Реферат по теме выпускной работы
Содержание
- Введение
- 1. Актуальность темы
- 2. Цель и задачи исследования, планируемые результаты
- 3. Обзор исследований и разработок
- 3.1 Анализ технологического процесса просушки сыпучих материалов в сушильной барабанной печи как объекта автоматизации
- 3.2 Сушильная барабанная печь как объект автоматического управления
- 3.3 Анализ существующих разработок по автоматизации сушильной барабанной печи
- 3.4 Обоснование направления автоматизации сушильной барабанной печи
- 3.5 Алгоритмизация работы и схемные решения системы автоматического управления режимом сушильной барабанной печью
- Выводы
- Список источников
Введение
В различных отраслях народного хозяйства и обрабатывающей промышленности широко распространены процессы удаления жидкости (растворителей) с поверхности или из внутренних слоев различных материалов. В качестве удерживаемых материалами жидкостей могут быть вода, метанол, бензин, метаноло – ацетоновая смесь, бензино – изопропиловая смесь и т. п. Среди существующих способов обезвоживания материалов (сушка, отжатие, центрифугирование, фильтрование, отсасывание, поглощение химическими реагентами и т. д.) особое место занимает тепловая сушка, при которой удаление влаги из материала происходит в основном путем испарения.
Сушка – это тепловой процесс обезвоживания твердых материалов путем испарения влаги и отвода образующихся паров. При этом веществе происходит перенос тепла и диффузионное перемещение влаги. Продолжительность процесса сушки определяется интервалом времени, необходимым для понижения влагосодержания материала от начального значения до конечного.
1. Актуальность темы
Целью управления процесса сушки заключается в обеспечении высушивания поступающего влажного твердого материала до заданного влагосодержания.
Обезвоживание материалов, в том числе и сушка, предназначаются для улучшения их качества и долговечности, например при сушке древесины, увеличения теплотворности при сушке топлива, возможности длительного хранения при сушке пищевых продуктов и т. д. Поэтому в ряде случаев сушка сопровождается структурно – механическими, химическими, биохимическими, реологическими изменениями высушиваемого материала.
Скорость протекания этих процессов, степень их завершенности зависит не только от способа подвода теплоты к материалу, но и от режима сушки.
Различают сушку естественную (на открытом воздухе) и искусственную (в сушилках). При естественной сушке материал можно высушить только до влажности, близкий к равновесной. Преимущество искусственной сушки состоит в ее малой продолжительности и возможности регулирования конечной влажности материала. Аппараты, в которых осуществляют сушку, называют сушилками. По способу сообщения тепла различают конвективные, контактные, терморадиационные, сублимационные и высокочастотные сушилки. Дисперсные материалы, к которым относятся зернистые, порошкообразные, гранулированные, дробленные твердые, а также диспергированные жидкие и пастообразные продукты, в химической технологии высушивают, главным образом, конвективным способом.
Если соприкосновение высушиваемого материала с кислородом воздуха недопустимо или пары удаляемой влаги взрыво – или огнеопасны, то сушильным агентом служат инертные к высушиваемому материалу газы: азот, диоксид углерода, гелий и другие инертные газы или перегретый водяной пар.
2. Цель и задачи исследования, планируемые результаты
Цель исследования является повышение эффективности качественного технологического процесса просушки сыпучих материалов в сушильной барабанной печи путем разработки системы автоматического управления, а также контроля и регулирования основных технологических параметров данного объекта управления.
Основные задачи исследования:
- Анализ технологического процесса просушки сыпучих материалов сушильной барабанной печи как объекта автоматизации.
- Представление схемы сушильной барабанной печи как объекта автоматического управления;
- Анализ существующих разработок по автоматизации сушильной барабанной печи;
- Обоснование направления автоматизации сушильной барабанной печи;
- Алгоритмизация работы и схемные решения системы автоматического управления режимом сушильной барабанной печью.
3. Обзор исследований и разработок
3.1 Анализ технологического процесса просушки сыпучих материалов сушильной барабанной печи как объекта автоматизации
Главной целью управления процесса просушки сыпучих материалов в сушильной барабанной печи заключается в обеспечении высушивания поступающего влажного твердого материала до заданного влагосодержания. Основными возмущениями процесса являются изменение расхода, начальной влажности и дисперсного состава частиц твердого материала, а также изменение расхода и начальной температуры сушильного агента – теплоносителя. Основная регулируемая величина процесса – это остаточная влажность твердого материала, которая напрямую зависит от температуры при которой происходит сушка. Таким образом, для обеспечения надлежащего качества высушивания следует автоматизировать процесс управления технологическими режимами сушильной барабанной печи.
Критерием управления (показателем эффективности) процесса выступает параметр, определяющий качество продукта или его количество.
Температурный режим сушки регулируется в зависимости от влажности и температуры материалов, которые контролируются по пробам, отобранным через люк расширительной камеры.
После выхода на требуемый температурный режим контролируют влажность материала. Если она выше 7 % (требуемой влажности), то это означает, что исходная влажность материалов повышенная, и их надо сушить более чем за один пропуск чрез барабанную сушилку.
В зависимости от влажности и количества материала, будет меняться и количество газовоздушной смеси, необходимой для сушки. Поэтому, для стабильной работы сушильного оборудования, в частности, поддержания необходимой скорости газовоздушной смеси (разряжения в тракте), должна регулироваться и работа вытяжного вентилятора (дымососа), установленного после сушильного агрегата за циклоном.
