Реферат за темою випускної роботи
Зміст
- Вступ
- 1. Актуальність теми
- 2. Мета та завдання дослідження, плановані результати
- 3. Огляд досліджень та розробок
- 3.1 Аналіз технологічного процесу просушування сипучих матеріалів у сушильній барабанній печі як об'єкта автоматизації
- 3.2 Сушильна барабанна пiчь як об'єкт автоматичного керування
- 3.3 Аналiз наявних розробок з автоматизацiї сушильної барабанної печі
- 3.4 Обґрунтування напряму автоматизацiї сушильної барабанної печі
- 3.5 Алгоритмізація роботы та схемнi рiшення системи автоматичного керування режимом управління сушильною барабанною піччю
- Висновки
- Список джерел
Вступ
У рiзних галузях промисловостi народного господарства та обробної промисловості широко поширені процеси видалення рідини (розчинників) з поверхні або з внутрішніх шарів різних матеріалів. Рідинами, що утримуються матеріалами, можуть бути вода, метанол, бензин, метаноло–ацетонова суміш, бензино–ізопропілова суміш тощо. Серед наявних способів зневоднення матеріалів (сушіння, віджимання, центрифугування, фільтрування, відсмоктування, поглинання хімічними реагентами тощо) особливе місце посідає теплове сушіння, за якого видалення вологи з матеріалу відбувається здебільшого шляхом випаровування.
Сушiння – це тепловий процес обробки твердих материалiв шляхом випаровування вологи та відведення парів, що утворюються. При цій речовині відбувається перенесення тепла і дифузійне переміщення вологи. Тривалiсть процесу сушiння визначається інтервалом часу, необхідним для зниження вологовмісту матеріалу від початкового значення до кінцевого.
1. Актуальність теми
Метою управління процесом сушіння є забезпечення висушування вологого твердого матеріалу, що надходить, до заданого вологовмісту.
Зневоднення матеріалів, зокрема й сушіння, призначаються для поліпшення їхньої якості та довговічності, наприклад під час сушіння деревини, збільшення теплоутворення під час сушіння палива, можливості тривалого зберігання під час сушіння харчових продуктів тощо. Тому в низці випадків сушіння супроводжується структурно–механічними, хімічними, біохімічними, біохімічними, реологічними змінами висушуваного матеріалу.
Швидкість протікання цих процесів, ступінь їхньої завершеності залежить не тільки від способу підведення теплоти до матеріалу, а й від режиму сушіння.
Розрізняють сушіння природне (на відкритому повітрі) і штучне (у сушарках). При природному сушінні матеріал можна висушити тільки до вологості, близької до рівноважної. Перевага штучного сушіння полягає в його малій тривалості та можливості регулювання кінцевої вологості матеріалу. Апарати, в яких здійснюють сушіння, називають сушарками. За способом повідомлення тепла розрізняють конвективні, контактні, терморадіаційні, сублімаційні та високочастотні сушарки. Дисперсні матеріали, до яких відносяться зернисті, порошкоподібні, гранульовані, подрібнені тверді, а також дисперговані рідкі та пастоподібні продукти, у хімічній технології висушують, головним чином, конвективним способом.
Якщо зіткнення висушуваного матеріалу з киснем повітря неприпустиме або пари вологи, що видаляється, вибухо– або вогненебезпечні, то сушильним агентом слугують інертні до висушуваного матеріалу гази: азот, діоксид вуглецю, гелій та інші інертні гази або перегріта водяна пара.
2. Мета та завдання дослідження, плановані результати
Метою дослідження є підвищення ефективності якісного технологічного процесу просушування сипких матеріалів у сушильній барабанній печі шляхом розроблення системи автоматичного керування, а також контролю та регулювання основних технологічних параметрів цього об'єкта керування.
Основні завдання дослідження:
- Аналіз технологічного процесу просушування сипучих матеріалів у сушильній барабанній печі як об'єкта автоматизації;
- Подання схеми сушильної барабанної печі як об'єкта автоматичного керування;
- Аналiз наявних розробок з автоматизацiї сушильної барабанної печі;
- Обґрунтування напряму автоматизацiї сушильної барабанної печі;
- Алгоритмізація роботы та схемнi рiшення системи автоматичного керування режимом управління сушильною барабанною піччю.
3. Огляд досліджень та розробок
3.1 Аналіз технологічного процесу просушування сипучих матеріалів у сушильній барабанній печі як об'єкта автоматизації
Головною метою управління процесом просушування сипучих матеріалів у сушильній барабанній печі є забезпечення висушування вологого твердого матеріалу, що надходить, до заданого вологовмісту. Основними обуреннями процесу є зміна витрати, початкової вологості та дисперсного складу частинок твердого матеріалу, а також зміна витрати та початкової температури сушильного агента – теплоносія. Основна регульована величина процесу – це залишкова вологість твердого матеріалу, яка безпосередньо залежить від температури, за якої відбувається сушіння. Таким чином, для забезпечення належної якості висушування слід автоматизувати процес управління технологічними режимами сушильної барабанної печі.
