Реферат за темою випускної роботи
Зміст
- Вступ
- 1.Актуальність теми
- 2. Мета і задачі дослідження та заплановані результати
- 3.Екологічна безпека при виробництві сортового прокату
- 3.1 Вплив прокатного виробництва на атмосферне повітря при виробництві сортового і листового прокату.
- 3.1.1 Технологічні викиди
- 3.1.2 Неорганізовані викиди
- 3.1.3 Утилізація окалини
- 4.Дослідження і розробка системи пилоподавлення сортового стана 250 ПрАТ «ДМЗ»
- 4.1Форсунки для подавлення неорганізованого пилу
- 4.2Утилізація замасленої окалини
- Висновки
- Перелік посилань
Вступ
Прокатне виробництво - одне з найбільших видів металургійного виробництва. У прокатних цехах обробляють приблизно 3/4 всього виплавленого металу. Технологічний процес отримання готових прокатних виробів є завершальною стадією металургійного виробництва. Різноманітність сортаменту прокатних виробів і складність умов пластичної та термічної обробки, а також обробка прокату визначають застосування в прокатних цехах потужного механічного, електричного і термічного обладнання. Експлуатація такого устаткування обумовлює необхідність створення безпечних, нешкідливих і зручних умов роботи для персоналу прокатних цехів.
1. Актуальність теми
сновною проблемою прокатних цехів є неорганізовані викиди пилу на ділянці прокатних станів. Ці викиди створюють велику запиленості повітря в цехах, що вкрай негативно впливає на здоров'я обслуговуючого персоналу, а також велика кількість пилу викидається через аераційні ліхтарі в навколишнє середовище.
Неорганізовані викиди вловлювати технічно неможливо, економічно невигідно. Тому в даній роботі акцентовано увагу саме на цю проблему. Проблема неорганізованих викидів актуальна подвійно: по-перше, з вирішенням цієї проблеми поліпшуються умови праці робітників і по-друге, покращиться екологічна обстановка.
2. Мета і задачі дослідження та заплановані результати
Мета роботи-розробити заходи щодо підвищення екологічної та технічної безпеки виробництва сортового прокату і оцінити їх вплив на навколишнє середовище.
Об'єкт дослідження span>: Сортове виробництво проектними цеху ПрАТ "ДМЗ"
Основні завдання дослідження:
- Збір інформаційних та експериментальних даних з питань, що стосуються придушення виділення пилу при прокатці, а також підготовки та утилізації замасленому окалини прокатного виробництва.
- Аналіз даних і розробка найбільш раціональної схеми утилізації замасленому окалини.
- Проведення промислових дослідів, що дозволяють визначити склад окалини, її властивості, температуру конденсації масла і т.д.
- Розробка математичної моделі системи пилоподавлення на прокатних станах.
- Розробка системи пилопригнічення для стану 250 ПАТ «ДМЗ»
- Розробка інформаційно-аналітичної системи для аналізу та оцінки екологічної та економічної ефективності від впровадження даної технології.
3.Екологічна безпека при виробництві сортового прокату
3.1 Вплив прокатного виробництва на атмосферне повітря при виробництві сортового і листового прокату.
У прокатному виробництві, як і в інших виробництвах, є організовані технологічні та неорганізовані викиди. Виробництво сортового і листового прокату супроводжується незначними викидами забруднюючих речовин в атмосферу. В даному виробництві, як і в інших виробництвах, є організовані технологічні та неорганізовані викиди. Основне джерело технологічних викидів - нагрівальні печі. Джерелом неорганізованих викидів: нагрівальні печі при недостатній тязі, робочі кліті, ножиці для різання металу, механічна зачистка заготовок [1]. з>
3.1.1 Технологічні викиди
Нагрівальні пристрої опалюються природним, коксовим, доменним газами та їх сумішшю. Кількість продуктів згоряння в нагрівальних печах та колодязях залежить від теплової роботи цих агрегатів і складає 700 - 1000 м 3 /т нагрівається металу. Оксиди сірки в продуктах горіння утворюються при використанні коксового і доменного газів. У разі використання в прокатному виробництві нетрадиційних штучних палив - конвертерних газів, очищених феросплавних, концентрація сірчистих газів в продуктах їх горіння збережеться приблизно на рівні 700 - 1000 мг/м3. При спалюванні природного газу в нагрівальних пристроях повітря практично не забруднюється. При спалюванні серосодержащего палива (мазуту, коксового та коксосодержащіх газів) в атмосферу надходить сірчистий ангідрит, кількість якого залежить від вмісту сірки в паливі і його витраті.