На рис. 1 приведена конструкция сушильной барабанной печи
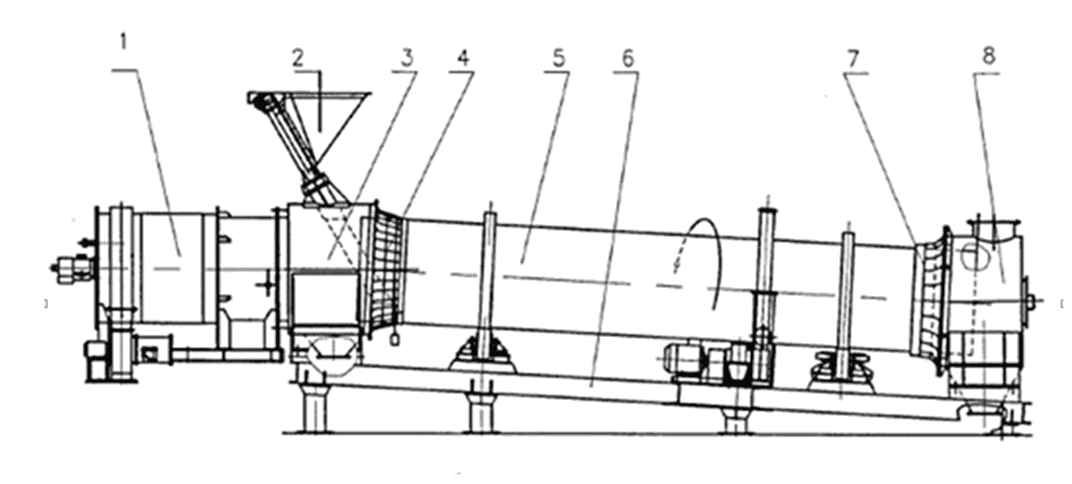
Рисунок 1 – Конструкция сушильной барабанной печи
Материал загружается в сушильный барабан (поз. 5) через винтовой питатель и трубу загрузочную, установленный на загрузочной камере (поз. 3). Барабанная сушилка установлена под углом 3° – 5° к горизонтали и может вращаться вокруг продольной оси со скоростью, задаваемой частотным преобразователем, которым можно регулировать скорость вращения приводного двигателя.
Материал последовательно проходит через эти составные части агрегата и по мере продвижения к камере выгрузочной (поз. 8) и из него испаряется влага. Теплоноситель, в данном случае газовоздушная смесь, образуемая в теплогенераторе (поз. 1), движется к камере выгрузочной под воздействием разряжения. Разряжение создается вытяжным вентилятором (дымососом), который не входит в состав сушильного агрегата и должен быть установлен после выгрузочной камеры. В данном технологическом процессе, сушка производится методом прямотока, то есть материал и теплоноситель двигаются в одну сторону.
Материал, поступивший в сушильный барабан, постоянно перемещается вдоль оси барабана, при этом перемешивается и постоянно находится в контакте с теплоносителем.
Для регулирования количества материала, подаваемого винтовым питателем (поз. 2), скорость вращения двигателя привода питателя винтового также регулируется частотным преобразователем.
По мере продвижения к камере выгрузочной, материал высушивается. Влага из материала уносится теплоносителем для очистки от пылевидной фракции материала, увлеченной теплоносителем.
Температура подаваемого из теплогенератора газовоздушной смеси должна быть не выше 900 °С. Температура отходящей газовоздушной смеси должна быть не ниже 100 °С, во избегании образования конденсата в разгрузочной части сушильного барабана. Влажность материала на входе в сушильный агрегат и выходе из него, должна периодически контролироваться для регулирования режима работы сушильного агрегата. Температурный режим сушки регулируется в зависимости от влажности и температуры материалов, которые контролируются по пробам, отобранным через люк расширительной камеры. После выхода на требуемый температурный режим контролируют влажность материала. Если она выше 7 % (требуемой влажности), то это означает, что исходная влажность материалов повышенная, и их надо сушить более чем за один пропуск через барабанную сушилку.
В зависимости от качества перерабатываемого сырья, его вида, должна быть подобрана наиболее оптимальная конструкция сушильного барабана, его размер, проведены необходимые теплотехнические расчеты. Барабаны могут иметь производительность от 150 кг до 100 т в час, от чего будут зависеть размеры загрузочной камеры, камеры выгрузки, мощность теплогенератора, особенности механизма пылегазоочистки, а также подачи и удаления теплоносителя. Такое оборудование может различаться по способу подачи материала (механической или пневматической), а также по количеству барабанов в установке (максимум три).
Чтобы проводить управление барабанной сушилкой, необходимо иметь определенный центральный пункт управления, с которого будет происходить дистанционное управление необходимыми технологическими параметрами, а также контроль расхода топлива и другими физическими величинами.
3.2 Сушильная барабанная печь как объект автомаматического управления
На рис. 2 представлена структурная схема сушильной барабанной печи как объекта автоматического управления
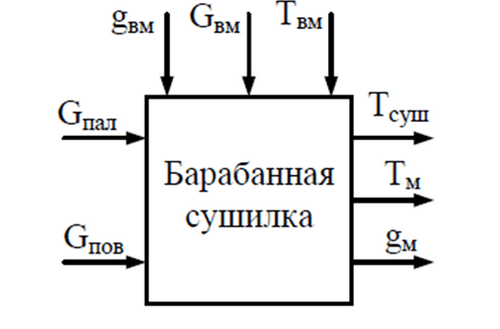
Рисунок 2 – Cушильная барабанная печь как объект автоматического управления
Влажность сухого материала gвм определяется, с одной стороны, количеством влаги, которая поступает с влажным материалом, а с другой стороны количеством влаги, которая удаляется из него в процессе сушения. Количество влаги, которая поступает с влажным материалом, зависит от расхода этого материала и его влажности, а также от расхода сушильного агента.
