Реферат по теме выпускной работы
Содержание
- Введение
- 1. Актуальность темы
- 2. Цель и задачи исследования, планируемые результаты
- 3.Экологическая безопастность при производстве сортового проката
- 3.1 Влияние прокатного производства на атмосферный воздух при производстве сортового и листового проката.
- 3.1.1 Технологические выбросы
- 3.1.2 Неорганизованные выбросы
- 3.1.3 Утилизация окалины
- 4. Иccледования и разработка системы пылеподавления сортового стана 250 ПрАО
ДМЗ
- 4.1Форсунки для подавления неорганизованного пыли
- 4.2Утилизация замасленной окалины
- Выводы
- Список источников
Введение
Прокатное производство - одно из крупнейших видов металлургического производства. В прокатных цехах обрабатывают примерно 3/4 всего выплавляемого металла. Технологический процесс получения готовых прокатных изделий является завершающей стадией металлургического производства. Разнообразие сортамента прокатных изделий и сложность условий пластической и термической обработки, а также обработка проката определяют применение в прокатных цехах мощного механического, электрического и термического оборудования. Эксплуатация такого оборудования обусловливает необходимость создания безопасных, безвредных и удобных условий работы для персонала прокатных цехов.
1. Актуальность темы
Основной проблемой прокатных цехов является неорганизованные выбросы пыли на участке прокатных станов. Эти выбросы создают большое запыленности воздуха в цехах, что крайне негативно влияет на здоровье обслуживающего персонала, а также большое количество пыли выбрасывается через аэрационные фонари в окружающую среду.
Неорганизованные выбросы улавливать технически невозможно, экономически невыгодно. Поэтому в данной работе акцентировано внимание именно на эту проблему. Проблема неорганизованных выбросов актуальна вдвойне: во-первых, с решением этой проблемы улучшаются условия труда рабочих и во-вторых, улучшится экологическая обстановка.
2. Цель и задачи исследования
Цель работы-разработать мероприятия по повышению экологической и технической безопасности производства сортового проката и оценить их влияние на окружающую среду.
Объект исследования: Сортовое производство проктного цеха ПрАОДМЗ
Основные задачи исследования:
- Сбор информационных и экспериментальных данных по вопросам, касающихся подавления выделения пыли при прокатке , а также подготовки и утилизации замасленной окалины прокатного производства.
- Анализ данных и разработка наиболее рациональной схемы утилизации замасленной окалины.
- Проведение промышленных опытов, позволяющих определить состав окалины, ее свойства, температуру конденсации масла и т.д.
- Разроботка математической модели системы пылеподавления на прокатных станах .
- Разработка системы пылеподавления для стана 250 ПhАО
ДМЗ
- Разработка информационно-аналитической системы для анализа и оценки экологической и экономической эффективности от внедрения данной технологии.
3.Экологическая безопастность при производстве сортового проката
3.1 Влияние прокатного производства на атмосферный воздух при производстве сортового и листового проката.
В прокатном производстве, как и в других производствах, имеются организованные технологические и неорганизованные выбросы. Производство сортового и листового проката сопровождается незначительными выбросами загрязняющих веществ в атмосферу. В данном производстве, как и в других производствах, являются организованные технологические и неорганизованные выбросы. Основной источник технологических выбросов - нагревательные печи. Источником неорганизованных выбросов: нагревательные печи при недостаточной тяге, рабочие клети, ножницы для резки металла, механическая зачистка заготовок [1].
3.1.1 Технологические выбросы
Нагревательные устройства отапливаются природным, коксовым, доменным газами и их смесью. Количество продуктов сгорания в нагревательных печах и колодцах зависит от тепловой работы этих агрегатов и составляет 700 – 1000 м3/т нагреваемого металла . Оксиды серы в продуктах горения образуются при использовании коксового и доменного газов. В случае использования в прокатном производстве нетрадиционных искусственных топлив - конвертерных газов, очищенных ферросплавных, концентрация сернистых газов в продуктах их горения сохранится примерно на уровне 700 - 1000 мг/м3. При сжигании природного газа в нагревательных устройствах воздух практически не загрязняется. При сжигании серосодержащего топлива (мазута, коксового и коксосодержащих газов) в атмосферу поступает сернистый ангидрит, количество которого зависит от содержания серы в топливе и его расходе.