Критерієм управління (показником ефективності) процесу виступає параметр, що визначає якість продукту або його кількість.
Температурний режим сушiння регулюється залежно від вологості та температури матеріалів, які контролюються за пробами, відібраними через люк розширювальної камери.
Після виходу на необхідний температурний режим контролюють вологість матеріалу. Якщо вона вища за 7 % (необхідну вологість), то це означає, що вихідна вологість матеріалів підвищена, і їх треба сушити більш ніж за один пропуск через барабанну сушарку.
Залежно від вологості та кількості матеріалу, змінюватиметься і кількість газоповітряної суміші, необхідної для сушіння. Тому, для стабільної роботи сушильного обладнання, зокрема, підтримання необхідної швидкості газоповітряної суміші (розрядження в тракті), має регулюватися і робота витяжного вентилятора (димососа), встановленого після сушильного агрегату за циклоном.
На мал. 1 наведена конструкція сушильної барабанної печі.
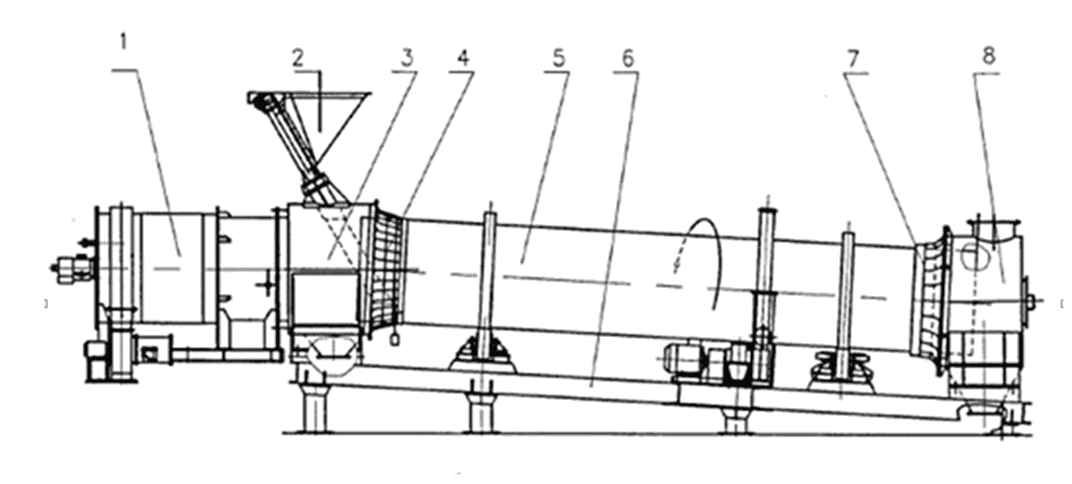
Малюнок 1 – Конструкція сушильної барабанної печі
Матеріал завантажується в сушильний барабан (поз. 5) через гвинтовий живильник і трубу завантажувальну, встановлений на завантажувальній камері (поз. 3). Барабанна сушарка встановлена під кутом 3° – 5° до горизонталі і може обертатися навколо поздовжньої осі зі швидкістю, що задається частотним перетворювачем, яким можна регулювати швидкість обертання приводного двигуна.
Матеріал послідовно проходить через ці складові частини агрегату і в міру просування до камери вивантажувальної (поз. 8) з нього випаровується волога. Теплоносій, у цьому разі газоповітряна суміш, утворена в теплогенераторі (поз. 1), рухається до камери вивантажувальної під впливом розрядження. Розрядження створюється витяжним вентилятором (димососом), який не входить до складу сушильного агрегату і має бути встановлений після вивантажувальної камери. У даному технологічному процесі сушіння проводиться методом прямотоку, тобто матеріал і теплоносій рухаються в один бік.
Сушка проводиться методом прямотоку.
Матеріал, що надійшов до сушильного барабана, постійно переміщується вздовж осі барабана, при цьому перемішується і постійно перебуває в контакті з теплоносієм.
Для регулювання кількості матеріалу, що подається гвинтовим живильником (поз. 2), швидкість обертання двигуна приводу живильника гвинтового також регулюється частотним перетворювачем.
У міру просування до камери вивантажувальної, матеріал висушується. Волога з матеріалу виноситься теплоносієм для очищення від пилоподібної фракції матеріалу, захопленої теплоносієм.