Разряжение Рвм в сушильной барабанной печи легко стабилизируется путем изменения расхода Gвм сушильного агента, который выводится из сушилки. Температура же определяется всеми имеющимися параметрами, и также интенсивностью процесса выпаривания влаги из материала. Стабилизировать ее можно путем изменения расхода Gпал или температуры Tсуш сушильного агента. Необходимо отметить, что диапазон изменения последнего параметра существенным образом ограничен, что объясняется требованиями техники безопасности.
Полнота сгорания топливного газа обеспечивается системой автоматического регулирования соотношение затрат топливного газа и первичного воздуха, управляющего подачей первичного воздуха в топку. При изменении теплоты сгорания топлива целесообразно корректировать это соотношение по содержанию кислорода в топочных газах.
Cформулируем требования к системе автоматического управления режимом работы сушильной барабанной печи на основании модели FURPS+, такие как: Functionlity – функциональность; Usability – применимость; Reliability – надежность; Performance – производительность; Supportability – пригодность к эксплуатации.
- Функциональность:
– сбор, первичная обработка, распределение и формирование информации, получаемой от датчиков технологических и энергетических параметров сушильной барабанной печи в виде аналоговых, цифровых и дискретных сигналов;
– представление информации и взаимодействие пользователей с программно – техническим комплексом сушильной барабанной печи;
– дистанционное управление приводами оборудования и исполнительных механизмов сушильной барабанной печи;
– автоматическое, программное управление сушильной барабанной печью;
– контроль разряжения после батарейных циклонов (P = 0, 5 кПа).
- Безопасность:
Все электротехнические изделия, используемые в системе управления сушильной барабанной печью, должны соответствовать ГОСТ 12.2.007–75, а средства вычислительной техники – по ГОСТ 25861–83, и имеют класс 1 защиты человека от поражения электрическим током. Все внешние элементы технических систем управления, находящиеся под напряжением, защищаются от случайного прикосновения.
- Применимость:
Рабочее место оператора системы управления сушильной барабанной печью должно содержать несколько рабочих станций, которые предназначены для:
– предоставления, хранения и обработки технологической информации;
– выполнение функций и задач расчетного характера;
- Надежность:
Программно – технический комплекс сушильной барабанной печи в части требований по надежности должен соответствовать ГОСТ 4.148–85, ГОСТ 24.70186 и ГОСТ 27.003–90.
- Производительность:
Пригодность к эксплуатации характеризуется:
– рабочая температура окружающей среды 5 – 50 °С;
– предельная температура 0 – 100 °С;
– относительная влажность воздуха 30 – 75 % при температуре 25 °С;
- Требования по массе, габаритам и степени защищенности корпуса
Узлы САУ должны являться изделиями заводского изготовления с типовыми или проектно–компонуемыми тактико–техническими, метрологическими и массогабаритными характеристиками. По степени защиты от воздействия окружающей среды:
– приборные шкафы КП ТМ – не ниже IP55(IP65);
– пульт управления – не ниже IP21;
– шкаф серверного оборудования – не ниже IP21;
– пылевлагозащита – IP31 (корпус защищает от проникновения части более 2, 5 мм частиц);
3.3 Анализ существующих разработок по автоматизации сушильной барабанной печи
Процесс сушки в сушильной барабанной печи как объект автоматизации описывается достаточно сложными дифференциальными уравнениями в частных производных. Для упрощения модели сушильного барабана по каналу «расход горячего воздуха – влажность материала на выходе» ее можно принять в виде апериодического звена второго порядка с чистым запаздыванием. При это следует отметить, что процесс сушки характеризуется значительной инерционностью. Возмущающими воздействиями при сушке являются изменения влажности и расхода материала на входе, параметров горячего воздуха, поступающего в сушильный барабан.
В системе управления режимом работы сушильной барабанной печи используется следующее оборудование:
– программируемый контроллер с модулями расширения Mitsubishi Electric, серии FX3U;
– графическая панель оператора WEINTEK, серии MT8000iЕ;
– температурный регулятор Autonics, серии TM2.
Программируемый контроллер Mitsubishi Electric, серии FX3U необходим для сбора, преобразования, обработки, хранения информации и выработки команд управления, имеющий конечное количество входов и выходов, подключенных к ним датчиков, исполнительных механизмов к сушильной печи, и предназначенный для работы в режимах реального времени. Усовершенствованный контроллер позволяет подключать к себе расширительные модули контроллеров прошлого поколения (FX0N, FX2N), так и модули нового поколения. При подключении модулей FX3U контроллер автоматически переключает свою коммутационную шину на высокоскоростной режим и обмен данным происходит на повышенной скорости. Модули FX0N, FX2N работают с контроллером на обычных скоростях.
Преобразователи частоты Mitsubishi Electric, серии FR–D740 – это устройства, предназначенные для преобразования переменного тока (напряжения) одной частоты в переменный ток (напряжение) другой частоты. Данное устройство необходимо для управления двигателем, предназначенный за вращения барабана сушильной печи. Устройство оснащено встроенной функцией обеспечения безопасной аварийной остановки, для проверки состояния компонентов и устранения неисправностей, инструментарий самодиагностики.