3.1.2 Неорганизованные выбросы
При горячей прокатке металла пыль образуется в результате измельчения окалины валками и испарения вследствие мгновенного увеличения давления и повышения температуры в очаге деформации при прокатке. Количество пыли, выделяемой на 1т проката, составляет при прокатке слябов и блюмов до 80 г/т, а при прокате листа до 100 г/т. Часть пыли (~ 20%) мелкодисперсная (размер частиц <10 мкм) [1].
На блюмингах и сортовых станах наиболее интенсивное пылевыделения происходит в первых проходах. Количество пыли увеличивается с повышением скорости прокатки и зависит от марки стали и толщины прокатываемого раската. Отдельные измерения содержания пыли в чистовой клети листопрокатного состояния показали загрязнение воздуха в пределах 400 - 100 мг / м ³ [1]. При недостаточной тяге в дымоходах нагревательных печей в неорганизованных выбросах , содержится окись углерода в количестве до 150 г/т проката. Удельные выбросы пыли в прокатных цехах блюминга и слябинга составляют 50 г / т, через вытяжные фонари выбрасывается 15% этого количества, т.е. примерно 11 г / т проката, при этом на долю отделения нагревательных колодцев приходится 7 г/т, а на отделение подготовки - 4 г/т.
В процессе прокатки металла в валках и при его резке на ножницах, а также при транспортировке по рольгангу окалина отделяется по поверхности заготовок и частично измельчается. Мелкие фракции в виде пыли захватываются выходные тепловыми потоками. Часть этой пыли удаляется из цеха через вытяжные проемы (около 10 - 20%), а другая (около 30 - 90%) осаждается в помещениях цеха на строительных конструкциях здания и оборудовании. Расчеты и исследования показали, что общее удельное количество пыли, которая выделяется в отделении прокатки, составляет 30г /т прокатываемого металла . Неорганизованные выбросы листопрокатных и крупносортных цехов содержат окись углерода и пыль. Так, удельное количество пыли, выделяемой по цеху слябинга в целом составляет 50 + 30= 80 г/т.
Общее удельное количество окиси углерода, выделяемого из печного отделения при несовершенной конструкции горелочного устройств и недостаточной тяге (выбивание газов из рабочего пространства), составляет до 200 г / т проката. Удельное количество пыли, выделяющейся через аэрационные фонари, составляет в среднем до 16 г / т проката и до 0,27 г / м2 площади прокатываемого листа. Общая удельное количество пыли, выделяющейся при прокатке металла, составляет 100 г/т.[1]. Все неорганизованные выбросы из здания удаляются через аэрационный фонарь.
3.1.3 Утилизация окалины
В прокатных цехах металлургических предприятий основными отходами являются: окалина первичных отстойников, окалина вторичных отстойников, отходы порезки металла, маслоотдходы.
Для организации ресурсосберегающих технологий прокатного производства указанные отходы должны быть соответствующим образом собраны, подготовлены и отправлены потребителям. Наличие перечисленных отходов на конкретном предприятии зависит от состава прокатных цехов, а также от вида выпускаемой продукции, и ее обработки. Не все отходы находят полное применение. Если окалина первичных отстойников используется практически полностью, то использование вторичного окалины составляет ¾.
