
Выпаренный раствор отводят с установки по уровню в последнем аппарате, регулятором, задание которому изменяет регулятор концентрации растворенного вещества в упаренном растворе.
Если расход исходного раствора зависит от работы предыдущих технологических установок, но колебания его незначительны, то концентрацию упаренного раствора можно регулировать изменением подачи греющего пара на установку. При этом с помощью регуляторов уровня в выпарных аппаратах изменяют количество отведенного из них раствора.
4. Математическая модель процесса выпаривания гидроксида калия
Выпарной аппарат, будучи крупногабаритным аппаратом, как объект регулирования, по каналу расход греющего пара – концентрация полученного раствора
обладает значительной инерционностью. Динамику выпарного аппарата по основному управляющему каналу концентрация полученного раствора – расход греющего пара
можно описать линеаризованным дифференциальным уравнением идеального перемешивания при условии, что уровень жидкости в аппарате постоянный, то есть выполняется условие стабилизации материального баланса. Изменение концентрации гидроксида калия на выходе ΔQ из аппарата объемом V при изменении концентрации ΔQ0 в исходном растворе должно устраняться изменением расхода пара ΔF2 [8–10].
Регулирование концентрации раствора гидроксида калия осуществляется путем изменения расхода греющего пара F2 через регулирующий клапан, который осуществляет регулирование в пределах 0...100%. На электропривод (исполнительный механизм) регулирующего клапана поступает сигнал задания открытия клапана в виде нормированного токового сигнала 4...20 мА. Максимальная скорость перемещения штока составляет 25 %/с.
По своим динамическим свойствам исполнительный механизм представляет собой апериодическое звено первого порядка с постоянной времени 1 с. Трубопровод от клапана до входа в выпарной аппарат моделируется инерционным звеном первого порядка с коэффициентом передачи K = 3/100 и постоянной времени T = 2 с. [11]. На вход звена должен подаваться сигнал положения штока в процентах хода регулирующего органа (РО) (0...100% хода РО).
Схема моделирования исполнительного механизма (ИМ) с регулирующим органом (РО) и трубопроводом к выпарному аппарату изображена на рис. 3.

Рисунок 3 – Схема моделирования ИМ с РО, трубопроводом к випарному аппарату
4.1. Схема моделирования САР соотношения потоков исходного раствора и греющего пара
В соответствии с выбранной идеологией управления комбинированная САУ стабилизации концентрации раствора гидроксида калия состоит из двух контуров [12–15]. Внутренний контур – это контур стабилизации соотношения расходов исходный раствор – греющий пар
. Он регулирует расход греющего пара F2 в определенном соотношении с расходом исходного раствора F1 (так называемый регулятор соотношения потоков). Внешний контур стабилизирует концентрацию полученного раствора KOH путем изменения расхода пара F2 и меняет задачи регулятору соотношения в зависимости от концентрации КОН на выходе испарительного аппарата.
Построим и проанализируем динамику регулятора соотношения потоков исходного раствора и греющего пара. Схема моделирования САР соотношение потоков будет построена в соответствии с принципом по отклонению.
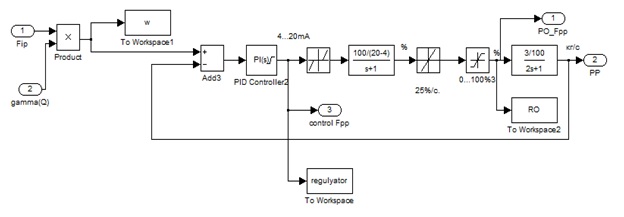
Рисунок 4 – Схема моделирования САР соотношения потоков исходного раствора и греющего пара
Из структуры САР видно, что выход регулятора соотношения ограничен возможным диапазоном его выходного сигнала 4...20 мА, а также блок зоны нечувствительности в интервале -4...4 мА, что следует из нижнего порогового значения диапазона выходного сигнала контроллера. Далее идет модель ИМ, РО и трубопровода, рассмотренная выше.
Основная задача синтеза САР заключается в выборе закона регулирования и определении настроечных параметров регулятора. Из практики применения регуляторов соотношения потоков принимаем ПИ-закон управления.
Значения параметров настройки, достаточно близкие к оптимальным, могут быть получены в результате исследования динамики замкнутой системы. В качестве метода нахождения настроечных параметров регулятора выберем метод автоматической настройки блока PID-control пакета моделирования Matlab, поскольку методы автоматической оптимизации является мощным средством современных промышленных контроллеров. Метод автоматической настройки основывается на трех этапах: идентификации модели объекта, определении параметров регулятора и настройке параметров.
Выбор вышеупомянутого метода обусловлен тем, что параметры регулятора определяются по существующим и широко распространенным методикам Зиглер и Никольса, а также CHR (Chien, Hrones и Reswick) затем настраиваются вручную или автоматически в процессе анализа динамики САР.