Графическая панель оператора WEINTEK, серии MT8000iЕ – это устройство, которое необходимо для отображения всех текущих измеряемых параметров определенного объекта управления. В отличие от классических мониторов, требующих подключения к компьютеру, панели оператора являются самостоятельными устройствами, которые напрямую связываются с компонентами АСУ ТП, визуализируют полученную информацию и передают контроллерам команды оператора. Взаимодействие панелей с управляемыми контроллерами и системами сбора данных осуществляется с помощью Ethernet, RS–232/485 или CAN–интерфейса. Интеллектуальные панели также могут протоколировать данные процесса, создавать отчеты и самостоятельно давать команды контроллерам на основании введенных оператором скриптов.
Температурный регулятор Autonics, серии TM2 предназначен для контроля температуры воздуха в помещении и для управления системой обогрева с возможностями программирования режимов работы на каждый день. Данное устройство позволяют использовать 4 или 2 канала для регулирования температуры с очень коротким интервалом измерения (100 мс и 50 мс, соответственно). Имеется возможность расширения системы до 31 модуля с синхронным регулированием температуры по 124 каналам без дополнительных источников питания и кабелей связи. Настройка параметров и управление с помощью ПК осуществляются по интерфейсам RS485 или USB. Различные дополнительные функции повышают общую надежность управления.
Степень автоматизации зависит от мощности, типа оборудования, заданных технологических параметров и должна обеспечивать надежную и эффективную работу оборудования в различных режимах без вмешательства обслуживающего персонала. Автоматическая система управления позволяет оператору своевременно принять правильное решение, обеспечивает быстроту выполнения необходимых операций и тем самым надежность и экономичность эксплуатации.
Существует АСУ ТП сушильной барабанной печи на основе базы оборудования серии Siemens. Внедрение данной системы позволяет увеличить производительность печи, сократить расход энергоресурурсов и сыпучих материалов; обеспечить требуемый режим просушки загрузочного материала.
Такая система способна выполнять следующие функции:
– автоматизация газовой горелки в соответствии с ГОСТ 21204;
– поддержания заданного разряжения в топке. Возможно применение аналоговых и дискретных датчиков разряжения. Работа с дымовой заслонкой или использование преобразователя частоты с дымососа;
– измерение влажности материала на конвейере загрузки и выгрузки. Поддержание влажности материала на конвейере выгрузки изменением частоты вращения привода вентилятора подачи вторичного воздуха. Корректировка регулирования по влажности материала на загрузке;
– регулирование подачи материала по сигналам датчиков влажности материала на конвейере загрузки и выгрузки изменением частоты вращения привода транспортера загрузки и барабана;
– контроль аварийных технологических параметров: температура отходящих газов на выходе из барабана, разряжение в топке, давление вторичного воздуха и т. д.;
– управление и регистрация всех технологических параметров сушильной барабанной печи на ПК оператора (АРМ).
САУ реализованная на базе регулирующего микропроцессорного контролера SIМАТIС S300 с необходимым набором модулей.
Также существует система автоматики безопасности и регулирования, которая построена на базе микропроцессорного устройства управления котлами, печами, сушилками (контроллере) АГАВА 6432.
Контроллер АГАВА 6432 при работе на газовом топливе в соответствии с руководством по эксплуатации на теплоустановку, техническими регламентами РФ и ТС в области безопасности, СП 62.13330.2011, ГОСТ Р 54961–2012, ГОСТ 21204–97 обеспечивает:
– повышение температуры теплоносителя на выходе;
– повышение температуры отходящих газов;
– отключение дутьевого вентилятора (при наличии);
– отключение дымососа (при наличии);
– остановку вращения барабана;
– прекращение подачи электроэнергии или исчезновении напряжения на устройствах дистанционного и автоматического управления и средствах измерения;
– послеаварийную вентиляцию топки не менее 10 минут.
Кроме реализации всех обязательных защит, система осуществляет:
– автоматическое плавное или позиционное регулирование температуры теплоносителя или материала;
– автоматическое плавное или позиционное регулирование соотношения топливо/ воздух с коррекцией по температуре воздуха, поступающего на горение;
– автоматическое плавное или позиционное регулирование разряжения в топке;
– автоматическое плавное или позиционное поддержание температуры в зоне подмеса;
– управление и защиту печи (барабана) при работе на резервном жидком топливе.
Для регистрации событий и основных технологических параметров котла в контроллере реализован электронный регистратор.
Блок управления технологическим режимом сушильной барабанной печи будет базироваться на микроконтроллере фирмы Atmell типа АТ90S8535, который выполняет функции по обработке принятых сигналов и на их основании выработке управляющих воздействий на внешние устройства с программой, заложенной в его памяти.
3.4 Обоснование направления автоматизации сушильной барабанной печи
К достоинствам сушильной барабанной печи следует отнести: быстроту сушки; относительную простоту конструкции; небольшую высоту (проще обслуживание и монтаж); относительно низкую стоимость; высокий термический КПД.
Вместе с тем, у сушильной барабанной печи имеются и недостатки: малое использование рабочего объема барабана; относительно высокий расход электроэнергии; большая занимаемая площадь; относительно низкое качество сушки (особенно по равномерности сушки).
При реализации систем автоматизации сушильной барабанной печи на предприятии «Донецкий металлургический завод» необходимо учитывать специфику объекта управления и контроля. Обеспечить гибкость системы, устойчивость и работоспособность в любых ситуациях. При проектировании системы автоматического управления необходимо обеспечить: снижение энергопотребления на сушку, уменьшение пересушивания материалов. Все эти критерии смогут обеспечить качество просушенного материала, при этом снижая его себестоимость.
