- Цели и задачи работы
- Введение. Обоснование актуальности темы работы
- Предполагаемая научная новизна
- Предполагаемая практическая ценность
- Обзор исследований и разработок по теме
- Постановка задачи исследования
- Описание муравьиных алгоритмов
- Графовая модель
- Заключение
- Список литературы
Цели и задачи работы
Цель работы: Разработать компьютеризированную подсистему оперативного планирования работы автоматизированного технологического участка механообработки деталей для повышения эффективности его работы за счет составления оптимальных расписаний работы в условиях многокритериальности решения задачи.
Задачи работы:
- Охарактеризовать работу механического участка, исследовать параметры, определяющие эту работу и поставить задачу календарного планирования
- Провести анализ методов, моделей, алгоритмов и инструментальных средств для оптимизации оперативного планирования производства.
- Провести выбор и обоснование метода для оптимизации оперативного планирования производства.
- Разработать и программно реализовать алгоритм для оптимизации оперативного планирования производства.
Введение. Обоснование актуальности темы работы
В наше время наблюдается бурное развитие информационных компьютерных технологий и их внедрение во все сферы деятельности человека. Более остро необходимость комплексного внедрения информационных систем управления стоит перед предприятиями машиностроения. Применение современных информационных технологий в области оперативного учета производства поможет упорядочить документооборот, учесть и минимизировать потери, повысить производительность работы, снизить затраты на работу и др [1].
Для машиностроительных предприятий с различной производственной структурой одной из важнейших задач внутрицехового планирования является установление календарного плана загрузки оборудования. Расчеты календарных графиков выполняются во всех системах оперативно-производственного планирования, однако из-за сложности задачи результаты этих расчетов далеко не в полной мере удовлетворяют условиям рациональной организации производствами, как правило, в силу непредвиденных обстоятельств календарные графики нарушаются в первые же часы работы цеха.
На реальный производственный процесс оказывают воздействие большое количество внешних причин:
- выход из строя технологического оборудования;
- введение в производство новой детали;
- сбои в транспортно-складской системе.
В связи с этим, для обеспечения сроков выполнения заказов, производственная программа на отдельно взятом участке может изменяться. Это вызывает необходимость оперативной корректировки расписания. Поэтому трудность построения календарного плана заключается не только в предварительном расчете оптимального (наилучшего) варианта использования имеющегося оборудования для своевременного выполнения производственных заданий, но также и в необходимости эффективного преобразования поступающей информации о ходе производства с целью внесения соответствующих коррективов в первоначальный вариант плана. Такие задачи из-за большого объема вычислительных работ можно решить только с помощью ЭВМ [2].
Компьютеризированные системы позволяют существенным образом повысить оперативность производственного управления на предприятии. Внедрение таких систем на предприятии помогли бы контролировать движение и производство деталей и узлов, потому что задача оперативно-календарного планирования в значительной мере влияют на результаты работы предприятия в целом [1].
Предполагаемая научная новизна
Для обеспечения высокой эффективности работы производственных участков и максимального использования возможности оборудования, необходимо создавать близкие к оптимальному расписанию работы станков (ГПМ). Основным инструментом для этого являются моделирование и оптимальное управление.
Большинство разработанных к настоящему времени методик оперативно-календарного планирования основано на упрощенных моделях, которые снижают их практическую значимость, или эти методики применимы лишь для определенных специфических условий. Существует необходимость в разработке методики оперативного календарного планирования работы предприятий дискретного производства, которая позволила бы проводить оптимизацию расписания выпуска продукции с учетом существующих ограничений, формировать сменно-суточные задачи подразделам цеха и при этом обеспечивала бы получение оптимальных или близких к оптимальным решениям.
Неизученным остается движение партий деталей непосредственно в производственной среде, на производственном участке согласно технологическому маршруту. Создание программных комплексов для моделирования и управления работой производственных участков, составление близких к оптимальным расписаниям работы оборудования, есть актуальной научно-технической задачей [3].
Эта задача уже решалась с помощью муравьиных алгоритмов, где обращение «муравьев» можно было расценивать как движение партий деталей по производственному участку. А научная новизна моей работы состоит в том, что за «муравья» я буду брать оборудование (ГПМ).