Температура газоповітряної суміші, що подається з теплогенератора, має бути не вище 900 °С. Температура газоповітряної суміші, що відходить, має бути не нижче 100 °С, щоб уникнути утворення конденсату в розвантажувальній частині сушильного барабана. Вологість матеріалу на вході в сушильний агрегат і виході з нього має періодично контролюватися для регулювання режиму роботи сушильного агрегату. Температурний режим сушіння регулюється залежно від вологості і температури матеріалів, які контролюються за пробами, відібраними через люк розширювальної камери. Після виходу на необхідний температурний режим контролюють вологість матеріалу. Якщо вона вища за 7 % (необхідної вологості), то це означає, що початкова вологість матеріалів підвищена, і їх треба сушити більш ніж за один пропуск через барабанну сушарку.
Залежно від якості сировини, що переробляється, її виду, має бути підібрана найбільш оптимальна конструкція сушильного барабана, його розмір, проведені необхідні теплотехнічні розрахунки. Барабани можуть мати продуктивність від 150 кг до 100 т на годину, від чого залежатимуть розміри завантажувальної камери, камери розвантаження, потужність теплогенератора, особливості механізму пилогазоочищення, а також подачі й видалення теплоносія. Таке обладнання може розрізнятися за способом подачі матеріалу (механічної або пневматичної), а також за кількістю барабанів в установці (максимум три).
Щоб проводити управління барабанною сушаркою, необхідно мати певний центральний пункт управління, з якого відбуватиметься дистанційне керування необхідними технологічними параметрами, а також контроль витрат палива та іншими фізичними величинами.
3.2 Сушильна барабанна піч як об'єкт автоматичного керування
На мал. 2 наведена структурна схема сушильної барабанної печі як об'єкта автоматичного керування.

Малюнок 2 – Сушильна барабанна піч як об'єкт автоматичного керування
Вологiсть сухого матерiалу gвм визначається, з одного боку, кількістю вологи, що надходить із вологим матеріалом, а з іншого боку кількістю вологи, що видаляється з нього в процесі сушіння. Кiлькiсть вологостi, яка надходить з вологим матерiалом, залежить вiд витрати цього матерiалу та його вологостi, а також вiд від витрати сушильного агента.
Розрядження Рвм у сушильній барабанній печі легко стабілізується шляхом зміни витрати Gвм сушильного агенту, який виводиться із сушарки. Температура ж визначається всіма наявними параметрами, і також інтенсивністю процесу випаровування вологи з матеріалу. Стабілізувати її можна шляхом зміни витрати Gпал або температури Tсуш сушильного агента. Необхiдно відзначити, що діапазон зміни останнього параметра істотно обмежений, що пояснюється вимогами техніки безпеки.
Повнота згоряння паливного газу забезпечується системою автоматичного регулювання співвідношення витрат паливного газу та первинного повітря, що керує подачею первинного повітря в топку. При зміні теплоти згоряння палива доцільно коригувати це співвідношення за вмістом кисню в топкових газах.
Сформулюємо вимоги до системи автоматичного керування режимом роботи сушильної барабанної печі на підставі моделі FURPS+, такі як: Functionlity–функціональність; Usability – застосовність; Reliability – надійність; Performance – продуктивність; Supportability – придатність до експлуатації.
- Функціональність:
– збір, первинне опрацювання, розподіл і формування інформації, одержуваної від датчиків технологічних і енергетичних параметрів сушильної барабанної печі у вигляді аналогових, цифрових і дискретних сигналів;
– подання інформації та взаємодія користувачів з програмно – технічним комплексом сушильної барабанної печі;
– дистанційне керування приводами обладнання та виконавчих механізмів сушильної барабанної печі;
– автоматичне, програмне керування сушильною барабанною піччю;
– контроль розрядження після батарейних циклонів (P = 0,5 кПа).
- Безпека:
Усі електротехнічні вироби, що використовуються в системі керування сушильною барабанною піччю, повинні відповідати ГОСТ 12.2.007–75, а засоби обчислювальної техніки – за ГОСТ 25861–83, і мають клас 1 захисту людини від ураження електричним струмом. Усі зовнішні елементи технічних систем керування, що перебувають під напругою, захищаються від випадкового дотику.
- Застосовність:
Робоче місце оператора системи керування сушильною барабанною піччю повинне містити кілька робочих станцій, які призначені для:
– надання, зберігання та обробки технологічної інформації;
– виконання функцій і завдань розрахункового характеру;
- Надійність:
Програмно–технічний комплекс сушильної барабанної печі в частині вимог щодо надійності повинен відповідати ГОСТ 4. 148–85, ГОСТ 24. 701–86 і ГОСТ 27. 003–90.