Обычно стандартное САУ сушильной барабанной печи обеспечивает:
– дистанционное управление расходами воздуха на разбавление;
– контроль расходов природного газа и воздуха;
– возможность ручного управления подачи материала в загрузочную камеру;
– возможность аварийной остановки процесса по команде оператора.
Известным недостатком конструкции сушильной барабанной печи является неполное сгорание топлива, вследствие этого высокая загрязненность окружающей среды и некачественная обработка просушиваемого материала. Все дело в том, что на пламя горящего топлива попадает высушиваемый материал, и потом уносит с собой частицы топлива (природный газ), тем самым не давая догореть и гасит их, потому – что они падают совместно с высушиваемым материалом вниз. Затем частицы через вытяжную трубу попадают в атмосферу и создают шлейф дыма. И чтобы снизить задымленность и обеспечить полное сгорание топлива, в барабане вдоль его оси устанавливают лопастной конус, который состоит из прикрепленных к барабану лопастей, имеющих общее коническое направление с вершиной в сторону топки: каждая из лопастей повернута относительно образующей барабана в сторону направления вращения.
Общая коническая направленность установки лопастей обеспечивает горение факела без засыпания его высушиваемым материалом. Это обеспечивает попадание между стенками лопастей и барабаном горячего газа, а также просыпание попавшего в конус материала на поверхность барабана.
Для образования газовоздушной смеси, будет использоваться теплогенератор – воздухонагреватель. Основным преимуществом является возможность нагрева воздуха до 900 °С, экологически чистое сжигание газа и широкий диапазон тепловых мощностей. В состав теплогенератора входит микродиффузионная газовая горелка которая необходима для экологически чистого сжигания природного газа и всех синтетически – биологических смесей образующихся с материалов. Они обеспечивают устойчивое горение в диапазоне мощности от 5 до 120 % при коэффициентах избытка воздуха 0, 8…2, 0.
Принцип действия основан на струйном смешении природного газа с воздухом, тем самым образуя горячую смесь на срезе стабилизирующих процесс пилонов. Микродиффузионный процесс сжигания газа протекает в коротком факеле, обеспечивая высокую устойчивость горения к колебаниям давления газа в газопроводе, равномерное температурное поле в камере горения теплового агрегата и высокие экологические показатели.
Для того чтобы поддерживать разряжение в топке, будут применяться аналоговые и дискретные датчики разряжения. Для контроля данного параметра, предусматривается работа с дымовой заслонкой или использования преобразователя частоты для дымососа.
3.5 Алгоритмизация работы и схемные решения системы автоматического управления режимом сушильной барабанной печью
Блок – схема алгоритма управления процессом сушки сыпучих материалов в барабанной сушилке представлена на рис. 3.
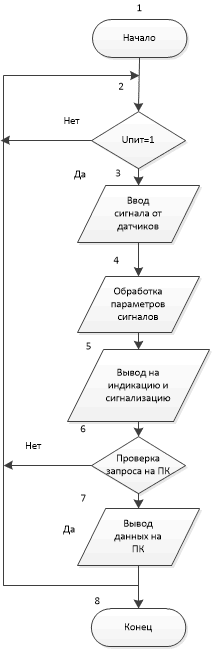
Рисунок 3 – Блок – схема алгоритма управления процессом сушки сыпучих материалов в сушильной барабанной печи
Работа блок – схемы происходит в следующем порядке:
– в блоке 1 происходит подача напряжения питания на блок управления и устройство начинает работу;
– в блоках 3 и 4 происходит опрос всех датчиков технологических параметров, ввод в микроконтроллер, полученной от них технологической информации, ее обработка. Происходит опрос датчиков и преобразователей с таких физических величин как давления, газ, воздух, температура, разряжение и т. д. Обработка с датчиков на преобразователи происходит в виде преобразования определенной физической величины в электронный унифицированный сигнал который в дальнейшем распространяется на блоки управления, показывающие контрольные регистрирующие приборы, задающие устройства и т. д.
– в блоке 5 идет визуализация полученной технологической информации. Все отображение сигналов и технологических параметров выводиться на контрольные регистрирующие приборы, а также на сигнализирующие приборы. В случае возникновения проблемы или неисправности, срабатывает звуковая или световая сигнализация, сигнал который в дальнейшем отправляются в высший уровень системы управления;
– в блоках 6 и 7 происходит проверка запроса от головного компьютера (высшего уровня системы управления) и вывод данных по внешним каналам связи на головной управляющий компьютер. Если полученные значения соответствуют заданным, то работа продолжается. В случае если значения не соответствует заданным, то необходимо уменьшить или увеличить подачу определенной физической величину к технологическому объекту в виде давления, газа или воздуха. Если полученные значения во время работы превышают требуемые, то клапан с трубопровода будет закрываться или регулироваться для уменьшения подачи требуемой физической величины.
На рис. 4 представлена блок – схема алгоритма управления расходами природного газа в сушильной барабанной печи.