При настройке регулятора основное внимание уделяется отработке изменения сигнала уставки, поскольку контур регулирования расхода греющего пара в соотношении с расходом исходного раствора является внутренним контуром САР концентрации гидроксида калия. Таким образом, с учетом ограничений на выходной сигнал регулятора 4...20 мA и скорость РО 25 %/c, параметры настройки ПИ-регулятора имеют следующие значения: Kp = 0, Ku = 0.67 обеспечивающие быстродействие, равное 16,6 с. На анимации под цифрой 1 приведен график переходной характеристики настройки регулятора соотношения, а под цифрой 2 график расхода греющего пара при изменении расхода исходного раствора с 0,6 кг/с до 0,5 кг/с.
Переходная характеристика расхода греющего пара носит апериодический характер с перерегулированием 8% и время регулирования 473 с. Данные показатели являются удовлетворительными для внутреннего контура.
На анимации под цифрой 3 и под цифрой 4 приведены графики переходных характеристик управляющего сигнала на выходе ПИ-регулятора, а также хода регулирующего органа.
Из этих графиков следует, что регулятор не выходит за пределы зоны ограничения 4...20 мА, необходимый расход греющего пара 2,4 кг/с обеспечивается открытием клапана на 80%.
4.2. Схема моделирования САР концентрации раствора гидроксида калия
Внешний контур стабилизирует концентрацию полученного раствора KOH путем изменения расхода пара F2 и корректирует задание регулятору соотношения в зависимости от концентрации КОН на выходе выпарного аппарата [16–18].
По технологии, требования к показателям САР концентрации следующие:
- апериодический характер переходного процесса с допустимым перерегулированием 5...10%;
- время установления (регулирования) 20 мин;
- время отработки внешнего возмущения 8-10 мин.
Выход концентрации раствора гидроксида калия на уставку 40% требует настройки внешнего регулятора по концентрации. Поскольку канал по управлению концентрация – расход греющего пара
обладает большой инерционностью [19, 20], а также исходя из практики, необходимо выбрать ПИД-закон управления.
Для расчета начальных значений параметров регулятора концентрации был применен метод CHR по отзыву на внешние возмущения. Начальные расчетные данные следующие: Kp = -0.026, Ku = -6e-4, Kd = -2.1. Однако при таком значении дифференциальной составляющей выход регулятора выходит за пределы ограничений его выходного сигнала и поэтому данные начальные значения были оптимизированы с помощью автоматического метода подстройки.
Результаты моделирования были получены по схеме моделирования САР. Подсистема САР соотношение потоков реализована на рис. 5.
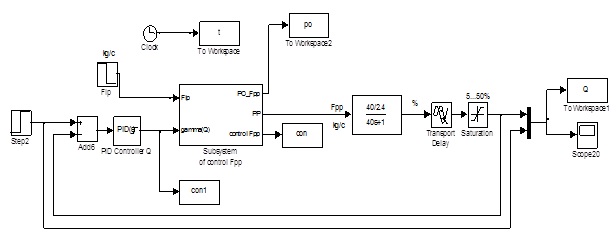
Рисунок 5 – Схема моделирования двухконтурной САР концентрации раствора гидроксида калия
Результаты автоматической настройки обеспечили заданные требования по качеству переходного процесса. График переходной характеристики регулятора, график переходной характеристики концентрации КОН и график переходного процесса регулятора соотношения при отработке уставки концентрации на 40% приведены в анимации под цифрами 5, 6 и 7 соответственно.
Анализ переходной характеристики по концентрации раствора гидроксида калия на выходе показывает, что регулятор отрабатывает внешнее возмущение на систему за 9 мин, не выходя за допустимый диапазон изменения по концентрации, соответствующей требованиям.
Переходная характеристика по концентрации раствора носит апериодический характер с перерегулированием 6% и временем регулирования 527 с.
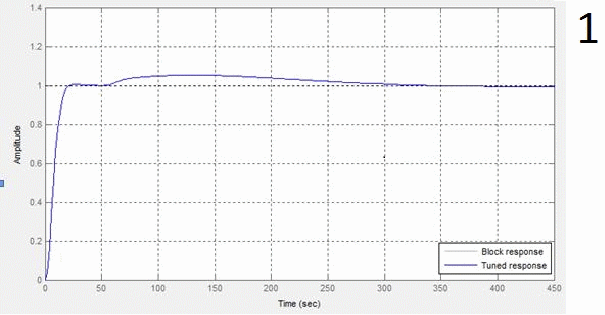
1 – окно настройки параметров блока PID-control,
2 – график переходного процесса расхода пара при изменении расхода исходного раствора с 0,6 кг/с до 0,5 кг/с,
3 – график переходного процесса выхода регулятора при изменении расхода исходного раствора с 0,6 кг/с до 0,5 кг/с,
4 – график переходного процесса хода регулирующего органа при изменении расхода исходного раствора с 0,6 кг/с до 0,5 кг/с,
5 – окно настройки параметров блока PID-control регулятора концентрации,
6 – график переходной характеристики концентрации КОН,
7 – график переходного процесса регулятора соотношения при отработке уставки концентрации на 40%
Рисунок 6 – Полученные графики переходных процесов в результате моделирования
(анимация: 7 кадров, 5 циклов повторения, 106 килобайт)
Выводы
- Разработана математическая модель процесса выпаривания гидроксида калия на основании линеаризованного дифференциального уравнения.