- Продуктивність:
Придатність до експлуатації характеризується:
– робоча температура навколишнього середовища 5 – 50 °С;
– гранична температура 0 – 100 °С;
– відносна вологість повітря 30 – 75 % за температури 25 °С;
- Вимоги щодо маси, габаритів і ступеня захищеності корпусу
Вузли САУ повинні бути виробами заводського виготовлення з типовими або проєктно–компонованими тактико–технічними, метрологічними та масогабаритними характеристиками. За ступенем захисту від впливу навколишнього середовища:
– приладові шафи КП ТМ – не нижче IP55(IP65);
– пульт керування – не нижче IP21;
– шафа серверного обладнання – не нижче IP21;
– пиловологозахист – IP31 (корпус захищає від проникнення частини більш ніж 2,5 мм частинок);
3.3 Аналiз наявних розробок з автоматизацiї сушильної барабанної печі
Процес сушіння в сушильній барабанній печі як об'єкт автоматизації описується доволі складними диференціальними рівняннями в приватних похідних. Для спрощення моделі сушильного барабана по каналу „витрата гарячого повітря – вологість матеріалу на виході“ її можна прийняти у вигляді аперіодичної ланки другого порядку з чистим запізнюванням. При цьому слід зазначити, що процес сушіння характеризується значною інерційністю. Збурхливими впливами під час сушіння є зміни вологості та витрати матеріалу на вході, параметрів гарячого повітря, що надходить у сушильний барабан.
У системі управління режимом роботи сушильної барабанної печі використовується таке обладнання:
– програмований контролер із модулями розширення Mitsubishi Electric, серiї FX3U;
– графічна панель оператора WEINTEK, серiї MT8000iЕ;
– температурний регулятор Autonics, серiї TM2.
Програмований контролер Mitsubishi Electric, серії FX3U, необхідний для збору, перетворення, оброблення, обробки, зберігання інформації та вироблення команд керування, що має кінцеву кількість входів і виходів, під'єднаних до них датчиків, виконавчих механізмів до сушильної печі, і призначений для роботи в режимах реального часу. Вдосконалений контролер дає змогу під'єднувати до себе розширювальні модулі контролерів минулого покоління (FX0N, FX2N), так і модулі нового покоління. Під час під'єднання модулів FX3U контролер автоматично перемикає свою комутаційну шину на високошвидкісний режим і обмін даними відбувається на підвищеній швидкості. Модулi FX0N, FX2N працюють із контролером на звичайних швидкостях.
Перетворювачі частоти Mitsubishi Electric, серії FR–D740 – це пристрої, призначені для перетворення змінного струму (напруги) однієї частоти на змінний струм (напругу) іншої частоти. Цей пристрій необхідний для керування двигуном, призначений для обертання барабана сушильної печі. Пристрій оснащений вбудованою функцією забезпечення безпечної аварійної зупинки, для перевірки стану компонентів і усунення несправностей, інструментарій самодіагностики.
Графічна панель оператора WEINTEK, серії MT8000iЕ – це пристрій, який необхідний для відображення всіх поточних вимірюваних параметрів певного об'єкта управління. На відміну від класичних моніторів, які потребують під'єднання до комп'ютера, панелі оператора є самостійними пристроями, що безпосередньо зв'язуються з компонентами АСУ ТП, візуалізують отриману інформацію та передають контролерам команди оператора. Взаємодія панелей з керованими контролерами і системами збору даних здійснюється за допомогою Ethernet, RS–232/485 або CAN–інтерфейсу. Інтелектуальні панелі також можуть протоколювати дані процесу, створювати звіти і самостійно давати команди контролерам на підставі введених оператором скриптів.
Температурний регулятор Autonics, серії TM2, призначений для контролю температури повітря в приміщенні та для керування системою обігріву з можливостями програмування режимів роботи на кожен день. Цей пристрій дає змогу використовувати 4 або 2 канали для регулювання температури з дуже коротким інтервалом вимірювання (100 мс і 50 мс, відповідно). Є можливість розширення системи до 31 модуля з синхронним регулюванням температури по 124 каналах без додаткових джерел живлення і кабелів зв'язку. Налаштування параметрів і керування за допомогою ПК здійснюються за інтерфейсами RS485 або USB. Різні додаткові функції підвищують загальну надійність керування.
Ступінь автоматизації залежить від потужності, типу обладнання, заданих технологічних параметрів і має забезпечувати надійну та ефективну роботу обладнання в різних режимах без втручання обслуговуючого персоналу. Автоматична система керування дає змогу оператору своєчасно прийняти правильне рішення, забезпечує швидкість виконання необхідних операцій і тим самим надійність та економічність експлуатації.
Існує АСУ ТП сушильної барабанної печі на основі бази обладнання серії Siemens. Впровадження цієї системи дає змогу збільшити продуктивність печі, скоротити витрату енергоресурсів і сипучих матеріалів; забезпечити потрібний режим просушування завантажувального матеріалу.
Система сушильної барабанної печі.