Предполагаемая практическая ценность
Это позволит на практике быстро и эффективно решать задачи оперативно-производственного планирования. Разработанный программный модуль позволит сократить затрату материальных и временных ресурсов на выполнение планирования производственного процесса, повысит качество обработки информации и качество результата обработки, исключив ошибки, связанные с человеческим фактором.
Обзор исследований и разработок по теме
- глобальный (мировой)
Создан ряд программных продуктов, которые можно отнести к ERP системам, например, LEKIN и TACTIC. Из зарубежных авторов можно выделить: Rong Zhou, Jun Zhang, Alan S. Manne и др.
- национальный (кто и что делает по данной теме в стране за пределами ДонНТУ)
В целом по Украине было найдено множество работ по смежным областям с разрабатываемой подсистемой. Можно выделить также существующие разработки по данной теме: система технологической подготовки, оперативного планирования и диспетчерского контроля «ФОБОС», (MRP-II) ERP-системы «Компас», СПРУТ-ОКП, Zenith SPPS и др.
- локальный (по материалам преподавателей, аспирантов и магистрантов ДонНТУ)
По результатам поиска среди материалов портала магистров ДонНТУ были найдены работы Андреенковой Е. А., Башева В.Г., Сухорукова Д. В., в которых рассматривались проблемы оперативно-календарного планирования в различных отраслях. Из научных работ преподавателей нашего университета по данной теме были найдены работы Секирина А. И.
Постановка задачи исследования
Составление календарного плана загрузки оборудования в общем случае заключается в следующем: имеются детали, которые необходимо обработать на станках. Требуется определить такую последовательность поступления деталей для обработки на каждый станок, чтобы время простоев оборудования (общее время обработки деталей) было минимальным.
Задачей управления является обеспечение выпуска продукции согласно производственной программе (Nпл) по количеству и в установленные сроки при эффективном использовании ресурсов (Rl) в условиях действия возмущений (Vk). Обеспечение высокой эффективности использования ресурсов (Rl) и функционирования цеха в целом достигается за счет оптимизации расписаний работы оборудования.
Процесс изготовления деталей Di (i=l, ..., п) разбивают на технологические операции Оij (i=1,..., п; j=l,..., m). Детали одного типа объединяются в транспортные партии и в разрезе расписаний рассматриваются как технологическая единица. Каждая операция может быть выражена:
Оij = <Нij ,Тij>, (1)
где Нij - номер группы технологического оборудования; Тij - продолжительность выполнения операции.
Технологический маршрут представляет собой последовательность выполняемых операций, которые проходит i-я деталь в процессе обработки:
Мi = < Оi1, Оi2,..., Оim > (2)
Операция Оij должна выполняться без перерыва с самого начала. Если обозначить через tij - время начала выполнения операции Оij, а через tij' -момент окончания обработки, то должно выполнятся равенство:
tij' = tij + Tij (3)
Очевидно, что время начала обработки зависит от времени выполнения предыдущих операций и всегда выполняется неравенство: tij ≤ tij+1. Тогда совокупность {tij} (i=1,..., n; j=l,..., m), удовлетворяющих всем технологическим и временным ограничениям, является расписанием работы.
Ограничения
Задача оптимизации расписания заключается в том, чтобы определить такую последовательность запуска деталей в производство и размеры партий запуска, при которых критерий оценки качества расписания стремился к экстремуму при выполнении следующих ограничений:
-
ограничения по объемам изготовления:
-
ограничения по срокам изготовления:
-
ограничения по фонду времени работы технологического оборудования:
Nпл=Nф, (4)
где Nф - фактическое изготовленное количество деталей i-го типа (i=l,...,K);
Nпл - заданное в производственной программе количество деталей i-гo типа;
К - номенклатура изготавливаемых деталей.
Тпл ≥ Тф , (5)
где Тф - фактический срок изготовления i-ой детали (i=l,...,K);
Тпл - директивный срок изготовления i-ой детали.
, (6)
где Тij - длительность выполнения технологической операции;
Ri - ресурс i-ой группы оборудования.