4. Иccледования и разработка системы пылеподавления сортового стана 250 ПрАО ДМЗ
При прокатке количество пыли попадает в атмосферу, составляет не менее 200 грамм на тонну готового проката, причем до 20% от этого количества составляет мелкодисперсная окалина, наиболее опасная для человека. При создании технологий нового качественного уровня, обеспечивающих повышение механических свойств проката за счет совмещения в едином технологическом потоке стана операций пластической деформации и термического упрочнения, была также поставлена задача существенного снижения вредных выбросов в атмосферу цеха за счет подавления пылеобразования на выходе из ячейки деформации компактной струей отработанного охладителя.
В работе предусмотрено две схемы пылеподавления.
- На клетях, где нет устройства ускоренного охлаждения, предусмотрено установить форсунки для подавления неорганизованного пыли, образующейся при выходе металла из калибра.
- На рабочих клетях, на которых устраивается устройство ускоренного охлаждения, предусмотрено совмещения процесса охлаждения с пылеподавлением.
4.1Форсунки для подавления неорганизованного пыли
Пыль при работе прокатных станов образуется в результате раздавливания поверхностного слоя металла при проходе его через валки.
На блюмингах и слябингов пыль выделяется в течение всей прокатки. На сортовых станах с 11 - 12 проходами раската при прокатке выделением пыли сопровождается в большинстве случаев 5 - 6 проходов, а на непрерывных сортопрокатных станах пыль выделяется при прокатке в чистовых клетях, потому что у них металл проходит со значительно большей скоростью, чем в черновых. На листовых станах горячей прокатки пылевыделенниям сопровождает не только чистые, но и черновые клети. При этом на чистовых клетях пыли выделяется значительно больше, чем на черновых.
В небольших клетей пыль можно отсасывать через зонт, установленный на выходной стороне клети. Такая система имеет серьезные недостатки. В связи с тем, что отсасывается влажный пыль, воздуховоды в ряде случаев быстро забиваются, и поэтому требуют постоянного ухода. Кроме того, зонты мешают обслуживанию клетей. При обеспыливания крупных клетей приходится отсасывать и очищать большие объемы воздуха.
Учитывая перечисленные недостатки, проблему обеспыливания на ряде станов пытались решить применением гидравлического способа. Воду на клети подавали через трубу, выполненную в виде душевой сетки. Однако сила струи оказалась слабой. Для ее усиления было подведено сжатый воздух. Пыления прекратилось, однако возникли новые осложнения - шум от сжатого воздуха мешал работать. Обеспыливания с применением сжатого воздуха экономически невыгодно, и при дефиците сжатого воздуха, оно не может быть использовано на всех клетях. Кроме того, сжатый воздух создавало воздушный подпор под клетью и выгонял в цех пыль высохшую на стенах канала для смыва окалины [7].
Наиболее надежным средством обеспыливания на станах горячей прокатки является применение гидросмыва пыли в месте выхода проката из валков. Данный способ не имеет недостатков, которые присущи способам, описанным выше. При увеличении размеров сложной форме проката нужно подавать не одну, а несколько струй воды, причем таким образом, чтобы пыль смывался из всех плоскостей проката. Для реализации поставленной первой задачи разработан алгоритм проектирования форсунок. Предусмотрено форсунки струйного типа с конически росходящимся соплом, которые подают поток воды в зону выхода металла с рабочего калибра. С использованием разработанной программы спроектирована система пылеподавления для условий работы стана 250 ПрАО «ДМЗ». На рисунке 4.1 показана схема размещения основного оборудования и источников выброса пыли в состоянии 250.
С помощью водопроводных труб будет подаваться вода из оборотного цикла водоснабжения ПрАО ДМЗ
. Эта вода направляется далее в форсунки. Форсунки создают распыления воды, которое покрывает источника выброса пыли. Пыль будет падать и направляться вместе с водой в подстановой тоннель для дальнейшей очистки от окалины.
На рисунке 4.1 можно видеть, каким образом будет проходить гидросмыв на клети прокатного стана.