Така система здатна виконувати такі функції:
– автоматизація газового пальника відповідно до ГОСТ 21204;
– підтримання заданого розрядження в топці. Можливе застосування аналогових і дискретних датчиків розрядження. Робота з димовою заслінкою або використання перетворювача частоти з димососа;
– вимірювання вологості матеріалу на конвеєрі завантаження і вивантаження. Підтримання вологості матеріалу на конвеєрі вивантаження зміною частоти обертання приводу вентилятора подачі вторинного повітря. Коригування регулювання за вологістю матеріалу на завантаженні;
– регулювання подачі матеріалу за сигналами датчиків вологості матеріалу на конвеєрі завантаження і вивантаження зміною частоти обертання приводу транспортера завантаження і барабана;
– контроль аварійних технологічних параметрів: температура газів, що відходять, на виході з барабана, розрядження в топці, тиск вторинного повітря тощо;
– управління і реєстрація всіх технологічних параметрів сушильної барабанної печі.
САУ реалізована на базі регулюючого мікропроцесорного контролера SIМАТIС S300 з необхідним набором модулів.
Також існує система автоматики безпеки та регулювання, яка побудована на базі мікропроцесорного пристрою керування котлами, печами, сушарками (контролера) АГАВА 6432.
Контролер АГАВА 6432 під час роботи на газовому паливі відповідно до керівництва з експлуатації на теплоустановку, технічних регламентів РФ і ТЗ у сфері безпеки, СП 62.13330.2011, СП 62.13330.2011, ДСТУ Р 54961–2012, ДСТУ 21204–97 забезпечує:
– підвищення температури теплоносія на виході;
– підвищення температури газів, що відходять;
– вимкнення дуттьового вентилятора (за наявності);
– вимкнення димососа (за наявності);
– зупинку обертання барабана;
– припинення подачі електроенергії або зникнення напруги на пристроях дистанційного й автоматичного керування та засобах вимірювання;
– післяаварійну вентиляцію топки не менше 10 хвилин.
Крім реалізації всіх обов'язкових захистів, система здійснює:
– автоматичне плавне або позиційне регулювання температури теплоносія або матеріалу;
– автоматичне плавне або позиційне регулювання співвідношення паливо/повітря з корекцією за температурою повітря, що надходить на горіння;
– автоматичне плавне або позиційне регулювання розрядження в топці;
– автоматичне плавне або позиційне підтримання температури в зоні підмішування;
– керування та захист печі (барабана) під час роботи на резервному рідкому паливі.
Для реєстрації подій та основних технологічних параметрів котла в контролері реалізовано електронний реєстратор.
Блок керування технологічним режимом сушильної барабанної печі базуватиметься на мікроконтролері фірми Atmell типу АТ90S8535, що виконує функції з оброблення прийнятих сигналів і на їхній підставі вироблення керувальних впливів на зовнішні пристрої за програмою, закладеною в його пам'яті.
.3.4 Обґрунтування напряму автоматизацiї сушильної барабанної печі
До переваг сушильної барабанної печі слід віднести: швидкість сушіння; відносну простоту конструкції; невелику висоту (простіше обслуговування і монтаж); відносно низьку вартість; високий термічний ККД.
Водночас у сушильної барабанної печі є й недоліки: мале використання робочого об'єму барабана; відносно висока витрата електроенергії; велика площа, яку займає; відносно низька якість сушіння (особливо за рівномірністю сушіння).
Під час реалізації систем автоматизації сушильної барабанної печі на підприємстві „Донецький металургійний завод“ необхідно враховувати специфіку об'єкта управління і контролю. Забезпечити гнучкість системи, стійкість і працездатність у будь–яких ситуаціях. Під час проєктування системи автоматичного керування необхідно забезпечити: зниження енергоспоживання на сушіння, зменшення пересушування матеріалів. Усі ці критерії зможуть забезпечити якість просушеного матеріалу, при цьому знижуючи його собівартість.
Зазвичай стандартна САУ сушильної барабанної печі забезпечує:
– дистанційне керування витратами повітря на розведення;
– контроль витрат природного газу і повітря;
– можливість ручного управління подачі матеріалу в завантажувальну камеру;
– можливість аварійного зупинення процесу за командою оператора.
Відомим недоліком конструкції сушильної барабанної печі є неповне згоряння палива, внаслідок цього високе забруднення довкілля і неякісна обробка матеріалу, який просушується. Річ у тім, що на полум'я палаючого палива потрапляє висушуваний матеріал, і потім забирає з собою частинки палива (природний газ), тим самим не даючи догоріти і гасить їх, бо вони падають разом із висушуваним матеріалом донизу. Потім частинки через витяжну трубу потрапляють в атмосферу і створюють шлейф диму. І щоб знизити задимленість і забезпечити повне згоряння палива, у барабані вздовж його осі встановлюють лопатевий конус, який складається з прикріплених до барабана лопатей, що мають загальний конічний напрямок з вершиною у бік топки: кожна з лопатей повернута відносно твірної частини барабана у бік напряму обертання.
