- Мета й завдання роботи
- Вступ. Обгрунтування актуальності теми роботи
- Запланована наукова новизна
- Запланована практична цінність
- Огляд досліджень і розробок по темі:
- Постановка завдання дослідження
- Опис мурашиних алгоритмів
- Графова модель
- Висновок
- Список літератури
Мета й завдання роботи
Мета роботи: Розробити комп'ютеризовану підсистему оперативного планування роботи автоматизованої технологічної ділянки механообробки деталей для підвищення ефективності його роботи за рахунок складання оптимальних розкладів роботи в умовах багатокрітеріальності вирішення завдання.
Завдання роботи:
- Охарактеризувати роботу механічної ділянки, дослідити параметри, що визначають цю роботу й поставити завдання календарного планування.
- Провести аналіз методів, моделей, алгоритмів і інструментальних засобів для оптимізації оперативного планування виробництва.
- Провести вибір і обґрунтування методу для оптимізації оперативного планування виробництва.
- Розробити й програмно реалізувати алгоритм для оптимізації оперативного планування виробництва.
Вступ. Обгрунтування актуальності теми роботи
У наш час спостерігається бурхливий розвиток інформаційних комп'ютерних технологій і їх впровадження в усі сфери діяльності людину. Більш гостро необхідність комплексного впровадження інформаційних систем керування стоїть перед підприємствами машинобудування. Застосування сучасних інформаційних технологій в галузі оперативного обліку виробництва допоможе впорядкувати документообіг, урахувати й мінімізувати втрати, підвищити продуктивність роботи, знизити витрати на роботу та ін [1].
Для машинобудівних підприємств із різною виробничою структурою одним із найважливіших завдань внутрішньоцехового планування є встановлення календарного плану завантаження встаткування. Розрахунки календарних графіків виконуються в усіх системах оперативно-виробничого планування, однак через складність завдання результати цих розрахунків далеко не повною мірою задовольняють умовам раціональної організації виробництва, як правило, у силу непередбачених обставин календарні графіки порушуються в перші ж години роботи цеху.
На реальний виробничий процес впливає велика кількість зовнішніх причин:
- вихід з ладу технологічного встаткування;
- уведення до виробництва нової деталі;
- збої в транспортно-складській системі.
У зв'язку із цим, для забезпечення строків виконання замовлень, виробнича програма на окремо взятій ділянці може змінюватися. Це викликає необхідність оперативного коректування розкладу. Тому труднощі побудови календарного плану полягають не тільки в попередніх розрахунках оптимального (найкращого) варіанта використання наявного встаткування для своєчасного виконання виробничих завдань, але також і в необхідності ефективного перетворення інформації про хід виробництва, що надходить з метою внесення відповідних корективів у первісний варіант плану. Такі завдання через великий обсяг обчислювальних робіт можна вирішити тільки за допомогою ЕОМ [2].
Комп'ютеризовані системи дозволяють істотно підвищити оперативність виробничого керування на підприємстві. Впровадження таких систем на підприємстві допомогли б контролювати рух і виробництво деталей і вузлів, тому що завдання оперативно-календарного планування значною мірою впливають на результати роботи підприємства в цілому [1].
Запланована наукова новизна
Для забезпечення високої ефективності роботи виробничих ділянок і максимального використання можливості встаткування, необхідно створювати близькі до оптимального розклади роботи встаткування. Основним інструментом для цього є моделювання й оптимальне керування.
Більшість розроблених до теперішнього часу методик оперативно-календарного планування засновані на спрощених моделях, які знижують їхню практичну значимість, або ці методики можуть застосовуватися лише для певних специфічних умов. Існує необхідність у розробці методики оперативного календарного планування роботи підприємств дискретного виробництва, яка дозволила б проводити оптимізацію розкладу випуску продукції по декільком критеріям якості з урахуванням існуючих обмежень, формувати змінно-добові завдання підрозділам цеху й при цьому забезпечувала б отримання оптимальних або близьких до оптимальних розв'язків.
Невивченим залишається рух партій деталей безпосередньо у виробничім середовищі, на виробничій ділянці згідно з технологічним маршрутом. Створення програмних комплексів для моделювання й керування роботою виробничих ділянок, складання близьких до оптимальних розкладів роботи встаткування, є актуальним науково-технічним завданням [3].