Критерии оценки эффективности
Запишем основные критерии, по которым может быть произведена оценка эффективности полученного расписания:
-
Минимизация длительности цикла изготовления деталей (минимизация простоя оборудования)
-
Максимизация среднего коэффициента загрузки технологического оборудования (максимизация загрузки оборудования)
-
Минимизация времени пролеживания деталей
Tопт = Т → min, (7)
где Т - общее время производственного цикла.
, (8)
где Тij - длительность цикла технологической операции i-ой партии деталей;
αij - длительность простоя перед началом выполнения j-ой технологической операции над i-ой партией деталей;
Копт з = 1/m∑Kз → max, (9)
где m - количество оборудования;
Kз - коэффициент загрузки i-го оборудования.
Коэффициент загрузки i-гo оборудования определяется отношением времени производительной работы к общему времени по формуле:
, (10)
, (11)
, (12)
где αi - затраты на хранение i-й партии деталей.
Также возможны и другие критерии для выбора оптимального календарного плана загрузки станков. Можно использовать минимизацию: общих расходов на обработку деталей; максимальной задержки выпуска деталей; общего времени обработки деталей; стоимости незавершенного производства; суммарных отклонений от плановых сроков изготовления деталей; числа или продолжительности переналадок; размера партии деталей; загрузки уникальных станков.
Перечисленные критерии в большинстве случаев противоречивы, и поэтому от правильного выбора критерия во многом зависит качество календарного плана.
При этом совокупность времени {tij}опт, соответствующая экстремуму критерия F(G) при выполнении указанных ограничений будет являться оптимальным расписанием (G') работы [2].
Описание муравьиных алгоритмов
Муравьиный алгоритм для оптимизации задач, подобный оперативному планированию, не требует наличия модели объекта оптимизации [4].
Основная идея простого муравьиного алгоритма есть моделирования обращения муравьев, коллективной адаптации. Колония представляет собой систему с очень простыми правилами автономного обращения особей. Однако, несмотря на примитивность обращения каждого отдельного муравья, обращение всей колонии оказывается довольно умным. Таким образом, основой обращения муравьиной колонии служит низкоуровневое взаимодействие, благодаря которому, в целом, колония представляет собой умную многоагентную систему. Взаимодействие определяется через химическое вещество - феромон, что откладывается муравьями на пройденном пути. При выборе направления движения, муравей исходит не только из желания пройти кратчайший путь, но и по опыту других муравьев, информацию о котором получаем через уровень феромонов (на ребрах). Со временем происходит процесс испарения феромонов, что есть негативной обратной связью [5].
Графовая модель
Задача планирования относится к оптимизации дискретных процессов. В последнее время, для поиска оптимального решения, широко используются муравьиные алгоритмы, в основе которых всегда лежит графовая модель объекта или задачи. Поэтому рассмотрим построение графовой модели функционирования работы автоматизированного технологического участка (АТУ).
Элементами графа является узел (вершина) и ребра, соединяющие отдельные вершины графа (см. рис.1). Исходная вершина графа определяет начало выполнения плана (стартовая точка) и в эту вершину предполагается помещать столько муравьев, каково количество оборудования на производственном участке. Остальные вершины графа разбиты на уровни, каждый из которых соответствует отдельной технологической операции. Количество вершин в первом и во втором уровне равно количеству типов, запланированных к выпуску деталей. На остальных уровнях вершин может быть меньше, если технологическая карта выпуска деталей содержит только две операции.
Таким образом, узел – это условное обозначение выполняемой операции на данном этапе определенным ГПМ, а ребро характеризуется вероятностью перехода муравья (ГПМ) с одной операции на другую.
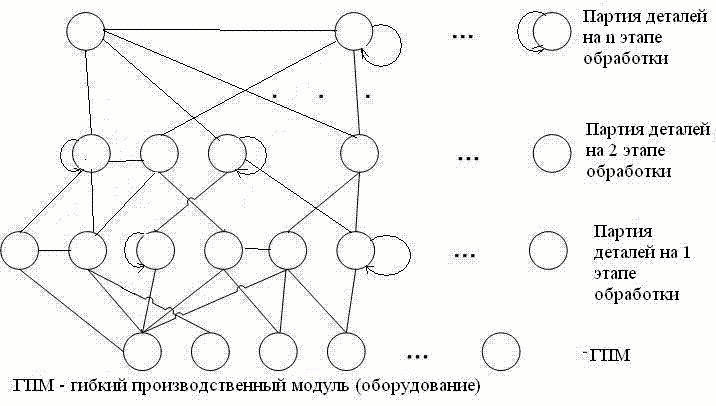
Рисунок 1 – Граф для задания оперативного планирования работы производственного участка.