Сукупність лопатей, що обертаються, має загальний конічний напрямок з вершиною у бік топки: кожна з лопатей повернута щодо твірної частини барабана у бік напрямку обертання.
Загальна конічна спрямованість установки лопатей забезпечує горіння факела без засипання його висушуваним матеріалом. Це забезпечує потрапляння між стінками лопатей і барабаном гарячого газу, а також просипання матеріалу, що потрапив у конус, на поверхню барабана.
Для утворення газоповітряної суміші використовуватиметься теплогенератор – повітронагрівач. Основною перевагою є можливість нагрівання повітря до 900 °С, екологічно чисте спалювання газу та широкий діапазон теплових потужностей. До складу теплогенератора входить мікродифузійний газовий пальник, який необхідний для екологічно чистого спалювання природного газу і всіх синтетично–біологічних сумішей, що утворюються з матеріалів. Вони забезпечують стійке горіння в діапазоні потужності від 5 до 120 % при коефіцієнтах надлишку повітря 0,8...2,0.
Принцип дії ґрунтується на струменевому змішуванні природного газу з повітрям, тим самим утворюючи гарячу суміш на зрізі пілонів, що стабілізують процес. Мікродифузійний процес спалювання газу протікає в короткому факелі, забезпечуючи високу стійкість горіння до коливань тиску газу в газопроводі, рівномірне температурне поле в камері горіння теплового агрегату і високі екологічні показники.
Для того щоб підтримувати розрядження в топці, застосовуватимуться аналогові та дискретні датчики розрядження. Для контролю цього параметра передбачається робота з димовою заслінкою або використання перетворювача частоти для димососа.
3.5 Алгоритмізація роботы та схемнi рiшення системи автоматичного керування режимом управління сушильною барабанною піччю
Блок–схему алгоритму керування процесом сушіння сипучих матеріалів у барабанній сушарці подано на мал. 3.

Малюнок 3 – Блок–схема алгоритму керування процесом сушіння сипучих матеріалів у сушильній барабанній печі
Робота блок–схеми відбувається в такому порядку:
– у блоці 1 відбувається подача напруги живлення на блок управління і пристрій починає роботу;
– у блоках 3 і 4 відбувається опитування всіх датчиків технологічних параметрів, введення в мікроконтролер отриманої від них технологічної інформації, її обробка. Відбувається опитування датчиків і перетворювачів з таких фізичних величин, як тиск, газ, повітря, температура, розрядження тощо. Обробка з датчиків на перетворювачі відбувається у вигляді перетворення певної фізичної величини на електронний уніфікований сигнал, який надалі поширюється на блоки керування, показуючі контрольні реєструвальні прилади, задавальні пристрої тощо.
– у блоці 5 йде візуалізація отриманої технологічної інформації. Усе відображення сигналів і технологічних параметрів виводитися на контрольні прилади, що реєструють, а також на прилади, що сигналізують. У разі виникнення проблеми або несправності, спрацьовує звукова або світлова сигналізація, сигнал, який надалі надсилається на вищий рівень системи управління;
– у блоках 6 і 7 відбувається перевірка запиту від головного комп'ютера (вищого рівня системи управління) і виведення даних зовнішніми каналами зв'язку на головний керуючий комп'ютер. Якщо отримані значення відповідають заданим, то робота триває. У разі якщо значення не відповідають заданим, то необхідно зменшити або збільшити подачу певної фізичної величини до технологічного об'єкта у вигляді тиску, газу або повітря. Якщо отримані значення під час роботи перевищують необхідні, то клапан із трубопроводу закриватиметься або регулюватиметься для зменшення подачі необхідної фізичної величини.
На мал. 4 представлено блок–схему алгоритму керування витратами природного газу в сушильній барабанній печі.

Малюнок 4 – Блок–схема алгоритму керування витратами природного газу і повітря в сушильній барабанній печі
Процес управління відбувається таким чином:
– блок 1 – 2 – введення пристрою в роботу;
– блоки 3 – 4 – приймання та оброблення поточної інформації з датчиків технологічних параметрів;
– блок 5 – порівняння поточної витрати газу і повітря з уставкою за верхнім рівнем;
– блоки 6 – 7 необхідні для формування зовнішніх сигналів керування на виконавчий механізм (виконавчий механізм газоподібного палива) на зменшення витрати палива;
– блоки 8 – 9 – підтримання початкової за витратою палива Q;
– блок 10 необхідний для виведення отриманих даних на головний персональний комп'ютер (ПК) про перебіг процесу виконання.
На мал. 5 представлено функціональну схему автоматизації сушильної барабанної печі.