Це завдання вже вирішувалося за допомогою мурашиних алгоритмів, де обіг «мурах» можна було розцінювати як рух партій деталей по виробничій ділянці. А наукова новизна моєї роботи полягає в тому, що за «мураху» я буду брати встаткування (ГПМ).
Запланована практична цінність
Це дозволить на практиці швидко й ефективно вирішувати завдання оперативно-виробничого планування. Розроблений програмний модуль дозволить скоротити витрату матеріальних і тимчасових ресурсів на виконання планування виробничого процесу, підвищить якість обробки інформації і якість результату обробки, виключивши помилки, пов'язані з людським фактором.
Огляд досліджень і розробок по темі:
- глобальний (світовий)
Створений ряд програмних продуктів, які можна віднести до ERP систем, наприклад, LEKIN та TACTIC. Із закордонних авторів можна зазначити: Rong Zhou, Jun Zhang, Alan S. Manne та ін.
- національний (хто й що робить по даній темі в країні за межами ДонНТУ)
У цілому по Україні було знайдено безліч робіт із суміжних областей з розроблювальною підсистемою. Можна зазначити такі існуючі розробки по даній темі як: система технологічної підготовки, оперативного планування й диспетчерського контролю «ФОБОС», (MRP-II) ERP-система «Компас», СПРУТ-ОКП, Zenith SPPS та ін.
- локальний (за матеріалами викладачів, аспірантів і магістрантів ДонНТУ)
За результатами пошуку серед матеріалів порталу магістрів ДонНТУ були знайдені роботи Андрєєнкової О.О., Хаустової Д. О., Сухорукова Д. В., у яких розглядалися проблеми оперативно-календарного планування в різних галузях. З наукових праць викладачів нашого університету по даній темі були знайдені роботи Секіріна О. І.
Постановка завдання дослідження
Складання календарного плану завантаження встаткування в загальному випадку полягає в наступному: є деталі, які необхідно обробити на верстатах. Потрібно визначити таку послідовність вступу деталей для обробки на кожний верстат, щоб час простоїв устаткування (загальний час обробки деталей) був мінімальним.
Завданням керування є забезпечення випуску продукції згідно з виробничою програмою (Nпл) по кількості й у встановлений термін при ефективному використанні ресурсів (Rl) в умовах дії обурювань (Vk). Забезпечення високої ефективності використання ресурсів (Rl) і функціонування цеху в цілому досягається за рахунок оптимізації розкладів роботи встаткування.
Процес виготовлення деталей Di (i=1, ..., п) розбивають на технологічні операції Оij (i=1,..., п; j=1,..., m). Деталі одного типу поєднуються в транспортні партії й у розрізі розкладів розглядаються як технологічна одиниця. Кожна операція може бути виражена:
Оij = <Нij,Тij>, (1)
де Нij - номер групи технологічного встаткування; Тij - тривалість виконання операції.
Технологічний маршрут – це послідовність виконуваних операцій, які проходить i-а деталь у процесі обробки:
Мi = < Оi1, Оi2,..., Оim > (2)
Операція Оij повинна виконуватися без перерви із самого початку. Якщо позначити через tij - час початку виконання операції Оij, а через tij' -момент закінчення обробки, то повинна виконуватися рівність:
tij' = tij + Tij (3)
Очевидно, що час початку обробки залежить від часу виконання попередніх операцій і завжди виконується нерівність: tij ≤ tij+1. Тоді сукупність {tij} (i=1,...,n; j=1,...,m), що задовольняє усім технологічним і тимчасовим обмеженням, є розкладом роботи.
Обмеження
Завдання оптимізації розкладу полягає в тому, щоб визначити таку послідовність запуску деталей у виробництво й розміри партій запуску, при яких критерій оцінки якості розкладу прагнув до экстремуму при виконанні наступних обмежень:
-
обмеження за обсягами виробництва:
-
обмеження за строками виготовлення:
-
обмеження за фондом часу роботи технологічного встаткування:
Nпл=Nф, (4)
де Nф - фактична виготовлена кількість деталей i-го типу (i=l,...,K);
Nпл - задана у виробничій програмі кількість деталей i-гo типу.
К - номенклатура деталей, що виготовляються.
Тпл ≥ Тф, (5)
де Тф - фактичний строк виготовлення i-ої деталі (i=l,...,K);
Тпл - директивний строк виготовлення i-ої деталі.
, (6)
де Тij - тривалість виконання технологічної операції;
Ri - ресурс i-ої групи встаткування.