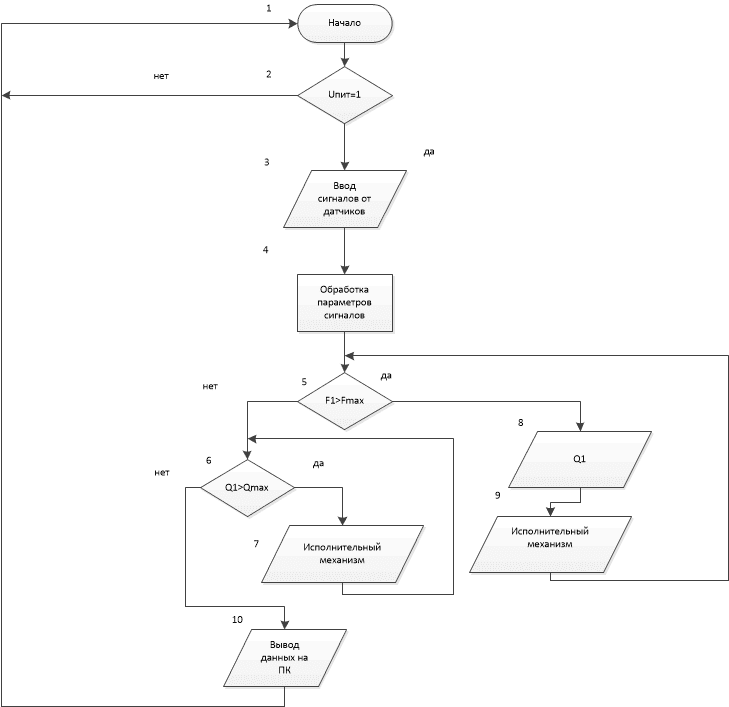
Рисунок 4 – Блок – схема алгоритма управления расходами природного газа и воздуха в сушильной барабанной печи
Процесс управления происходит следующим образом:
– блок 1 – 2 – ввод устройства в работу;
– блоки 3 – 4 – прием и обработка текущей информации с датчиков технологических параметров;
– блок 5 – сравнение текущего расхода газа и воздуха с уставкой по верхнему уровню;
– блоки 6 – 7 необходимы для формирования внешних сигналов управления на исполнительный механизм (исполнительный механизм газообразного топлива) на уменьшение расхода топлива;
– блоки 8 – 9 – поддержание изначальной по расходу топлива Q;
– блок 10 необходим для вывода полученных данных на головной персональный компьютер (ПК) о ходе процесса выполнения.
На рис. 5 представлена функциональная схема автоматизации сушильной барабанной печи
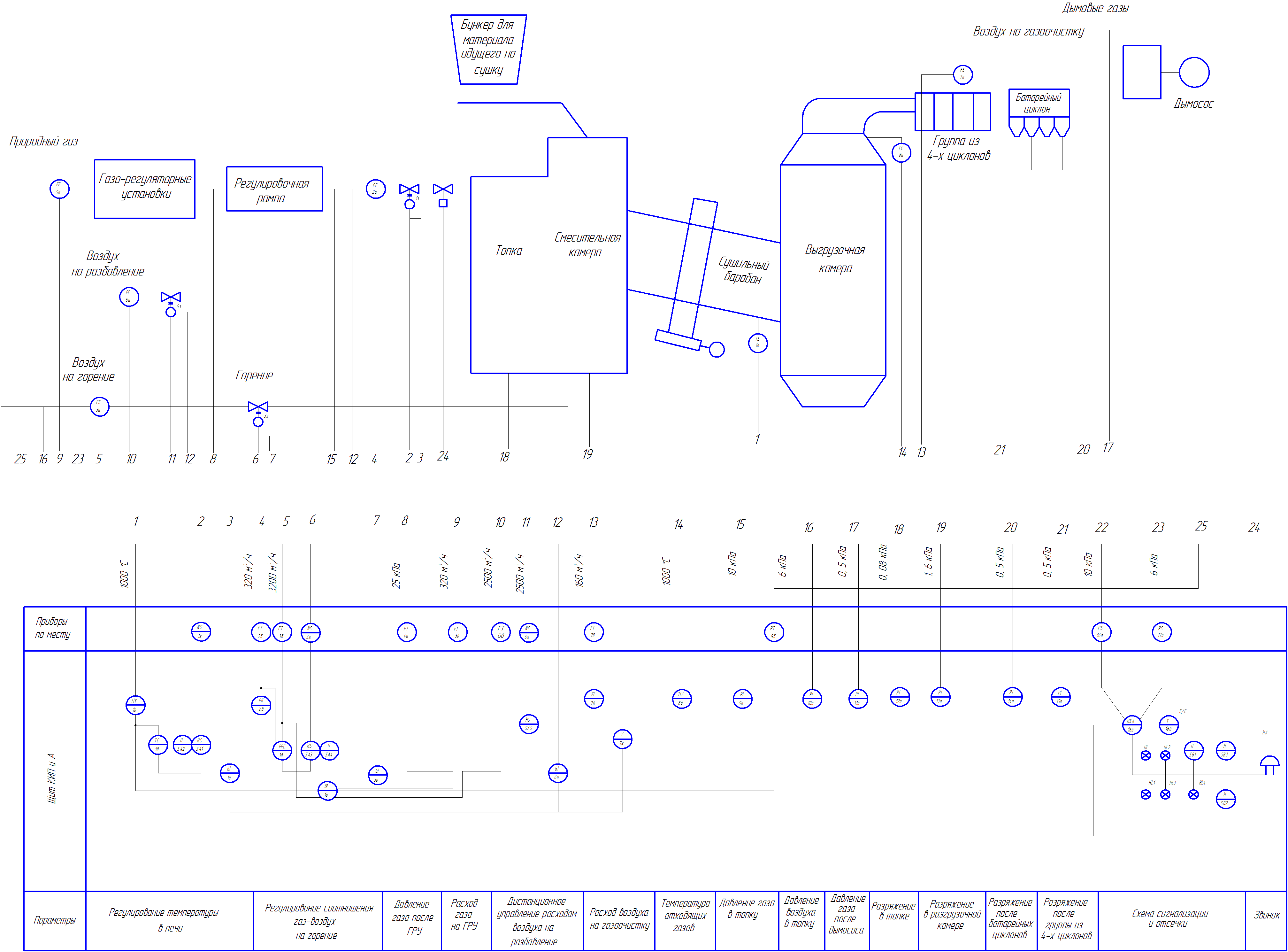
Рисунок 5 – Функциональная схема автоматизации сушильной барабанной печи
Управление технологическими параметрами сушильной барабанной печи осуществляется следующим образом:
- Регулирование температуры в печи. На барабанной печи устанавливается преобразователь термоэлектрический ТХА – 2388 (п. 1а), выходной сигнал в виде ЭДС поступает на вход измерительного многопредельного преобразователя МТМ – 402 – 01 – ХА (К) (п. 1б). В этот момент происходит преобразование термо – ЭДС в унифицированный токовый сигнал. Далее сигнал поступает на регулирующий прибор МИК – 51 (п. 1д) и одновременно поступает сигнал на регистратор контрольный 6 – канальный МТМ РЭ – 160 – 01 (п. 1о). Регулятор сравнивает заданное значение с текущим значением и вырабатывает управляющий сигнал, который поступает на два ключа УП5311 – 23 (п. SA1) и УП5314 – С256 (п. SA2), с помощью которого выбираются режимы регулирования. При автоматическом режиме, сигнал поступает на пускатель бесконтактный реверсивный ПБР – 2М (п. 1ж) и включающий механизм электрический однооборотный МЭО – 63 – 25 – 6, 3 (п. 1з), который в свою очередь перемещает регулирующий орган, установленного на трубопроводе природного газа. Контроль за положением регулирующего органа осуществляет дистанционный указатель положения МТМ – 103 (п. 1и).