3.1.2 Неорганізовані викиди
При гарячої прокатки металу пил утворюється в результаті подрібнення окалини валками і випаровування внаслідок миттєвого збільшення тиску та підвищення температури в осередку деформації при прокатці. Кількість пилу, що виділяється на 1т прокату, становить при прокатці слябів і блюмів до 80 г / т, а при прокаті листа до 100 г / т. Частина пилу (~ 20%) мелкодисперсная (розмір часток <10 мкм) [1].
На блюмінгах і сортових станах найбільш інтенсивне пиловиділення відбувається в перших проходах. Кількість пилу збільшується з підвищенням швидкості прокатки і залежить від марки сталі і товщини прокатуваного розкату. Окремі вимірювання вмісту пилу в чистової кліті листопрокатного стану показали забруднення повітря в межах 400 - 100 мг / м ³ [1]. При недостатній тязі в димоходах нагрівальних печей в неорганізованих викидах, міститься окис вуглецю в кількості до 150 г / т прокату. Питомі викиди пилу в прокатних цехах блюмінга і слябінга становлять 50 г / т, через витяжні ліхтарі викидається 15% цієї кількості, тобто приблизно 11 г / т прокату, при цьому на частку відділення нагрівальних колодязів припадає 7 г / т, а на відділення підготовки - 4 г / т.
В процесі прокатки металу в валках і при його різанні на ножицях, а також при транспортуванні по рольганги окалина відділяється по поверхні заготовок і частково подрібнюється. Дрібні фракції у вигляді пилу захоплюються вихідні тепловими потоками. Частина цього пилу видаляється з цеху через витяжні отвори (близько 10 - 20%), а інша (близько 30 - 90%) осідає в приміщеннях цеху на будівельних конструкціях будівлі і устаткуванні. Розрахунки та дослідження показали, що загальна питома кількість пилу, який виділяється у відділенні прокатки, складає 30г / т прокочується металу. Неорганізовані викиди листопрокатних і великосортних цехів містять окис вуглецю і пил. Так, питома кількість пилу, що виділяється по цеху слябінга в цілому складає 50 + 30 = 80 г / т.
Загальна питома кількість окису вуглецю, що виділяється з пічного відділення при недосконалої конструкції пальникового пристроїв і недостатній тязі (вибивання газів з робочого простору), становить до 200 г / т прокату. Питомий кількість пилу, що виділяється через аераційні ліхтарі, складає в середньому до 16 г / т прокату і до 0,27 г / м2 площі прокатуваного листа. Загальна питома кількість пилу, що виділяється при прокатці металу, становить 100 г / т. [1]. Всі неорганізовані викиди з будівлі видаляються через аераційний ліхтар.
3.1.3 Утилізація окалини
У прокатних цехах металургійних підприємств основними відходами є: окалина первинних відстійників, окалина вторинних відстійників, відходи порізки металу, маслоотдходи.
Для організації ресурсозберігаючих технологій прокатного виробництва зазначені відходи повинні бути відповідним чином зібрані, підготовлені та відправлені споживачам. Наявність перерахованих відходів на конкретному підприємстві залежить від складу прокатних цехів, а також від виду продукції, що випускається, і її обробки. Не всі відходи знаходять повне застосування. Якщо окалина первинних відстійників використовується практично повністю, то використання вторинного окалини становить ¾.