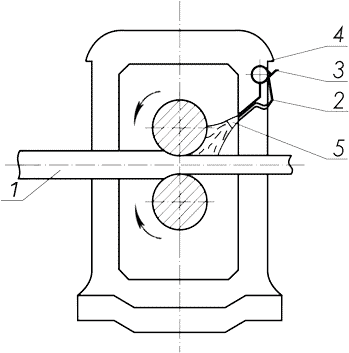
1 - прокат; 2 - гибкий шланг, 3 - водопроводная труба, 4 - сдвижной хомут, 5 - сопло.
Рисунок 4.1 - Схема системы гидросмыва на клети прокатного стана
По разработанной программе получены зависимости работы системы от различных конструктивных устройств. На рисунке 4.2 показана зависимость расхода воды на разные группы клетей стана 250 при разных диаметрах сопел. График позволяет выбрать соответствующий диаметр сопла и определить расход воды на разных клетях, что упрощает выбор технологических параметров работы системы пылеподавления.
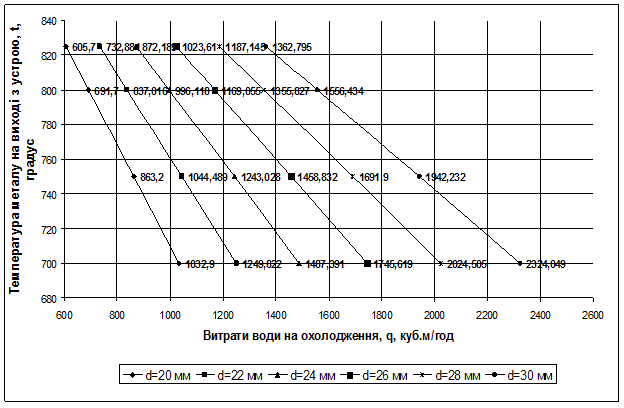
Рисунок 4.2 - Выбор необходимого расхода охладителя в зависимости от диаметра охлаждаемого профиля.
4.2Утилизация замасленной окалины
Как уже было сказано выше, идеей магистерской работы является разработка новой совершенной технологии по утилизации замасленной окалины, которая является отходом металлургического производства и его ценным вторичным сырьем одновременно. Содержание железа в ней составляет около 70 %.
Перейдем непосредственно к данной проблеме. Существует два пути утилизации окалины: возврат ее в металлургическое производство или использование ее в других производствах (например, в лакокрасочном).
Замасленную окалину трудно подготовить к утилизации из-за повышенного содержания в ней масел, а в прокатных цехах металлургических предприятий образуются большие количества замасленной окалины, которая находит ограниченное применение и сбрасывается в шламонакопители.
Проблема утилизации замасленной окалины в настоящее время решается в основном в одном направлении — обезмасливание ее с получением чистой, обезжиренной, легко утилизируемой окалины. Однако и химическое и термическое обезмасливание - дорогостоящие процессы, создающие дополнительные экологические осложнения. В настоящее время практически все образующиеся мелкодисперсные железосодержащие отходы утилизируют в составе аглошихты.
Выводы
-
На основании данных, полученных в ПрАО
ДМЗ
, определено, что суммарное количество отходов при производстве сортового и листового проката составляет: окалины - около 60 тыс. т/год, обрезь - более 115 тыс. т /год, лом черных металлов - более 9 тыс. т/год, в том числе неорганизованных выбросов около 200 т/год. Установлено, что наиболее целесообразно утилизировать железосодержащие отходы, образующиеся отправляя их в агломерационное производство в качестве шихтовых материалов. - На основании литературных данных и проведенных исследований установлено, что источником выделения пыли на прокатном стане есть процесс деформации металла. Поэтому целесообразно организовать пылеподавления в рабочих клетях с целью предотвращения распространения пыли в цехе.