- Составлена комплексная модель САР. Проведен синтез систем автоматического регулирования процессов выпаривания раствора гидроксида калия. В качестве законов регулирования по каналу управления
концентрация – расход греющего пара
выбран ПИД-закон, а по каналурасход исходного раствора – расход греющего пара
ПИ-закон. Параметры регуляторов были определены методом Chien, Hrones и Reswick и автоматически оптимизированы средствами блока PID-control. Результаты моделирования показывают работоспособность САР и возможность применения разработанных систем, основными показателями качества которых выступают:
- отсутствие статической ошибки;
- время регулирования – около 20 мин;
- апериодический характер переходных процессов с допустимым перерегулированием;
- удовлетворительное время отработки возмущений;
- компенсация возмущений за счет выбранного принципа управления по отклонению.
При написании данного реферата магистерская работа еще не завершена. Окончательное завершение: декабрь 2015 года. Полный текст работы и материалы по теме могут быть получены у автора или его руководителя после указанной даты.
Список источников
- Таубман Е. И. Расчёт и моделирование выпарных установок. – М.: Химия, 1970. – 215 с.
- Попов Н. П. Выпарные аппараты в производстве минеральных удобрений. – Калининград: КГТУ, 1974. – 538 с.
- Кафаров В. В., Макаров В. В. Гибкие автоматизированные системы в химической промышленности: Учебник для вузов. – М.: Химия, 1990. – 320 с.
- Дудников Е. Г. Автоматическое управление в химической промышленности. – М.: Химия, 1987. – 368 с.
- Шувалов В. В. Огаджанов Г. А., Голубятников В. А. Автоматизация производственных процессов в химической промышленности. – М.: Химия, 1991. – 480 с.
- Полоцкий Л. М., Лапшенков Г. И. Автоматизация химических производств. – М.: Химия, 1982. – 295 с.
- Исаев С. И., Кожинов И. А., Кофанов В. И., Леонтьев А. И. Теория процесса выпаривания: Учебник для технических университетов и вузов. / 2-е изд., испр. и доп. – М.: Изд-во МГТУ им. Н. Э. Баумана, 1997. – 683 с.
- Кафаров В. В., Глебов М. Б. Математическое моделирование основных процессов химических производств: Учебн. пособие для вузов. – М.: Высш. шк., 1991. – 400 с.
- Курко В. И. Методы исследования процесса выпаривания химических растворов. – М.: Химическая промышленность, 1977. – 191 с.
- Борисов Г. С., Брыков В. П., Дытнерский Ю. И. Основные процессы и аппараты химической технологии: Пособие по проектированию / Под ред. Дытнерского Ю. И., 2-е изд., перераб. и дополн. – М.: Химия, 1991. – 496 с.
- Дытнерский Ю. И. Процессы и аппараты химической технологии: Учебник для вузов. Изд. 2-е В 2-х кн.. Часть 2. Массообменные процессы и аппараты. – М.: Химия, 1995. – 368 с.: ил.
- Таубман Е. И. Выпаривание. – М., 1982.
- Иоффе И. Л. Проектирование процессов и аппаратов химической промышленности: Учебник для техникумов. – Л.: Химия, 1991. – 352 с.: ил.
- Гельперин Н. И. Основные процессы и аппараты химической технологии. – М.: Химия, 1981. – 812 с.:ил.
- Клюев А. С. Проектирование систем автоматизации технологических процессов: Справочное пособие. Изд. 2-е, перераб. и доп. – М.: Энергоатомиздат, 1990. – 464 с.: ил.
- Плановский А. Н., Николаев П. И. Процессы и аппараты химической и нефтехимической технологии:Учебник для вузов. Изд. 3-е, перераб. и доп. – М.: Химия, 1987. – 496 с.
- Плановский А. Н., Рамм В. М., Каган С. З. Процессы и аппараты химической технологии. Изд. 5-е. – М.: Химия, 1991. – 848 с.
- Гуров А. М., Починкин С. М. Автоматизация технологических процессов. – М.:Высшая школа, 1979. – 355 с.
- Колач Т. А., Радун Д. В. Выпарные станции. – М.: Машгиз, 1963. – 219 с.
- Гельперин Н. И., Пебалк В. Л., Костанян А. Е. Структура потоков и эффективность колонных аппаратов химической промышленности. – М.: Химия, 1977. – 262 с.