Критерії оцінки ефективності
Запишемо основні критерії, завдяки яких може бути зроблена оцінка ефективності отриманого розкладу:
-
Мінімізація тривалості циклу виготовлення деталей (мінімізація простою встаткування)
-
Максимізація середнього коефіцієнта завантаження технологічного встаткування (максимізація завантаження встаткування)
-
Мінімізація часу пролежування деталей
Tопт = Т → min , (7)
де Т - загальний час виробничого циклу.
, (8)
де Тij - тривалість циклу технологічної операції i-ої партії деталей;
αij - тривалість простою перед початком виконання j-ої технологічної операції над i-ою партією деталей;
Копт з = 1/m∑Kз → max, (9)
де m - кількість устаткування;
Kз - коефіцієнт завантаження i-го встаткування.
Коефіцієнт завантаження i-гo устаткування визначається відношенням часу продуктивної роботи до загального часу по формулі:
, (10)
, (11)
, (12)
де αi - витрати на зберігання i-ої партії деталей.
Також можливі й інші критерії для вибору оптимального календарного плану завантаження верстатів. Можна використовувати мінімізацію: загальних витрат на обробку деталей; максимальної затримки випуску деталей; загального часу обробки деталей; вартості незавершеного виробництва; сумарних відхилень від планових строків виготовлення деталей; числа або тривалості переналагоджень; розміру партії деталей; завантаження унікальних верстатів.
Перераховані критерії в більшості випадків суперечливі, і тому від правильного вибору критерію багато в чому залежить якість календарного плану.
При цьому сукупність часу {tij}опт, що відповідає екстремум критерію F(G) при виконанні зазначених обмежень буде оптимальним розкладом (G') роботи [2].
Опис мурашиних алгоритмів
Мурашиний алгоритм для оптимізації завдань, подібний до оперативного планування, не вимагає наявності моделі об'єкта оптимізації [4].
Основна ідея простого мурашиного алгоритму є моделювання обігу мурах, колективної адаптації. Колонія являє собою систему з дуже простими правилами автономного обігу особин. Однак, незважаючи на примітивність обігу кожної окремої мураху, обіг усієї колонії виявляється досить розумним. Таким чином, основою обігу мурашиної колонії є низькорівнева взаємодія, завдяки якому, у цілому, колонія являє собою розумну багатоагентну систему. Взаємодія визначається через хімічну речовину - феромон, що відкладається мурахами на пройденому шляху. Під час вибору напрямку руху, мураха виходить не тільки з бажання пройти найкоротший шлях, але й по досвіду інших мурах, інформацію про який одержуємо через рівень феромонів (на ребрах). Згодом відбувається процес випару феромонів, що є негативним зворотним зв'язком [5].
Графова модель
Завдання планування ставиться до оптимізації дискретних процесів. Останнім часом, для пошуку оптимального вирішення, широко використовуються мурашині алгоритми, в основі яких завжди лежить графова модель об'єкта або завдання. Тому розглянемо побудову графової моделі функціонування роботи автоматизованої технологічної ділянки (АТД).
Елементами графа є вузол (вершина) і ребра, що з'єднують окремі вершини графа (див. мал.1). Вихідна вершина графа визначає початок виконання плану (старт) і в цю вершину передбачається поміщати стільки мурах, скільки устаткування на виробничій ділянці. Інші вершини графа розбиті на рівні, кожний з яких відповідає окремій технологічній операції. Кількість вершин у першому й у другому рівні дорівнює кількості типів, запланованих до випуску деталей. На інших рівнях вершин може бути менше, якщо технологічна карта випуску деталей містить тільки дві операції.
Таким чином, вузол – це умовна позначка виконуваної операції на даному етапі певним ГВМ, а ребро характеризується ймовірністю переходу мурахи (ГВМ) з однієї операції на іншу.
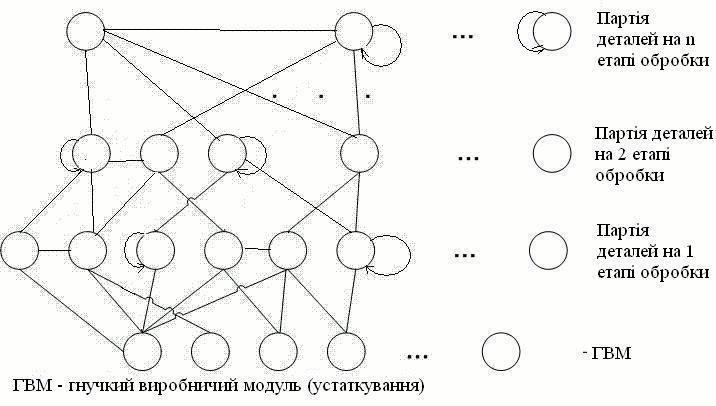
Малюнок 1 – Граф для завдання оперативного планування роботи виробничої ділянки.