- На основании анализа технологии прокатки, работой предусмотрено две схемы пылеподавления: 1) в черновых и передчистових клетях предусмотрены форсунки для пылеподавления при выходе раската из клети; 2) для чистовой клети целесообразно предусмотреть установку форсунок, что позволяет одновременно обеспечивать и пылеподавления , и ускоренное охлаждение проката для повышения качественных свойств проката.
- Для разработки системы совмещения пылеподавления и ускоренного охлаждения разработана математическая модель и программа расчета технологических и конструктивных параметров установки.
- Для проектирования системы пылеподавления в черновых и передчистових клетях разработана математическая модель, что позволит определить конструктивные и кинематические параметры установки пылеподавления. Разработанная система пылеподавления предполагается использовать на всех станах горячей прокатки. С использованием разработанной программы выработаны теоретические исследования влияния изменения давления и расхода воды от размеров сечения камеры. Результаты данного исследования имеют практическое значение, поскольку позволяют выбрать оптимальное значение диаметра сопла форсунки при минимальном значении давления и минимальными возможными затратами воды. Это существенно уменьшит эксплуатационные расходы на обслуживание данной установки.
- . Использование радиального отстойника в качестве вторичных позволяет улавливать до 95% окалины, что существенно улучшает работу вторичных отстойников, а также снижает затраты на их обслуживание. В результате установки предлагаемой трехступенчатого очистки сточных вод прокатных цехов уменьшается вредное воздействие на водоемы.
- Анализ условий труда на прокатных станах показал, что основными вредными факторами на рабочих местах являются: шум, опыления и выделение тепла. После проведения системы пылеподавления условия труда вальцовщиков значительно улучшатся, так как опыление снизится в 3 - 4 раза.
- Экономический эффект от реализации данных мероприятий состоит из трех частей:
- Эффект от замены первичных шихтовых материалов вторичными, который составил 19,26 грн;
- Эффект от снижения выбросов пыли, который составил 5782 грн;
- Эффект от улучшения условий труда, который составил 192221,1 грн;
Суммарный экономический эффект составляет 198022,36 грн.
Список источников
- Андоньев С.М., Зайцев Ю.С., Филипьев О.В. Пылегазовые выбросы предприятий черной металлургии.– Харьков: Металлургия, 1989.– 247 с.
- Шабалин А.Ф. Очистка сточных вод предприятий черной металлургии.– М.: Металлургия, 1960.– 216 с.
- Защита водоемов от загрязнений сточными водами предприятий черной металлургии / Г.М. Левин, Г.С. Пантелят, И.А. Вайнштейн и др.– М.: Металлургия, 1978.–216 с.
- Красавцев Г.И., Ильичев Ю.И., Кашуба А.И. Рациональное использование и защита водных ресурсов черной металлургии.– М.: Металлургия, 1989.– 288 с.
- Толчко А.И., Славин В.И. Утилизация пылей и шламов в черной металлургии.– М.: Металлургия, 1990.– 145 с.
- Старк С.Б. Газоочистные аппараты и установки в металлургическом производстве.– М.: Металлургия, 1990.– 400 с.
- Бринза В.Н. Охрана труда в прокатном производстве.– М.: Металлургия, 1986.– 208с.
- Темнохуд В.А., Откидач В.В., Кравец В.А. Система технологического проектирования подавления неорганизованных пылевых выбросов в прокатных цехах // Совершенствование и разработка новых технологий и оборудование по охране окружающей среды: Сборник научных трудов.– Донецк: ОАО «Украинский научный центр технической экологии», 2000.– С. 99–105.
- Пажи Д.Г., Галустов В.С. Основы техники распыливания жидкостей.– М.: Химия, 1984.– 255 с.
- Денисенко Г.Ф. Охрана труда.– М.: Высшая школа, 1985.– 320 с.
- Методика визначення соціально-економічної ефективності заходів щодо поліпшення умов і охорони праці / ткачук К.Н., Лисюк М.О., Лучко І.А. та ін.– Київ: Основа, 1999.– 96 с.