4. Іccледованія і розробка системи пилоподавлення сортового стана 250 ПрАТ «ДМЗ»
При прокатці кількість пилу потрапляє в атмосферу, становить не менше 200 грам на тонну готового прокату, причому до 20% від цієї кількості становить мелкодисперсная окалина, найбільш небезпечна для людини. При створенні технологій нового якісного рівня, що забезпечують підвищення механічних властивостей прокату за рахунок поєднання в єдиному технологічному потоці стану операцій пластичної деформації і термічного зміцнення, була також поставлена задача істотного зниження шкідливих викидів в атмосферу цеху за рахунок придушення пилоутворення на виході з осередку деформації компактної струменем відпрацьованого охолоджувача.
У роботі передбачено дві схеми пилоподавлення.
- На клітях, де немає пристрою прискореного охолодження, передбачено встановити форсунки для придушення неорганізованого пилу, що утворюється при виході металу з калібру.
- На робочих клітях, на яких влаштовується пристрій прискореного охолодження, передбачено суміщення процесу охолодження з пиловиділенням.
4.1Форсункі для придушення неорганізованого пилу
Пил при роботі прокатних станів утворюється в результаті роздавлювання поверхневого шару металу при проході його через валки. На блюмінгах і слябінгів пил виділяється протягом всієї прокатки. На сортових станах з 11 - 12 проходами розкату при прокатці виділенням пилу супроводжується в більшості випадків 5 - 6 проходів, а на безперервних сортопрокатних станах пил виділяється при прокатці в чистових клітях, тому що у них метал проходить зі значно більшою швидкістю, ніж в чорнових. На листових станах гарячої прокатки пиловиділення супроводжує не тільки чисті, а й чорнові кліті. При цьому на чистових клітях пилу виділяється значно більше, ніж на чорнових. У невеликих клітей пил можна відсмоктувати через парасольку, встановлений на вихідній стороні кліті. Така система має серйозні недоліки. У зв'язку з тим, що відсмоктується вологий пил, димарі в ряді випадків швидко забиваються, і тому вимагають постійного догляду. Крім того, парасолі заважають обслуговування клітей. При знепилювання великих клітей доводиться відсмоктувати й очищати великі об'єми повітря. Враховуючи перераховані недоліки, проблему знепилювання на ряді станів намагалися вирішити застосуванням гідравлічного способу. Воду на кліті подавали через трубу, виконану у вигляді душовою сітки. Однак сила струменя виявилася слабкою. Для її посилення було підведено стиснене повітря. Пилення припинилося, однак виникли нові ускладнення - шум від стисненого повітря заважав працювати. Знепилювання із застосуванням стисненого повітря економічно невигідно, і при дефіциті стисненого повітря, воно не може бути використано на всіх клітях. Крім того, стиснене повітря створювало повітряний підпір під кліттю і виганяв в цех пил висохлу на стінах каналу для змиву окалини [7]. Найбільш надійним засобом знепилювання на станах гарячої прокатки є застосування гідрозмиву пилу в місці виходу прокату з валків. Даний спосіб не має недоліків, які притаманні способам, описаним вище. При збільшенні розмірів складній формі прокату потрібно подавати не одну, а кілька струменів води, причому таким чином, щоб пил змивався з усіх площин прокату. Для реалізації поставленої першого завдання розроблено алгоритм проектування форсунок. Передбачено форсунки струминного типу з конически росходящімся соплом, які подають потік води в зону виходу металу з робочого калібру. З використанням розробленої програми спроектована система пилопригнічення для умов роботи стану 250 ПрАТ «ДМЗ». На малюнку 4.1 показана схема розміщення основного обладнання та джерел викиду пилу в стані 250. За допомогою водопровідних труб буде подаватися вода з оборотного циклу водопостачання ПрАТ «ДМЗ». Ця вода прямує далі в форсунки. Форсунки створюють розпилення води, яка покриває джерела викиду пилу. Пил буде падати і направлятися разом з водою в подстановой тунель для подальшого очищення від окалини. На малюнку 4.1 можна бачити, яким чином буде проходити гідрозмив на кліті прокатного стану.