Малюнок 5 – Функціональна схема автоматизації сушильної барабанної печі
Керування технологічними параметрами сушильної барабанної печі здійснюється таким чином:
- Регулювання температури в печі. На барабанній печі встановлюється перетворювач термоелектричний ТХА – 2388 (п. 1а), вихідний сигнал у вигляді ЕРС надходить на вхід вимірювального багатограничного перетворювача МТМ – 402 – 01 – ХА (К) (п. 1б). У цей момент відбувається перетворення термо–ЕДС в уніфікований струмовий сигнал. Далі сигнал надходить на регулювальний прилад МІК–51 (п. 1д) і одночасно надходить сигнал на реєстратор контрольний 6–канальний МТМ РЕ–160–01 (п. 1о). Регулятор порівнює задане значення з поточним значенням і виробляє керувальний сигнал, який надходить на два ключі УП5311–23 (п. SA1) і УП5314–С256 (п. SA2), за допомогою якого вибираються режими регулювання. За автоматичного режиму сигнал надходить на пускач безконтактний реверсивний ПБР–2М (п. 1ж), який вмикає механізм електричний однооборотний МЕО–63–25–6,3 (п. 1з), що, своєю чергою, переміщає регулювальний орган, встановлений на трубопроводі природного газу. Контроль за положенням регулювального органу здійснює дистанційний покажчик положення МТМ – 103 (п. 1і).
- Контроль тиску газу після ГРУ. Відбувається вимірювання середовища між газорозподільним пристроєм (ГРУ) і регулювальною рампою. Перед ГРУ проходить природний газ під високим тиском, а після ГРУ, через регулювальну рампу, проходить уже природний газ із низьким тиском. Потім вимірюваний параметр, а саме тиск у 25 кПа, проходить через вимірювальний перетворювач тиску „ЕЛЕМЕР – АІР – 10“ (п. 4а), який перетворює тиск, що надійшов, на уніфікований вихідний струмовий сигнал і подає на реєстратор електронний 6–канальний МТМ РЕ–160–01 (п. 1о). У самому реєстраторі відображається вся необхідна інформація про стан технологічного параметра тиску газу після ГРУ.
- Контроль витрати газу на ГРУ здійснюється таким чином. На технологічному трубопроводі подачі природного газу встановлено звужувальний пристрій – діафрагма камерна стандартна ДКС (п. 5а). З нього надходить перепад тиску 320 м3/год на вимірювальний перетворювач „ЕЛЕМЕР – АІР – 30“ (п. 5б). З виходу перетворювача надходить на один із шести каналів реєструвального приладу МТМ РЕ – 160 – 01 (п. 1о).
- Дистанційне керування витратою повітря на розведення. Під час подавання повітря на розведення, саме повітря потрапляє на діафрагму камерну стандартну ДКС (п. 6а). Потім надходить перепад тиску, що дорівнює 2500 м3/год, на вимірювальний перетворювач „ЕЛЕМЕР – АІР – 30 “ (п. 6б). Уніфікований струмовий сигнал надходить на реєструвальний прилад МТМ РЕ – 160 – 01 (п. 1о). За допомогою перемикача УП5311 – 23 (п. SA5) здійснюють перемикання на дистанційне керування, у результаті чого сигнал надходить на пускач безконтактний реверсивний ПБР – 2М (п. 6ж). Вмикається механізм електричний однооборотний МЕО – 63 – 25 – 6,3 (п. 6з), потім подає сигнал на дистанційний покажчик положення МТМ – 103 (п. 6і).
- На трубопроводі подачі природного газу вимірюване середовище (тиск) надходить на вимірювальний перетворювач тиску „ЕЛЕМЕР – АІР – 10“ (п. 9б), який перетворює отриманий тиск на уніфікований струмовий сигнал, що надходить на один із каналів електронного реєстратора „МТМ РЕ–160–01“ (п. 1о).
- Під час контролю розрядження в топці, розрядження в розвантажувальній камері, розрядження після батарейних циклонів і групи з 4–х циклонів, необхідний прилад для показання тиску. Оскільки всі перераховані параметри вимірюють тиску, все буде надходити на такі тягонапороміри, як показуючий мембранний тягонапоромір ТНМП – 100 (п. 11а, 12а, 13а, 14а, 15а).
На мал. 6 наведено структурну схему автоматичного керування сушильною барабанною піччю

Малюнок 6 – Структурна схема керування АСУ ТП сушильної барабанної печі
Крім самого керованого об'єкта, мнемосхеми і пульта диспетчера, присутні такі умовні позначення:
– КД – комплекс датчиків;
– БЖ – блок живлення з напругою U = 12 В;
– ІУ – виконавчі пристрої;
– ПУ – пристрої керування;
– ПК – персональний комп'ютер;
– ПК – персональний комп'ютер.Комплекс датчиків (КД) необхідний для контролю таких технологічних параметрів, як температура в печі, співвідношення газ – повітря на горіння, тиск газу після ГРУ, витрата повітря на розрідження, розрядження і сигналізації. Вони встановлені на трубопроводах природного газу і первинного повітря, на засувках подачі палива тощо.