- Контроль давления газа после ГРУ. Происходит измерение среды между газораспределительным устройством (ГРУ) и регулировочной рампой. Перед ГРУ проходит природный газ под высоким давлением, а после ГРУ, через регулировочную рампу проходит уже природный газ с низким давлением. Затем измеряемый параметр, а именно давление в 25 кПа, проходит через измерительный преобразователь давления «ЭЛЕМЕР – АИР – 10» (п. 4а), который преобразует поступившее давление в унифицированный выходной токовый сигнал и подает на регистратор электронный 6 – канальный МТМ РЭ – 160 – 01 (п. 1о). В самом регистраторе отображается вся необходимая информация о состоянии технологического параметра давления газа после ГРУ.
- Контроль расхода газа на ГРУ осуществляется следующим образом. На технологическом трубопроводе подачи природного газа установлено сужающее устройство – диафрагма камерная стандартная ДКС (п. 5а). С него поступает перепад давления 320 м3/ ч на измерительный преобразователь «ЭЛЕМЕР – АИР – 30» (п. 5б). С выхода преобразователя поступает на один из шести каналов регистрирующего прибора МТМ РЭ – 160 – 01 (п. 1о).
- Дистанционное управление расходом воздуха на разбавление. При подаче воздуха на разбавление, сам воздух попадает на диафрагму камерную стандартную ДКС (п. 6а). Затем поступает перепад давления, равный 2500 м3/ ч, на измерительный преобразователь «ЭЛЕМЕР – АИР – 30» (п. 6б). Унифицированный токовый сигнал поступает на регистрирующий прибор МТМ РЭ – 160 – 01 (п. 1о). С помощью переключателя УП5311 – 23 (п. SA5) производится переключение на дистанционное управление, в результате чего сигнал поступает на пускатель бесконтактный реверсивный ПБР – 2М (п. 6ж). Включается механизм электрический однооборотный МЭО – 63 – 25 – 6, 3 (п. 6з), затем подает сигнал на дистанционный указатель положения МТМ – 103 (п. 6и).
- На трубопроводе подачи природного газа, измеряемая среда (давление) поступает на измерительный преобразователь давления «ЭЛЕМЕР – АИР – 10» (п. 9б), который преобразует полученное давление в унифицированный токовый сигнал, который поступает на один из каналов электронного регистратора «МТМ РЭ – 160 – 01» (п. 1о).
- При контроле разряжения в топке, разряжения в разгрузочной камере, разряжения после батарейных циклонов и группы из 4 – х циклонов, необходим прибор для показания давления. Так как все перечисленные параметры измеряют давления, все будет поступать на такие тягонапоромеры, как показывающий мембранный тягонапоромер ТНМП – 100 (п. 11а, 12а, 13а, 14а, 15а).
На рис. 6 представлена структурная схема автоматического управления сушильной барабанной печи
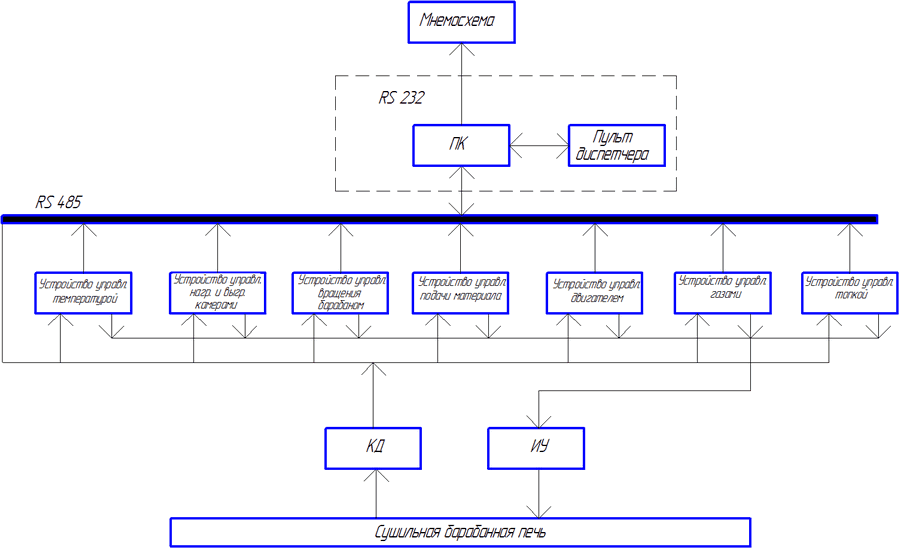
Рисунок 6 – Структурная схема управления АСУ ТП сушильной барабанной печи
Помимо самого управляемого объекта, мнемосхемы и пульта диспетчера, присутствуют следующие условные обозначения:
– КД – комплекс датчиков;
– БП – блок питания с напряжением U = 12 В;
– ИУ – исполнительные устройства;
– УУ – устройства управления;
– ПК – персональный компьютер.