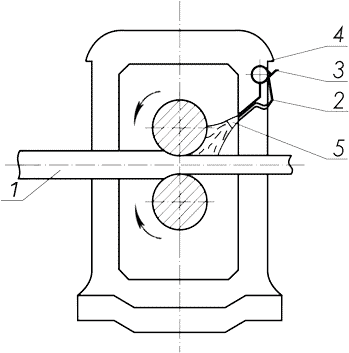
1 - прокат; 2 - гнучкий шланг, 3 - водопровідна труба, 4 - зсувний хомут, 5 - сопло.
Рисунок 4.1 - Схема системи гідрозмиву на кліті прокатного стану
За розробленою програмою отримані залежності роботи системи від різних конструктивних пристроїв. На малюнку 4.2 показана залежність витрати води на різні групи клітей стану 250 при різних діаметрах сопел. Графік дозволяє вибрати відповідний діаметр сопла і визначити витрату води на різних клітях, що спрощує вибір технологічних параметрів роботи системи пилоподавлення.
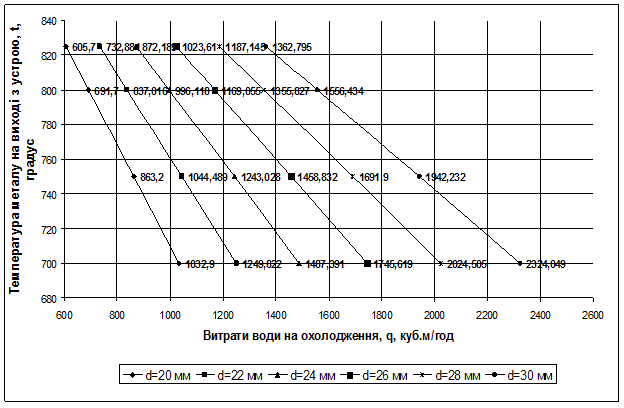
Рисунок 4.2 - Вибір необхідного витрати охолоджувача в залежності від діаметру охолоджуваного профілю.
4.2Утілізація замасленому окалини
Як вже було сказано вище, ідеєю магістерської роботи є розробка нової досконалої технології з утилізації замасленому окалини, яка є відходом металургійного виробництва та його цінною вторинною сировиною одночасно. Вміст заліза в ній становить близько 70%.
Перейдемо безпосередньо до даної проблеми. Існує два шляхи утилізації окалини: повернення її в металургійне виробництво або використання її в інших виробництвах (наприклад, в лакофарбовому).
засмальцьовану окалину важко підготувати до утилізації через підвищений вміст в ній масел, а в прокатних цехах металургійних підприємств утворюються великі кількості замасленому окалини, яка знаходить обмежене застосування і скидається в шламонакопичувачі.
Проблема утилізації замасленому окалини в даний час вирішується в основному в одному напрямку - знемаслення її з отриманням чистою, знежиреної, легко утилізованої окалини. Однак і хімічне і термічне знемаслення - дорогі процеси, що створюють додаткові екологічні ускладнення. В даний час практично всі утворюються дрібнодисперсні залізовмісні відходи утилізують у складі аглошихти.
Висновки
- На підставі даних, отриманих на ЗАТ «ДМЗ», визначено, що сумарна кількість відходів при виробництві сортового і листового прокату складає: окалини – біля 60 тис. т/рік, обрізь – більш 115 тис. т/рік, брухт чорних металів – понад 9 тис. т/рік, в тому числі неорганізованих викидів біля 200 т/рік. Встановлено, що найбільш доцільно утилізирувати залізовмісні відходи, що утворюються, відправляючи їх в агломераційне виробництво в якості шихтових матеріалів.
- . На підставі літературних даних проведених досліджень встановлено, що джерелом виділення пилу на прокатному стані є процес деформації металу. Тому доцільно організувати пилеподавлення в робочих клітях, з метою запобігання розповсюдження пилу в цеху.