Вероятности перехода муравьев из стартовой точки в узлы первого уровня могут быть рассчитаны с использованием временных параметров технологических карт изготовления деталей и с учетом сроков выполнения заказа.
, (13)
где Ti – время выполнения операции;
Tiср – срок выполнения заказа.
Вероятности дальнейших переходов необходимо рассчитывать с учетом уже выполненной работы и оставшегося времени до срока выпуска партии деталей.
Если переходы от стартовой точки возможны только к вершинам первого уровня, то дальнейшие переходы предусматривают соединение вершин одного уровня и наличие петель, что означает продолжение выполнения данной операции со следующей партией деталей [6].
Заключение
Автоматизация обрабатывающего и вспомогательного оборудования с использованием современных компьютерных технологий, в условиях развития машиностроения, есть одним из основных направлений технического прогресса в машиностроении. Оборудование должно обеспечивать выполнение заданной номенклатуры технологических операций на участке в установленный срок и иметь способность оперативно реагировать на смену состояния оборудования, изменение производственных заказов.
Для обеспечения высокой эффективности работы производственных участков и максимального использования возможности оборудования, необходимо создавать близкие к оптимальному расписанию работы оборудования.
В ходе выполнения данной работы были проанализированы существующие методы, модели и подходы для решения задач оперативно-календарного планирования. Был разработан алгоритм и графовая модель процессов работы и повышения эффективности функционирования автоматизированного технологического участка механообработки деталей, на основе субоптимального расписания работы оборудования.
В дальнейшем будет разработан и программно реализован алгоритм для оптимизации работы производственного участка.
Список литературы
1. Первозванский А.А. Математические модели в управлении производством // Главная редакция физико-математической литературы издательства «Наука», М. – 1975, 616 с.
2. Сытник В.Ф. АСУП и оптимальное планирование // Издательское объединение «Вища школа», Киев. – 1977, 312 с.
3. Секирин А.И. Программный комплекс для моделирования, анализа и оптимизации работы автоматизированных технологических комплексов механообработки // Донецкий национальный технический университет, кафедра автоматизированных систем управления.
4. Ходашинский И.А., Горбунов И.В., Дудин П.А. «Алгоритмы муравьиной и пчелиной колонии» // М. - 2007.
5. Штовба С. Статья из журнала Exponenta Pro: Муравьиные алгоритмы [электронный ресурс]. – Режим доступа: http://rain.ifmo.ru/.../ant-algo-2006/article.pdf
6. Габалис Е.Ю., Савкова Е.О., Жукова Т.П. Графовая модель планирования работы автоматизированного технологического участка механообработки деталей // Збірка матеріалів IІ всеукраїнської науково-технічної конференції студентів, аспірантів та молодих вчених – 11-13 квітня 2011 р., Донецьк, ДонНТУ – 2011, с. 49-53.
7. Лаздынь С.В., Секирин А.И. Оптимизация расписаний работы автоматизированных технологических комплексов механообработки с использованием генетических алгоритмов // Международный сборник научных трудов “Прогрессивные технологии и системы машиностроения”, выпуск 25. –Донецк: ДонНТУ.-2003, c. 198-203.
8. Исполнительный производственные системы. Официальный сайт компании Fobos-mes [электронный ресурс]. – Режим доступа: http://www.fobos-mes.ru/russian-MES/index.php
9. Независимый ERP-портал [электронный ресурс]. – Режим доступа: http://www.erp-online.ru/.../kompas/
10. Официальный сайт LEKIN [электронный ресурс]. – Режим доступа: http://www.stern.nyu.edu/.../lekin/index.htm
11. Официальный сайт TACTIC [электронный ресурс]. – Режим доступа: http://www.waterloo-software.com/
ВАЖНОЕ ЗАМЕЧАНИЕ.
При написании данного автореферата магистерская работа еще не завершена. Окончательное завершение: декабрь 2012 года. Полный текст работы и материалы по теме могут быть получены у автора или его руководителя после указанной даты.