Імовірності переходу мурах зі старту до вузлів першого рівня можуть бути розраховані з використанням тимчасових параметрів технологічних карт виготовлення деталей і з урахуванням строків виконання замовлення.
, (13)
де Ti – час виконання операції;
Tiср – строк виконання замовлення.
Імовірності подальших переходів необхідно розраховувати з обліком вже виконаної роботи й часу, що залишився до строку випуску партії деталей.
Якщо переходи від старту можливі тільки до вершин першого рівня, то подальші переходи передбачають з'єднання вершин одного рівня й наявність петель, що означає продовження виконання даної операції з наступною партією деталей [6].
Висновок
Автоматизація обробного й допоміжного устаткування з використанням сучасних комп'ютерних технологій, в умовах розвитку машинобудування, є одним з основних напрямків технічного прогресу в машинобудуванні. Устаткування повинне забезпечувати виконання заданої номенклатури технологічних операцій на ділянці у встановлений строк і мати здатність оперативно реагувати на зміну стану встаткування, зміну виробничих замовлень.
Для забезпечення високої ефективності роботи виробничих ділянок і максимального використання можливості встаткування, необхідно створювати близькі до оптимального розкладу роботи встаткування.
У ході виконання даної роботи були проаналізовані існуючі методи, моделі й підходи для вирішення завдань оперативно-календарного планування. Був розроблений алгоритм і графова модель процесів роботи й підвищення ефективності функціонування автоматизованої технологічної ділянки механообробки деталей, на основі субоптимального розкладу роботи встаткування.
У подальшому буде розроблений і програмно реалізований алгоритм для оптимізації роботи виробничої ділянки.
Список літератури
1. Первозванский А.А. Математические модели в управлении производством // Главная редакция физико-математической литературы издательства «Наука», М. – 1975, 616 с.
2. Сытник В.Ф. АСУП и оптимальное планирование // Издательское объединение «Вища школа», Киев. – 1977, 312 с.
3. Секирин А.И. Программный комплекс для моделирования, анализа и оптимизации работы автоматизированных технологических комплексов механообработки // Донецкий национальный технический университет, кафедра автоматизированных систем управления.
4. Ходашинский И.А., Горбунов И.В., Дудин П.А. «Алгоритмы муравьиной и пчелиной колонии» // М. - 2007.
5. Штовба С. Статья из журнала Exponenta Pro: Муравьиные алгоритмы [электронный ресурс]. – Режим доступа: http://rain.ifmo.ru/.../ant-algo-2006/article.pdf
6. Габалис Е.Ю., Савкова Е.О., Жукова Т.П. Графовая модель планирования работы автоматизированного технологического участка механообработки деталей // Збірка матеріалів IІ всеукраїнської науково-технічної конференції студентів, аспірантів та молодих вчених – 11-13 квітня 2011 р., Донецьк, ДонНТУ – 2011, с. 49-53.
7. Лаздынь С.В., Секирин А.И. Оптимизация расписаний работы автоматизированных технологических комплексов механообработки с использованием генетических алгоритмов // Международный сборник научных трудов “Прогрессивные технологии и системы машиностроения”, выпуск 25. –Донецк: ДонНТУ.-2003, c. 198-203.
8. Исполнительный производственные системы. Официальный сайт компании Fobos-mes [электронный ресурс]. – Режим доступа: http://www.fobos-mes.ru/russian-MES/index.php
9. Независимый ERP-портал [электронный ресурс]. – Режим доступа: http://www.erp-online.ru/.../kompas/
10. Официальный сайт LEKIN [электронный ресурс]. – Режим доступа: http://www.stern.nyu.edu/.../lekin/index.htm
11. Официальный сайт TACTIC [электронный ресурс]. – Режим доступа: http://www.waterloo-software.com/
ВАЖЛИВЕ ЗАУВАЖЕННЯ.
Під час написання даного автореферату магістерська робота ще не завершена. Повне закінчення роботи: грудень 2012 року. Повний текст роботи та матеріали по темі можуть бути отримані в автора або його керівника після зазначеної дати.