Пристрої керування необхідні не тільки для отримання інформації від вимірюваних величин з об'єкта керування, а й для перетворення отриманої фізичної величини в електронний уніфікований сигнал для подальшого виведення його на показувальні, реєструвальні та задавальні пристрої, щоб надалі вивести отримані сигнали через ЕОМ та відобразити їх на мнемосхемі диспетчера.
Як датчики для вимірювання витрати слугуватимуть витратоміри змінного перепаду тиску зі звужувальним пристроєм у вигляді діафрагми камерної стандартної ДКС.
Висновки
Магістерська робота присвячена актуальному науковому завданню – підвищенню ефективності якісного технологічного процесу просушування сипких матеріалів у сушильній барабанній печі шляхом розроблення системи автоматичного керування, а також контролю та регулювання основних технологічних параметрів даного об'єкта керування. У рамках проведених досліджень виконано:
- Аналіз технологічного процесу просушування сипучих матеріалів у сушильній барабанній печі як об'єкта автоматизації;
- Розглянута сушильна барабанна піч як об'єкт автоматичного керування;
- Анализ существующих разработок по автоматизации сушильной барабанной печи;
- Обґрунтовано напрями автоматизації сушильної барабанної печі;
- Розроблено структурну схему керування, функціональну схему автоматизації, а також алгоритми технологічного процесу сушильної барабанної печі.
Подальші дослідження спрямовані на якісне вдосконалення запропонованих методів і розробок до удосконалення технологічного процесу просушування сипучих матеріалів у сушильній барабанній печі.
Пiд час написання написання цього реферату магистерська робота ще не завершена. Остаточне завершення: червень 2023 року. Пiвний текст роботы та матерiали за темою можуть бути отримані в автора або його керівника після зазначеної дати.
Список джерел
- Глинков Г. М. АСУ ТП в черной металлургии: учебник для вузов. / Г. М. Глинков, В. А. Маковский – 2 – е изд., перераб. и доп. – М.: «Металлургия», 1999. – 310 с.
- Григорьева В. А., Зорина В. М. «Промышленная теплоэнергетика и теплотехника: Справочник». – М.: Энергоатомиздат, 1983. – 588 с.
- Громаков Е. И. Проектирование автоматизированных систем: учебно – методическое пособие. – Томск: Томский политехнический университет, 2010. – 173 с.
- Дубровский А. Х. Устройство электрической части систем автоматизации. – М.: Энергоатомиздат, 1984. – 264 с.
- Котов К. И., Шершевер М. А. Средства измерения, контроля и автоматизации технологических процессов. – М.: Металлургия, 1987. – 496 с.
- Михеев А. А. Методы и средства автоматизированного управления сушильной камерой (промышленность): дисс…. канд. техн. наук: 05. 13. 06/ Михеев Алексей Александрович. – Ируктск, 2015. – 133 с.
- Плетнев Г. П. Автоматическое регулирование и защита теплоэнергетических установок. – М.: Энергия, 1976
- Сергиенко А. Б. Цифровая обработка сигналов. – Спб.: Санкт – Петербург, 2002.
- Уэйкерли Д. Проектирование цифровых устройств / Д. Уэйкерли. – М.: Постмаркет, 2002. – Том 2. – 528 с.
- Михайлов Ю. Ю., Лабутин В. А., Быков И. Н., А.Ю. Михайлов. Моделирование процесса сушки в барабанной сушилке с учетом влияния продольного перемешивания сушильного агента. – Владимир: Владимирский государственный университет, 2010. – 3 с.
- Гартман Т. Н., Клушин Д. В. Основы компьютерного моделирования химико – технологических процессов: учеб. пособие для вузов. – М.: Академкнига, 2006.
- Питухин Е. А. Математическая модель управления качеством работы сушильной установки барабанного типа/// Труды Петрозаводского государственного университета. Вып. 6. 1997
- Кашьян Р. Л. Построение динамических стохастических моделей по экспериментальным данным. – М.: Наука, 1983.
- Vasiltsov I. Evolutionary technique to elementary coding of the internal states of the state machine / I. Vasiltsov // Proceedings of the 2002 NASA/DoD Conference on Evolvable Hardware. – 2002. – pp. 63–64.
- Шувалова Л.А. Структура программного комплекса синтеза и верификации моделей цифровых автоматов / Л.А. Шувалова, Д.Н. Моамар, Т.Ю. Уткина // Системи обробки інформації. – Харьков, 2010. – № 5. – С. 149–152.