Комплекс датчиков (КД) необходимы для контроля таких технологических параметров как температуры в печи, соотношения газ – воздуха на горение, давления газа после ГРУ, расхода воздуха на разбавление, разряжения и сигнализации. Они установлены на трубопроводах природного газа и первичного воздуха, на задвижках подачи топлива и т. д.
Устройства управления необходимы не только для получения информации от измеряемых величин с объекта управления, но и для преобразования полученной физической величины в электронный унифицированный сигнала для дальнейшего выведения его на показывающие, регистрирующие и задающие устройства, чтобы в дальнейшем вывести полученные сигналы через ЭВМ и отобразить их на мнемосхеме диспетчера.
В качестве датчиков для измерения расхода будут служить расходомеры переменного перепада давления с сужающим устройством в виде диафрагмы камерной стандартной ДКС.
Выводы
Магистерская работа посвящена актуальной научной задаче является повышение эффективности качественного технологического процесса просушки сыпучих материалов в сушильной барабанной печи путем разработки системы автоматического управления, а также контроля и регулирования основных технологических параметров данного объекта управления. В рамках проведенных исследований выполнен:
- Анализ технологического процесса просушки сыпучих материалов сушильной барабанной печи как объекта автоматизации.
- Рассмотрена сушильная барабанная печь как объект автоматического управления;
- Анализ существующих разработок по автоматизации сушильной барабанной печи;
- Обоснованы направления автоматизации сушильной барабанной печи
- Разработаны структурная схема управления, функциональная схема автоматизации, а также алгоритмы технологического процесса сушильной барабанной печи.
Дальнейшие исследования направлены на качественное совершенствование предложенных методов и разработок к усовершенстованию технологического процесса просушки сыпучих материалов в сушильной барабанной печи.
При написании данного реферата магистерская работа еще не завершена. Окончательное завершение: июнь 2023 года. Полный текст работы и материалы по теме могут быть получены у автора или его руководителя после указанной даты.
Список источников
- Глинков Г. М. АСУ ТП в черной металлургии: учебник для вузов. / Г. М. Глинков, В. А. Маковский – 2 – е изд., перераб. и доп. – М.: «Металлургия», 1999. – 310 с.
- Григорьева В. А., Зорина В. М. «Промышленная теплоэнергетика и теплотехника: Справочник». – М.: Энергоатомиздат, 1983. – 588 с.
- Громаков Е. И. Проектирование автоматизированных систем: учебно – методическое пособие. – Томск: Томский политехнический университет, 2010. – 173 с.
- Дубровский А. Х. Устройство электрической части систем автоматизации. – М.: Энергоатомиздат, 1984. – 264 с.
- Котов К. И., Шершевер М. А. Средства измерения, контроля и автоматизации технологических процессов. – М.: Металлургия, 1987. – 496 с.
- Михеев А. А. Методы и средства автоматизированного управления сушильной камерой (промышленность): дисс…. канд. техн. наук: 05. 13. 06/ Михеев Алексей Александрович. – Ируктск, 2015. – 133 с.
- Плетнев Г. П. Автоматическое регулирование и защита теплоэнергетических установок. – М.: Энергия, 1976
- Сергиенко А. Б. Цифровая обработка сигналов. – Спб.: Санкт – Петербург, 2002.
- Уэйкерли Д. Проектирование цифровых устройств / Д. Уэйкерли. – М.: Постмаркет, 2002. – Том 2. – 528 с.
- Михайлов Ю. Ю., Лабутин В. А., Быков И. Н., А.Ю. Михайлов. Моделирование процесса сушки в барабанной сушилке с учетом влияния продольного перемешивания сушильного агента. – Владимир: Владимирский государственный университет, 2010. – 3 с.
- Гартман Т. Н., Клушин Д. В. Основы компьютерного моделирования химико – технологических процессов: учеб. пособие для вузов. – М.: Академкнига, 2006.
- Питухин Е. А. Математическая модель управления качеством работы сушильной установки барабанного типа/// Труды Петрозаводского государственного университета. Вып. 6. 1997
- Кашьян Р. Л. Построение динамических стохастических моделей по экспериментальным данным. – М.: Наука, 1983.
- Vasiltsov I. Evolutionary technique to elementary coding of the internal states of the state machine / I. Vasiltsov // Proceedings of the 2002 NASA/DoD Conference on Evolvable Hardware. – 2002. – pp. 63–64.
- Шувалова Л.А. Структура программного комплекса синтеза и верификации моделей цифровых автоматов / Л.А. Шувалова, Д.Н. Моамар, Т.Ю. Уткина // Системи обробки інформації. – Харьков, 2010. – № 5. – С. 149–152.