- . На підставі аналізу технології прокатці, роботою передбачене дві схеми пилеподавлення: 1) в чорнових та передчистових клітях передбачені форсунки для пилеподавлення при виході розкату з кліті; 2) для чистової кліті доцільно передбачити установку форсунки, що дозволяє водночас забезпечувати і пилеподавлення і прискорене охолодження прокату для підвищення якісних властивостей прокату.
- Для розробки системи суміщення пилеподавлення і прискореного охолодження розроблена математична модель та програма розрахунку технологічних та конструктивних параметрів установки.
- Для проектування системи пилеподавлення в чорнових і передчистових клітях розроблена математична модель, що дозволить визначити конструктивні та кінематичні параметри установки пилеподавлення. Розроблену систему пилеподавлення передбачається використати на всіх станах гарячої прокатки. З використанням розробленої програми вироблені теоретичні дослідження впливу зміни тиску і витрат води від розмірів перетину камери. Результати даного дослідження мають практичне значення, бо дозволяють вибрати оптимальне значення діаметру сопла форсунки при мінімальному значенні тиску і мінімальними можливими витратами води. Це суттєво зменшить експлуатаційні видатки на обслуговування даної установки.
- . Використання радіального відстійника в якості вторинних дозволяє уловлювати до 95 % окалини, що суттєво покращує роботу вторинних відстійників, а також знижує витрати на їхнє обслуговування. У результаті установки пропонованої триступінчатого очищення стічних вод прокатних цехів зменшується шкідливий вплив на водойми.
- Аналіз умов праці на прокатних станах показав, що основними шкідливими чинниками на робочих місцях є: шум, запилення та виділення тепла. Після проведення системи пилеподавлення умови праці вальцювальників значно покращаться, так як запилення знизиться в 3 – 4 рази.
- . Економічний ефект від реалізації даних заходів складається з трьох складників:
– ефект від заміни первинних шихтових матеріалів вторинними, який склав 19,26 грн;
– ефект від зниження викидів пилу, який склав 5782 грн;
– ефект від поліпшення умов праці, який склав 192221,1грн;
Сумарний економічний ефект складає 198022,36 грн.
Список источников
- Андоньев С.М., Зайцев Ю.С., Филипьев О.В. Пылегазовые выбросы предприятий черной металлургии.– Харьков: Металлургия, 1989.– 247 с.
- Шабалин А.Ф. Очистка сточных вод предприятий черной металлургии.– М.: Металлургия, 1960.– 216 с.
- Защита водоемов от загрязнений сточными водами предприятий черной металлургии / Г.М. Левин, Г.С. Пантелят, И.А. Вайнштейн и др.– М.: Металлургия, 1978.–216 с.
- Красавцев Г.И., Ильичев Ю.И., Кашуба А.И. Рациональное использование и защита водных ресурсов черной металлургии.– М.: Металлургия, 1989.– 288 с.
- Толчко А.И., Славин В.И. Утилизация пылей и шламов в черной металлургии.– М.: Металлургия, 1990.– 145 с.
- Старк С.Б. Газоочистные аппараты и установки в металлургическом производстве.– М.: Металлургия, 1990.– 400 с.
- Бринза В.Н. Охрана труда в прокатном производстве.– М.: Металлургия, 1986.– 208с.
- Темнохуд В.А., Откидач В.В., Кравец В.А. Система технологического проектирования подавления неорганизованных пылевых выбросов в прокатных цехах // Совершенствование и разработка новых технологий и оборудование по охране окружающей среды: Сборник научных трудов.– Донецк: ОАО «Украинский научный центр технической экологии», 2000.– С. 99–105.
- Пажи Д.Г., Галустов В.С. Основы техники распыливания жидкостей.– М.: Химия, 1984.– 255 с.
- Денисенко Г.Ф. Охрана труда.– М.: Высшая школа, 1985.– 320 с.
- Методика визначення соціально-економічної ефективності заходів щодо поліпшення умов і охорони праці / ткачук К.Н., Лисюк М.О., Лучко І.А. та ін.– Київ: Основа, 1999.– 96 с.